When Bulk Handlers Need Help Reducing Dust At The Conveyor Discharge Point, They Need Answers Fast.
Edited by Mark S. Kuhar
Every day, bulk handlers struggle with the conveyor discharge zone emitting dust, carryback, and spillage, some of the leading problems that cause equipment breakdowns, workplace safety violations and raise the cost of operation. Martin Engineering’s decades of research and development have resulted in some practical methods and innovative equipment that bulk handlers can apply to help reduce dust at the conveyor discharge point.
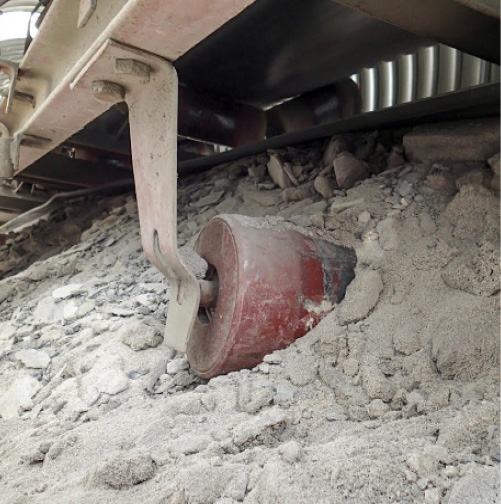
Dishonorable Discharge
Controlling conveyor discharge is, first and foremost, a workplace safety and compliance issue due to dust emissions. Nearly 90% of the earth’s crust contains silica, so one of the most highly regulated particulate emissions of any bulk handling material is Respirable Crystalline Silica (RCS).
Prevalent in limestone, coal and other raw material, RCS has been linked to several chronic lung diseases. The fact that particle sizes for the substance are tested in micrometers (1 thousandth of a millimeter) and volumes are monitored in micrograms (1 millionth of a gram) makes controlling the fugitive RCS a significant challenge.
Fugitive materials at the discharge zone of a conveyor belt are generally categorized into: dust, carryback and spillage.
- Dust is not just a health hazard but can get into roller bearing, greased machinery and equipment air intakes, causing breakage and downtime.
- Carryback is fine material that sticks to the belt surface or becomes lodged in the cracks and crevices of the belt and releases upon return causing excessive dust down the entire length of the system.
- Spillage is cargo that escapes the belt and accumulates around the discharge zone encapsulating rollers and the belt, cluttering walkways which limits access and increases labor costs for cleanup.
Adequately controlling the flow of conveyed material is not only efficient but maximizes production and lowers the cost of operation. In addition, it helps producers remain compliant for the safety of workers and the community.
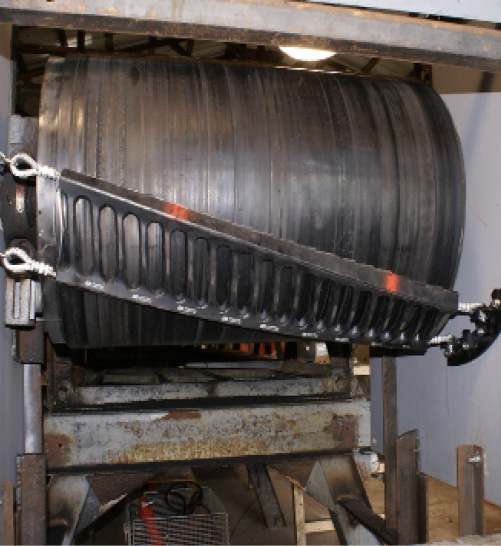
Belt Cleaning Methods
In the past, belt cleaners were rigid, linear pieces of hardware made out of various materials from brick to plastic with low operational life that frequently contributed to belt wear.
Modern primary cleaners like the Martin QC1+ Cleaner HD are mounted at the head pulley and usually made from engineered polyurethane. This specially formulated material is forgiving to the belt and splice, but still highly effective for dislodging cargo. Typically supported by mechanical or pneumatic tensioners, the designs require significantly less monitoring and maintenance of blade tension.
One primary cleaner design requires no tensioning at all after installation. The CleanScrape Primary Cleaner features a matrix of tungsten carbide scrapers installed diagonally to form a 3-dimensional curve around the head pulley and typically delivers up to four times the service life of urethane cleaners without needing re-tensioning.
As conveyor speeds and cargo volumes increase to meet production demands, secondary belt scrapers like the Martin SQC2S Secondary Cleaner are often installed immediately after the belt leaves the head pulley to address dust and fines that escape the primary cleaner.
Generally equipped with spring or air tensioners that easily adjust to fluctuations in the belt, secondary cleaners are particularly efficient for applications that produce wet, tacky or dusty carryback.
The CleanScrape Secondary Cleaner takes a different approach from the standard secondary cleaner. t features independent 6-inch-wide blades with carbide tips set on a stainless-steel assembly.
Each tip is supported on spring-loaded arms at both ends with a wide range of motion that provides equal load pressure across each blade and requires less re-tensioning over its lifespan. This design absorbs obstructions, responds to belt fluctuations, and is able to arc safely in the event of a belt rollback.

Conclusion
When fines are allowed to cling to the return side of the belt, suddenly dust can be detected along the entire length of the system. Spillage beneath the system is exposed to wind and adds to the dust. These fugitive emissions can cost coal terminals in violations and potential lawsuits.
Innovations in both blade design and tensioner engineering have improved cleaning ability, increased equipment life, reduced the need for tensioning and blade changes, and decreased labor for maintenance and cleanup. Along with lowering the cost of operation, the most noticeable change is less dust along the belt path and in work areas. This improves employee morale and retention and results in better compliance.
Martin Engineering has been a global leader in bulk material handling for more than 80 years, continuously developing new solutions to make high-volume conveyors cleaner, safer and more productive. All photos copyright Martin Engineering 2024.
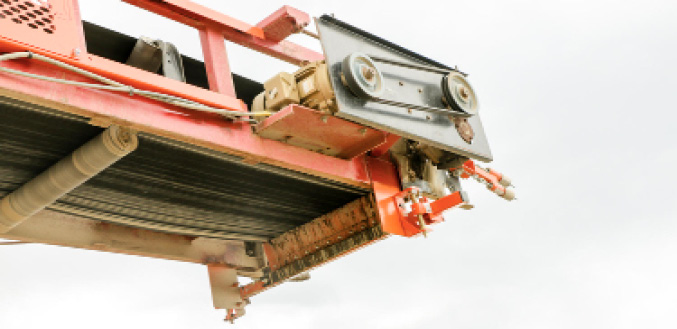