Research, Benchmarks and Plant Projects are Ongoing As The Industry Tackles Sustainability Challenges.
By Mark S. Kuhar
Whether it is Carbon Capture, Utilization and Storage; Climate and Energy Benchmarking; or innovative developments at the plant level, the cement industry is continuously working to reduce its carbon footprint. Here are some of the latest developments.
CCUS Opportunities in the Cement Industry
According to a MIT CSHub Research Brief written by Elizabeth Moore, Hessam AzariJafari, Randolph Kirchain, Erin Middleton, Richard Middleton, Kat Sale, Qasim Mehdi and Marcos Miranda, Carbon Capture, Utilization and Storage (CCUS) will play a key role in the decarbonization of the cement industry.
Eventually, some of this captured carbon will be converted into valuable products that can be shipped like any other good. Today, subsurface mineralization (e.g., CO2 injection through wells or under water) is gaining traction because of efficiency and technological flexibility. However, most cement facilities in the U.S. are not co-located with suitably deep geologic CO2 storage. As a result, to support CCUS at scale, a CO2 transportation system will be needed. To be cost effective, this will require the buildout of an extensive carbon pipeline system.
While pipeline transportation is the most efficient transport option, there are challenges in designing the system. To inform the diameter and length of the pipeline system, sufficient information about the location of CO2 sources and sinks and estimates of maximum annual flow is needed.
An economical pipeline design must also consider environmental and regulatory factors such as rights-of-way regulations as well as avoidance of mountains, tribal and federal lands, and highly populated areas.
Various studies have provided estimates for the magnitude of pipeline scale and investment required for U.S. decarbonization. The results are sensitive to assumptions of pipeline diameter, calculations for CO2 mass flow rate, and assumptions of suitable storage locations.
The reported pipeline distances range from 70,000 km to 200,000 km. These studies assume that all types of carbon-emitting facilities are equally motivated to invest in and implement carbon capture. Clearly, carbon transport costs would be minimized if every emitting firm shared in that cost.
However, real-world market pressures and constraints do not align with the assumption that all firms will participate. Different industries have different timelines for achieving carbon neutrality at regional and national levels. As shown in the Portland Cement Association’s (PCA) Roadmap to Carbon Neutrality, the cement industry will not wait for all stakeholders to be motivated to decarbonize.
The study explores the design of a transport network to serve the cement industry and how that network would enable carbon capture across a much larger swath of the economy. Specifically, geospatial optimization is used to design pipelines and CCUS deployment scenarios to abate various fractions of cement industry emissions. These pipeline designs were then used to identify potential carbon hubs – collections of nearby industrial facilities which could attach to and make use of this pipeline at little cost.
Key Takeaways
- Carbon capture, utilization and storage (CCUS) will play a key role in the decarbonization of the cement industry. Spatial economic models can help inform cost-effective deployment strategies for carbon capture at cement facilities.
- Carbon capture equipment installed at the plant represents on average 80% of the total CCUS system cost for cement facilities. (The balance being for carbon transport and storage facilities.)
- At plant capture costs can vary by about 50% for cement facilities depending on the presence of pre- treatment facilities, air-in leakage, fuel types, and kiln type.
- There is a need to identify gaps between current cost model estimates and real-world demonstration costs.
- Spatial-economic analysis identifies optimal cement source, pipeline routing, and sink locations with total pipeline length ranging from 247-6,864 km to abate 15% – 85% of the cement industry’s emissions.
- If the cement industry leads industrial CCUS deployment, spatial analysis can identify carbon-hubs made of the nearest industrial neighbors to the pipeline to significantly reduce systems costs.
- In the 85% abatement scenario, carbon hubs could enable capture from ~100 additional industrial sources capturing 5X the emissions for 2X the infrastructure investment.
- This information can be used to help policymakers understand what incentives are needed to enable widespread industrial CCUS adoption.
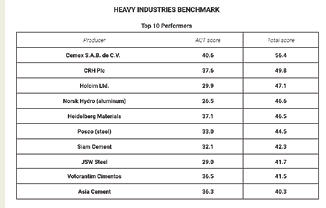
Transition (ACT), Core Social Indicator
and Just Transition figures in World
Benchmarking Alliance surveys and analyses.
