By Mauro Nogarin
Argentina and Peru have confirmed important investments in the cement industry, with the aim of diversifying the supply of products to strengthen the construction industry.
In Argentina, Holcim recently inaugurated a new mortar plant at its Malagueño cement plant in the province of Córdoba in order to produce different construction products for the local market.
Among the new products are cementitious adhesives for ceramic and porcelain tile placement, lime-based mortars for interior and exterior finishings, and normal mortars for interior and exterior finishings.
For the start-up of the new plant, Holcim Argentina invested approximately $5 million.
This operation is aligned with the Holcim Group strategy focused on expanding its portfolio with products and services that provide comprehensive solutions for the construction industry.
This new production line was carried out within the premises of the existing Malagueño plant and has a surface area of 1,500 m2. It includes six silos for storing raw material, each with a capacity of 100 tons; eight 1-ton silos for additives; a 2,000-liter mixer; a production line with three packaging machines; automated palletizing; and complete narrowing for subsequent transport. In turn, the new production line has a 750-m2 covered structure where the bagging and palletizing area is located.
The new facility is designed with a production capacity of 120,000 tpy.
Currently in production at the mortar plant, the following stand out: Four products from the Tector Adhesives line, and another four from the Tector Revokes line. All the products are packaged in 25-kg bags.
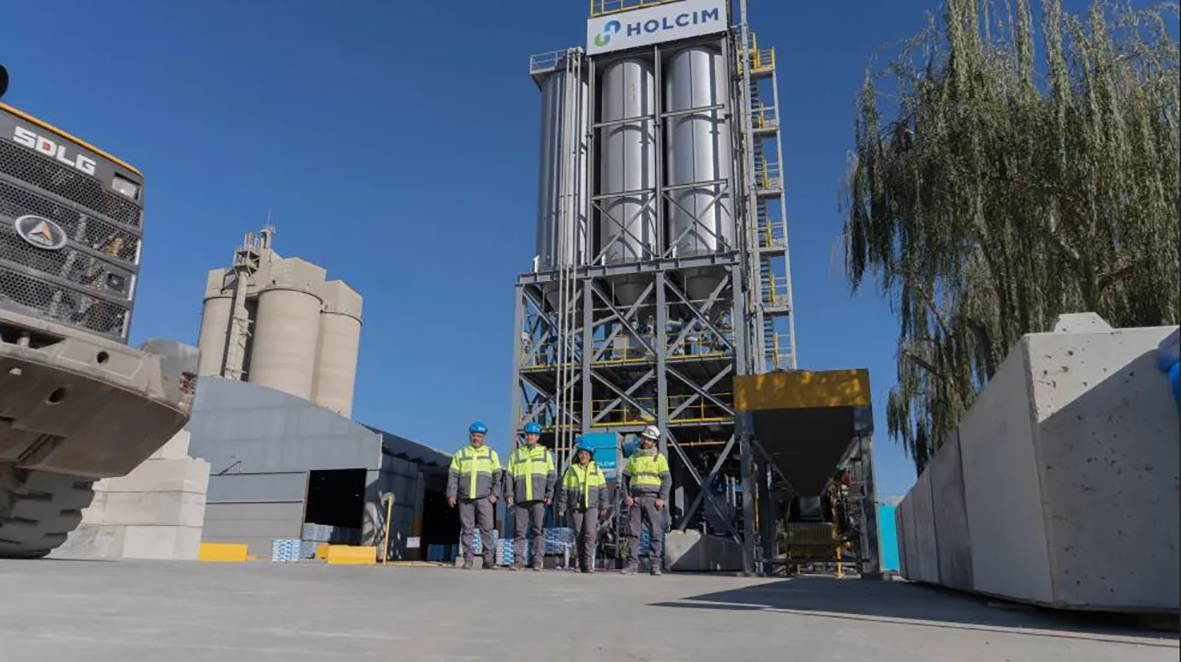
Credit: Holcim Argentina
Peru
In Peru, the Unacem Group received approval from the National Institute for the Defense of Competition and Protection of Intellectual Property for the launch of a new company with Mexico-based Group Calidra.
The new company was created to build and operate a quicklime and calcium carbonate plant in Condorcocha, Tarma province (in the Junín region).
The facility will have an initial production capacity of 600 tpd, thanks to a total investment of $40 million and its construction would begin in the fourth quarter of 2023, to begin operating in the first half of 2025.
The project includes the installation of six silos to collect raw material, each one having a capacity of 100 tons; seven 1-ton silos for additives; a sand dryer; a 2,000-liter mixer; three packaging lines; and automated palletizing.
The entire installation features respective bag filters at each point to avoid the spread of dust. To carry out this project, a shed will be built with an area of 750 m2 where the bagging and palletizing area will be.
The new lime line has a kiln with a total production capacity of 1,000 tpd that is made up of two regenerative units, the first with 600 tpd and the second with 400 tpd.
