Electrification Is Increasingly Being Mentioned In Discussions Around The Decarbonization Of Cement.
By Jonathan Rowland
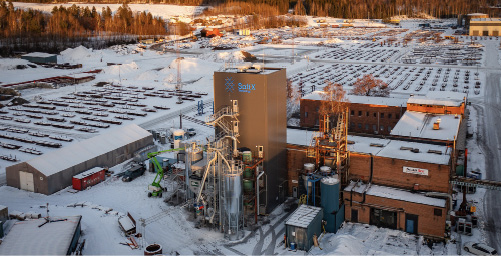
Electrification of process heat is still very much in the nascent stages of development in the cement industry. It’s not without interest, however. According to the experts at the European Cement Research Academy (ECRA), electrification of cement production “appears promising.” Researchers Sebastian Quevedo Parra and Mattero Romana of the Politecnico di Milano agree. In a 2023 paper entitled ‘Decarbonizing of cement production by electrification’, they called electrification “an interesting option to reduce the CO2 generated from fuel combustion”
Published in the Journal of Cleaner Production, that paper was at least partially funded by the Global Cement and Concrete Association’s (GCCA), Innovandi Global Cement and Concrete Research Network. This includes kiln electrification as one of its core projects, although in the GCCA’s roadmap to next zero, kiln electrification is forecast to play only a small role, and this from 2040, Claude Loréa, the association’s cement, innovation, and ESG director, told Cement Products.
There are also challenges to electrification beyond the simply technical. As the Politecnico di Milano researchers continued, electrification will rely on “access to low-cost and low-carbon electricity”. And then there are issues around grid capacity, eloquently highlighted by Rick Bohan of the Portland Cement Association in a recent interview with Cement Products. “Before we see a fully electric cement plant,” Bohan argued, “we need to make sure the grid is in place with sufficient capacity to ensure that, when we press the on-switch, we are not going to cause brownouts or shortages elsewhere.” This may all be cause for caution when it comes to electrification. But that is not stopping several companies and research projects pursuing the issue. In the US, EPIXC – Electrified Processes for Industry without Carbon – is aiming to develop the technologies and workforce required to replace fossil fuel-based heating with electric heating in industry, including cement production.
The cement side brings together researchers from Arizona State University, the University of Texas Austin, and the Missouri University of Science and Technology, as well as cement producers, CEMEX and CRH (Ashgrove Cement), to “develop electrified technologies for subprocesses of cement manufacturing,” Arizona State’s Prof. Narayanan Neithalath, told Cement Products. “Several technologies are under consideration, including the use of electrical resistance-based heating technologies, plasma-assisted heating, and microwave heating.”
The project has a timeframe of five years for initial technology development, plus another three to five years for further development and demonstration. “We are starting our first phase of projects on these topics on our new cement test bed,” continued Neithalath. “The idea is to translate potential technologies for scale up. Both existing cement manufacturers and new technology partners are collaborating with the institute.”
Coolbrook’s RotoDynamic Heater
One company already working to prove their electrification technology at industrial scale is Coolbrook with its RotoDynamic Heater (RDH) technology. “The RDH uses a multi-step process that rapidly accelerates and decelerates gas, e.g., air, across several stages that feed into each other to generate temperatures up to 1700°C within milliseconds,” Coolbrook told Cement Products. “Typically, a traditional turbine converts the kinetic energy of a fluid or a gas into motion via rotating blades. Our technology, however, uses renewable electricity to spin the blades instead, reversing the process and generating substantial heat.”
Coolbrook successfully completed pilot testing in September 2023. “Our testing demonstrated the technical viability and ability of the technology to generate the temperatures required for heavy industrial production,” the company said. “The tests also validated our technical pathway up to 1700°C, covering more than 95% of the temperature range needed by the more than $1 trillion industrial heating market. We are now partnering with leading industrial manufacturers across heavy industries, with deployment of the RDH technology at client sites this year and full commercial rollout expected to start around 2025.”
Among these partnerships are a number with leading cement producers, including CEMEX and India’s UltraTech Cement and JSW. “We are actively working with our partners in the cement industry on assessing our technology and planning its implementation in the cement manufacturing process,” the company continued.