Panel Measures Cement Industry’s CCUS Infancy, Future
A PCA panel on CCUS offered 2024 IEEE-IAS/PCA Cement Industry Conference participants updates on process technologies, IRS 45Q Carbon Oxide Sequestration Credits, private or public capital expenditure funding mechanisms, and carbon dioxide emissions management studies or projects for Central Plains Cement Co., Heidelberg Materials North America and Holcim US.
Heidelberg Materials Vice President, Environment & Sustainability Greg Ronczka reviewed the extensive preliminaries leading to a recent Department of Energy (DOE) action enabling the producer to negotiate a $500 million grant for a carbon capture facility at its recently rebuilt Mitchell, Ind., cement plant. While that figure might seem high, he noted, the grant, along with 45Q credits, amount to about half the investment envisioned for infrastructure to capture, refine and store up to 2 million mtpy of Mitchell Plant CO2 emissions. Even with the prospective DOE capex support and IRS allowances, the $1 billion-plus project “is still a challenge when you look at a long-term business expense,” Ronczka assured.
Panelist Kevin Lauzze of Sargent & Lundy, Chicago-based power and energy engineering specialist and a contractor on early Heidelberg CCS work, noted how the Mitchell site checks key boxes for a viable project: Plant exhaust with high purity CO2; adequate parcel for capturing, processing and delivery equipment; power and water access; and, a CO2 destination. To the latter point, southwest Indiana geological surveys suggest candidate storage area 7,000 ft. directly below the Mitchell plant footprint.
Sargent & Lundy also participated in a DOE-backed CCS pilot in the works at Eagle Materials’ Central Plains plant in Sugar Creek, Mo. The project will test the cryogenic CO2 capture technology of Salt Lake City-based Sustainable Energy Solutions. Panelist and SES President Andrew Baxter briefed the IEEE-IAC/PCA gathering on the basics of the 30-tpd demonstration at Central Plains. Scheduled for testing later this year, the infrastructure will cool calciner exhaust to isolate and liquify the CO2, then recover energy through heat exchange.
Rounding out the panel was Florian Gautier, director of Energy Transition for Large Industries at Paris-based Air Liquide. He reflected on his company’s Cryocap processing, where – like Sustainable Energy Solutions’ method – CO2 is cooled and liquified for delivery to storage or industrial use points. He discussed the Cryocap method in relation to a 2021 CCS feasibility study for the Holcim US Ste. Genevieve plant in Missouri.
Moderating the CCUS Panel was BloombergNEF Industrial Decarbonization Specialist Dr. Julia Attwood, returning to her role from a PCA and Global Cement and Concrete Association panel at 2023 Climate Week New York.
Joining moderator Dr. Julia Attwood, from left, Sustainable Energy Solutions’ Andrew Baxter, Air Liquide’s Florian Gautier, Sargent & Lundy’s Kevin Lauzze and Heidelberg Materials’ Greg Ronczka.
Cement Producers Dominate Heavy Industries Benchmark CO2 Reduction Survey
World Benchmarking Alliance’s (WBA) inaugural Heavy Industries Benchmark ranks 34 cement, 45 steel and 12 aluminum producers on carbon dioxide emissions reduction metrics. Four of the top five are cement producers Cemex, CRH, Holcim and Heidelberg Materials, all with major North American market positions.
Three other multinationals – Votoratim Cimentos, Asia Cement and Siam Cement – along with one aluminum and two steel producers round out the 2024 Heavy Industries Benchmark top 10.
The rankings are based on scores up to 100 of Accelerated Climate Transition (ACT) criteria, plus smaller Core Social Indicator and Just Transition data. ACT assessments emphasize actual CO2 emissions reduction performance against published targets; energy efficiency measures; low-carbon energy or electricity generation and consumption; and trend in future emissions intensity of own production or sold products.
Cemex tops the Heavy Industries ranking and ACT scoring. Heavy Industries, Electric Utilities, Oil and Gas, Buildings, Transport and Automotive comprise the WBA Climate and Energy Benchmark survey, which encompasses 450 companies across the globe.