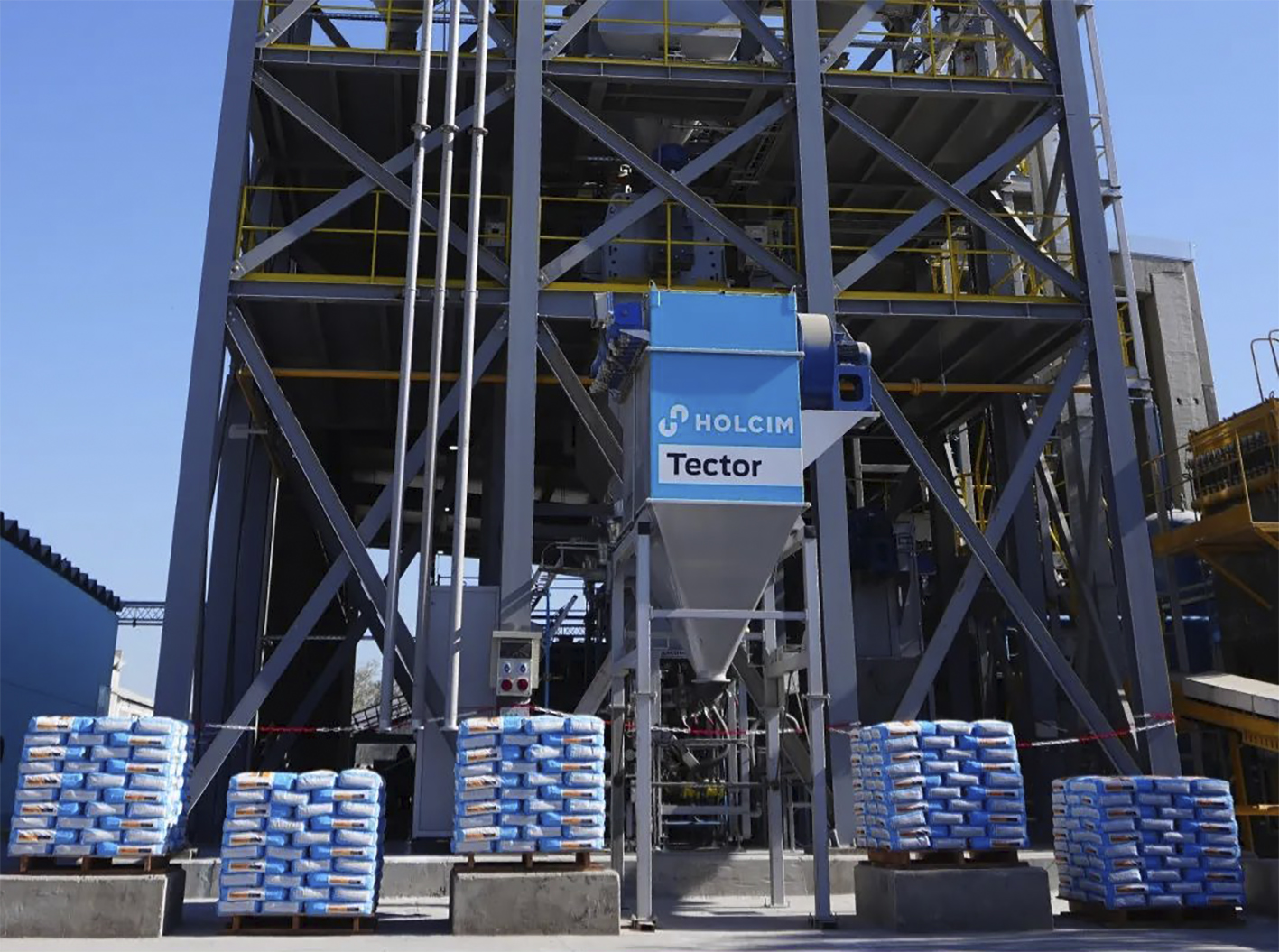
Regenerative furnaces have a technology that allows a minimal particle emission. The production process is made up of the stages of stone crushing, calcination, fed by solid fuel, quicklime pulverization system, packaging and storage.
In the crushing phase, calcium carbonate enters with a granulometry of 0- to 40-in.; once this material is crushed, a 3/4- to 5-in. granulometry is obtained where the excess material from this process can be used in the manufacture of cement.
In the kiln, calcination (using petroleum petcoke) the main material of the process is calcium carbonate, it enters with a granulometry of 2½- to 5-in,; the output product of this process is lime.
This process will have a gas filter (CP1-01) and dust recirculation. For quicklime pulverization, the main material of the process is lime < ¼-in. This process will also have bag filters (CPO-03) and a cyclone.
Finally, in the packaging phase they go to three different granulometries: 200 95%; 1/4- to 0-in. granules, and coarser 7/8- to 1/4-in. granules.
Mauro Nogarin is Cement Products’ Latin American correspondent.