According to Coolbrook, its technology offers the cement industry “more than the elimination of fossil fuels.” The RotoDynamic Heater is 90% to 95% energy efficiency and compact, allowing “seamless and easy retrofitting into existing cement kilns, without complicating the existing infrastructure”. It can also support other decarbonization levers such as alternative fuels and carbon capture.
“Cement industry decarbonization will likely utilize several technologies and solutions, combining technologies like electric heating, carbon capture, and alternative fuels,” concluded the company. “Our RDH technology can support the use of alternative fuels, e.g., by providing additional hot combustion air. But eventually, all CO2 must be captured or abated, and alternative fuels produce CO2 emissions in similar fashion to fossil fuels. We therefore think that, in the long term, a combination of electric heating, such as the RDH technology, and carbon capture for the process carbon emissions will be a winning combination.”
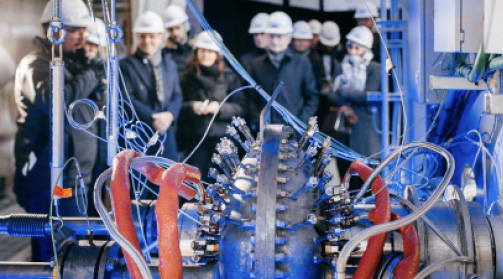
Plasma Heating and SaltX’s Electric Arc Calciner
Plasma heating involves the passing of electricity into a flowing gas to generate a hot beam of ionized plasma. Heat transfer to the product is “mainly achieved by convection and can be influenced by manipulating gas type and flow”, explained ECRA researchers in their 2022 Technology Paper 19: Electrification, plasma, and other technologies. Several research projects have considered plasma heating in the cement kiln. This includes the CemZero project, initiated by Vattenfall and Cementa in 2017, which concluded that “the concept of using plasma generators in a pre-heater, pre-calciner system is, at present, the main technology path for future development.”
Plasma technology has also been taken-up commercially by Swedish company, SaltX, with its electric arc calciner (EAC). Originally developed for the production of quicklime, SaltX has demonstrated the production of clinker in the EAC “with the same clinker mineral characteristics as conventional clinker,” the company said in a 2023 press release, quoting a specialist from cement and concrete chemistry consultancy, WHD Microanalysis, who analysed the material.
The company signed a collaboration agreement in 2023 with leading Indian cement producer, Dalmia Cement, to incorporate the EAC at one of Dalmia’s existing cement plants. It also announced the extension of an existing partnership with process automation giant, ABB, who will provide control and electrical systems for the EAC, as well as taking a minority stake in the company.
Induction, Microwave And Resistive Heating
Other options highlighted by ECRA researchers in their technology paper include induction, microwave, and resistive heating, although there are challenges to each of these that may impede their applicability to cement production.
- In induction systems, heat is the product of resistance to electrical currents (eddy currents), which are produced within the object to be heated by a rapidly alternating magnetic field. However, it requires that the material be electro-conductive, which cement raw meal is not – or at least not enough to allow direct induction. To apply induction heating to cement production, the heat would therefore have to be transferred indirectly through heat exchange from a conductive and magnetic material.
- Microwave heating involves the transmission of heat via microwave radiation into the material to be heated. But as the ECRA researchers point out, “cement raw material has very poor microwave absorbing capacity. Quartz in particular is transparent to microwaves at low temperatures. Therefore, microwave heating of cement raw meal is very inefficient.”
Resistive heating also relies on an object’s resistance to an electric current to generate heat, in this case, a specific resistive element. Heat can then be transferred to the meal or process gas either by convection of the gas, or indirectly through conduction and radiation. The challenge here, as noted by ECRA, is the availability of materials able to withstand the operating conditions within the cement kiln (i.e. high temperature, an oxidizing and dusty atmosphere).
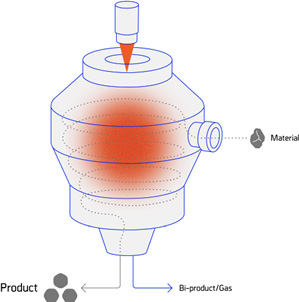
Cambridge Electric Cement
Cambridge Electric Cement is a novel approach to the electrification of cement that integrates cement production with the production of steel in an electric arc furnace (EAF). The process is premised on the fact that spent cement powder from concrete waste has a similar composition to the slag used in the EAF process.