“We are proud to achieve the highest score in the 2024 Climate and Energy Benchmark ranking, demonstrating our leadership in climate action and social impact,” said Cemex CEO Fernando González. “We are committed to achieving our ambitious 2030 decarbonization goals on the path to becoming a net-zero company by 2050, while making a positive and lasting difference in our communities.” Since the launch of its Future in Action program in 2020, he adds, Cemex has achieved record-breaking progress, reducing (GHG Protocol-defined) Scope 1 and 2 emissions by 13% and 10%, respectively – a pace that previously would have taken Cemex cement, concrete and aggregate operations 15 years to accomplish.
Despite the performance of Cemex and its global or multinational peers, WBA researchers contend that cement, steel and aluminum production emissions intensities need to fall three times faster in the next five years in order for Heavy Industries to align with widely adopted CO2 emissions reduction goals equating to a global temperature gain capped at 1.5°C by 2100. Upon releasing the Heavy Industries Benchmark ranking, WBA noted that cement, steel and aluminum “have new and innovative technologies available that can lead companies towards a low carbon future, but investments in research & development for market-ready technologies is insufficient. Of the companies assessed, 24% disclose R&D expenditure in low-carbon technologies, and just 10% in non-mature technologies.”
Total scores reflect Advanced Climate Transition (ACT), Core Social Indicator and Just Transition figures in World Benchmarking Alliance surveys and analyses.
Cement Plant CO2 Emissions Stay Their Flat Course in EPA GHG Inventory
The latest Environmental Protection Agency (EPA) Inventory of U.S. Greenhouse Gas Emissions and Sinks, presenting a national-level overview of annual greenhouse gas emissions from 1990 forward, cites 2022 GHG emissions of 5.489 billion metric tons (Gt) of carbon dioxide equivalent, a 1.3% increase from the prior year.
The GHG Inventory factors emissions of CO2, methane, nitrous oxide, hydrofluorocarbons, perfluorocarbons, sulfur hexafluoride and nitrogen trifluoride – all pegged for their global warming potential when released to the atmosphere.
Actual CO2 emissions in 2022 climbed just over 5 Gt, of which 41.9 million metric tons (Mt), or 0.008%, involved U.S. cement plants’ 80.5 Mt of clinker production. Combustion in cement calcining and kiln phases accounts for nearly a quarter of the 168.9 Mt of CO2 emissions in the GHG Inventory Industrial Products and Product Use (IPPU) chapter. Additional CO2 emissions attributable to the generation of electricity consumed in processing and finishing clinker and cement are pooled in the GHG Inventory Energy chapter. Under Energy, IPPU accounts for just over 800 Mt of CO2 emissions, tallied from iron & steel, petrochemical plus specialty chemical or metallic compound production, along with cement.
“Through a rigorous development and review process, EPA annually refines and strengthens our inventory, producing a comprehensive tally of U.S. greenhouse gas emissions and sinks,” said Assistant Administrator for the Office of Air and Radiation Joseph Goffman. “Reflecting input from hundreds of experts across the government, academia, industry, and consulting, the GHG Inventory report is a model for high-quality and transparent national GHG accounting.”
The agency has published the GHG Inventory as an impartial, policy neutral report since 1993, he added, submitting it to the United Nations Framework Convention on Climate Change.
MHI, Kiewit to Deliver Carbon Capture Tech for Heidelberg Project
As part of its procurement process for its Edmonton carbon capture, utilization and storage (CCUS) project, Heidelberg Materials has awarded MHI-LCSC, a division of Mitsubishi Heavy Industries Group, and Kiewit Energy Group a front-end engineering design (FEED) contract for carbon capture technology.
The FEED study will leverage MHI’s proprietary Advanced KM CDR Process developed jointly with Kansai Electric Power, which uses the KS-21 solvent.
“We are pleased with this latest step in advancing our Edmonton project and moving even closer to our goal of delivering the first full-scale application of CCUS in the cement sector,” said Joerg Nixdorf, vice president cement operations, Northwest Region for Heidelberg Materials North America. “This latest development represents meaningful progress on the path to achieving a net-zero future.”