The Cambridge Electric Cement process uses this cement powder instead of the traditional lime-flux to form slag in the EAF. The high temperatures involved in the steelmaking process, however, also reactivate the cement. When the steel is tapped off, the slag is cooled rapidly in air, and ground to a powder, which “has the chemical composition of clinker made with today’s process,” according to the project website.
“We have shown the high temperatures in the furnace reactivate the old cement and, because electric arc furnaces use electricity, they can be powered by renewable power, so the entire cement-making process is decarbonized,” lead scientist on the project, Cyrille Durant, told the BBC in a recent interview. The process was due to be tested in May at a full industrial-scale EAF owned by steelmaker, Celsa, in Cardiff, Wales, with results yet to be released at the time of writing.
Leilac Project, Electrification And Carbon Capture
Another project to note is the Leilac – Low Emissions Intensity Lime and Cement – project, now into its second phase and working toward a demonstration facility at Heidelberg Materials’ Ennigerloh cement plant in Germany. The Leilac technology re-engineers the traditional calciner to separate combustion exhaust gases from the process CO2 emissions released during calcination. These process emissions have a very high concentration of CO2, which can be efficiently captured without additional chemicals, solvents, or processes.
The technology achieves this separation by utilizing a tube reactor, which is indirectly heated to power the calcination reaction. This allows “high flexibility on heating sources, including electricity and alternative fuels,” the project noted in a 2023 techno-economic analysis. After a successful first phase, which demonstrated the ability of the technology to calcine both cement raw meal and limestone, a second phase of the project will see the commissioning of a multi-tube reactor at Ennigerloh, taking 20% of the total kiln feed.
The Leilac project also points to a potential knock-on benefit of electrification, as the European Commission noted in its factsheet on deep decarbonization options for the cement industry. “Electrified heating systems [produce] much higher concentrations of CO2 in the flue gases than with combustion heating, from an estimated 25% CO2 concentration, to close to 100%,” wrote the factsheet authors. “This would allow easier capture and purification of CO2 from process emissions.”
Electric Calcined Clay: the ECoClay Project
Calcined clay has received much attention in recent years as a lower-carbon alternative cementitious material to clinker. Current clay calcination processes product a highly reactive clay, allowing cement producers to replace up to 30% of the clinker in cement, and resulting in 40% lower CO2 emissions per tonne of cement, according to FLSmidth Cement. However, the process still relies on combustion of fuels (either conventional or alternative) to generate heat.
Led by FLSmidth Cement, the ECoClay project is looking into the potential of electrifying the clay calcination process. Project partners include cement producers, VICAT and Cementos Argos, as well as researchers from the Danish Technological Institute and Technical University of Denmark, and U.S.-based industrial heating expert, Rondo Energy.
According to Rondo Energy’s CEO, John O’Donnell, the company’s Rondo Heat Battery technology “captures intermittent renewable electricity and stores it for delivery as continuous high-temperature industrial-scale heat.” The system uses electric heating elements – such as those in a toaster or oven – to heat bricks and store thermal energy, with very low losses of less than 1% per day, according to the company’s website. When heat is needed, air flows through the brick stack and is superheated to over 1000°C with outlet heat delivered at the desired temperatures via automated controls. Air is eventually recycled back into the system, minimizing heat loss and maximizing efficiency.
Calcined clay “has no intrinsic process emissions; by replacing the fuel combustion powering the calcination process with renewable electricity, the EcoClay partnership will deliver prompt, practical, low-cost emissions reductions at scale – and can build the foundation for true-zero cement,” concluded O’Donnell.
Is the Future Electrified
What extent will electrification play a part in the cement industry of the future? It’s too soon to say, is the short answer. But interest is growing, although significant challenges remain. Ultimately – and as always when it comes to decarbonization of cement and other industries – there is no panacea. Decarbonization will rely on an evolving mix of technologies. Electrification may well be one of those; however, in order to so, it will require a sufficient quantity of low-carbon, low-cost electricity, as well as grid capacity capable of handling the increased loads associated with industrial electrification.