The Edmonton plant could eventually capture and store an estimated 1 million metric tons of carbon dioxide each year, which is the equivalent of taking 220,000 cars off the road annually.
Cemex, MPP to Accelerate Decarbonization Effort
Cemex and the Mission Possible Partnership (MPP), in partnership with the Bezos Earth Fund, are collaborating to conduct an analysis of the potential of decarbonization levers at Cemex’s Balcones cement plant in Texas.
“Our collaboration with the Mission Possible Partnership represents a joint effort seeking to accelerate our sustainable commitments and comprehensively evaluate the extent to which we can utilize decarbonization levers within a specific plant ecosystem,” said Fernando A. González, CEO of Cemex. “This involves leveraging scalable technologies that would contribute to achieving our ambitious decarbonization goals on the path to becoming a net-zero company by 2050.”
MPP is assisting Cemex in evaluating various technological pathways to decarbonize the production process, including the use of alternative fuels, incorporation of lower-carbon materials, carbon capture and storage, and the utilization of captured carbon to produce synthetic fuels, chemicals or construction materials.
Having created a series of transition strategies for reaching net-zero emissions in hard-to-abate industries, MPP is orchestrating collaboration with an expanding network of partners to enable commercial-scale deep decarbonization projects.
Fortera Opens First Industrial Green Cement Plant
Fortera has formally commenced low-carbon ReAct cement processing at its ReCarb facility, adjacent to CalPortland’s Redding, Calif., cement plant. It is North America’s first industrial green cement and carbon dioxide mineralization facility and one of the largest of its kind in the world.
The Redding ReCarb Plant is equipped for annual capture of 6,600 tons of carbon dioxide from a flue stack serving the CalPortland plant and production of 15,000 tons of ReAct powder. Fortera anticipates deliveries later this quarter – likely supersacks for starters – to concrete producers, who can use ReAct as a supplementary cementitious material in blended binders, or as a full portland cement replacement.
“Redding is the first of many plants in Fortera’s future as a green cement producer, and achieving this milestone brings the industry that much closer to realizing zero-carbon cement, which is critical for both our continued infrastructure and the health of our planet,” said Fortera CEO Ryan Gilliam. “While significant, we recognize this is one step in a much larger effort to reach commercialization globally, and we are committed to scaling our technology using existing infrastructure to mobilize widespread adoption of low and zero-carbon cement.”
On a ton-for-ton basis against portland cement, Fortera measures a 70% reduction in carbon emissions tied to ReAct, whose main compound is a rare form of calcium carbonate. ReAct testing and field concrete demonstration candidates include CalPortland ready mixed operations and Vulcan Materials’ Central Concrete Supply business.
ReCarb technology reduces carbon emissions throughout the value chain without imposing substantial capital costs and creates a product that is just as effective as ordinary cement, noted Fortera. ReCarb also increases overall product output: When limestone is heated in a kiln to make ordinary cement, nearly half is lost as CO2. Mineralizing calcining phase emissions through ReCarb yields a ton of green cement for every ton of limestone feedstock used. Further, ReCarb reduces energy consumption by using a lower kiln temperature and creates a path to zero CO2 cement when processed with renewable energy-powered equipment.
SOLAR POWER TO GIVE CEMEX PLANT A BOOST
Cemex USA announced an off-site renewable energy agreement with Georgia Power for its Clinchfield cement plant as the producer increases its decarbonization efforts.
“Embracing solar power not only accelerates our own aggressive sustainability goals but also sets a powerful example for the entire industry,” said Ernesto Felix, Cemex US senior vice president, cement operations and technical. “By integrating renewable energy solutions through Georgia Power, Cemex paves the way for a greener, more resilient future for generations to come.”
Through this long-term agreement, the Clinchfield plant will secure 25% of its power requirements from solar facilities throughout Georgia beginning next year. Cemex expects the solar-generated power to offset about 10,000 metric tons of indirect CO2 emissions per year.
The company has a 2030 Scope 2 goal of reducing indirect electricity GHG emissions in cement operations by 58% from a 2020 baseline.