When It Comes To The Sustainability Of Cement Production, Refractories Have A Broad And Essential Role To Play, As Experts From Calderys Group, Including Hwi, And Refratechnik Told Cement Products.
Since the early days of cement production, the industry has worked to reduce its specific energy consumption. This has changed the landscape of the cement plant as “today’s preheater-precalciner kilns with high-efficiency coolers replaced wet and dry long kilns and brought specific energy demand down to less than 750kcal/t of clinker (3.140 kJ/t of clinker),” said Dr. Hans-Jürgen Klischat, head of R&D at Refratechnik Cement GmbH. “These optimizations have more or less reached their technical limits, so other factors are now in focus, such as waste heat recovery units.”
Yet despite notable advances, some 10% of process thermal energy is still lost through the walls of the equipment (Figure 2). “Here, refractory engineering and design come into play to develop new refractory concepts that improve thermal efficiency by reducing the lining’s thermal conductivity while maintaining operational performance. This refractory concept is applied globally to the heart of the plant, the rotary kiln, which is responsible for 40% to 60% of heat losses,” Klischat emphasized.
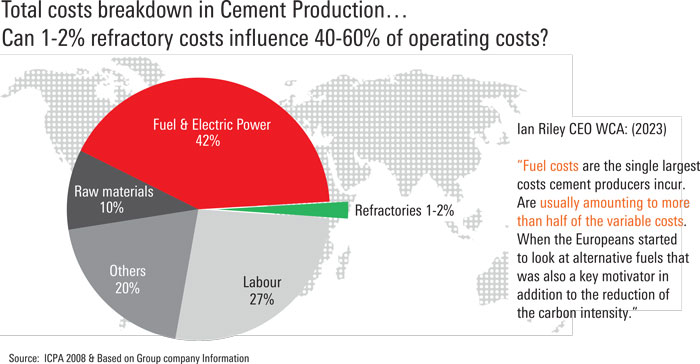
Case Study: Developing Energy and Emissions-Saving Refractories
Refratechnik was approached in 2012 by industry stakeholders to create a refractory that would maintain refractory performance while significantly reducing heat loss. The result “was the development of the patented ES (energy and emission saving) refractory concept, which led to the first basic brick grade providing ~30% lower wall heat losses.
This was achieved by reducing its thermal coefficient over the total application temperature profile,” Peter Groger, director of sales at Refratechnik, told Cement Products. “The ES portfolio also consumes about 10% less raw materials for manufacturing, reducing the environmental impact of production and transportation, as well as the amount of waste generated at tear-out.“
According to Groger, in 2015, the company’s ALMAG ES grade refractory (Figure 3) was independently evaluated by the German Cement Association (VDZ). In parallel, practical field tests were included in the proof of concept. These covered all relevant cement and lime kiln types (i.e., OPC, white cement, lime, and lime recovery); kiln diameters from 2.8 to 6.5 meters and capacities from 1,500 to 12,500 tpd; and all fuel types (coal, lignite, petcoke, gas, oil and alternative fuels).
Based on the VDZ evaluation and external applications, “we established a complete ES Series product portfolio of basic, high alumina and fireclay brick grades for all kiln zones and operation conditions,” continued Groger. “This refractory line-up was presented to the VDZ again for independent expert evaluation. In this latest study, the VDZ calculated a potential saving of about 3,500 tons of coal and 4% to 5% thermal energy at the main burner for a 5,000-tpd-capacity BAT cement plant with a 5-meter diameter x 75-meter long kiln. This also results in savings of more than 8,000 tCO2. Both values are calculated over an operating time of 320 days.”
Groger concluded that scaling up the VDZ-BAT simulation to cover global clinker production would save 4 to 6 million tons of coal equivalent and 10 to 14 million tons of thermal CO2. As refractory materials are consumables (i.e., OPEX costs), these commercial benefits can be achieved at any relining without the need to change other parameters or incur additional CAPEX.
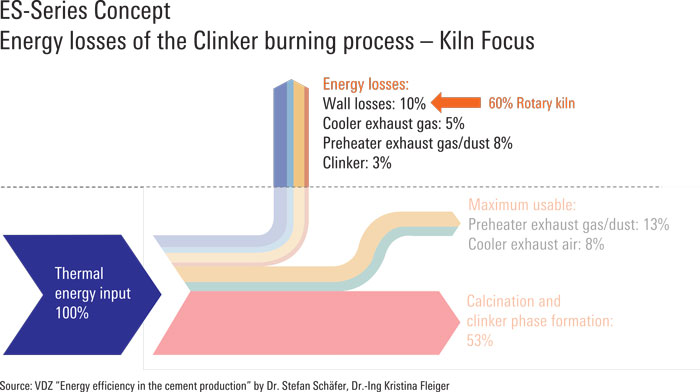
Refractories and Alternative Fuels
At the same time, refractories have had to deal with changes in how cement plants operate, notably the rising use of alternative fuels. Here, refractory suppliers have focused on “increasing refractory service life to help cement producers transition their energy needs,” Larry Morley, applications manager – cement and lime at HWI, a member of Calderys, told Cement Products.
Initially introduced to control fuel costs, alternative fuels are now considered an essential pathway to lower carbon emissions in cement production. Thermal substitution rates in some parts of the world can exceed 50%. In Austria and Germany, for example, rates exceed 70%, according to environmental data for 2022 from the VDZ.
“The addition or increased use of alternative fuels results in faster than ‘normal’ refractory wear in the form of chemical attack due to alkali and salt penetration of the refractory,” explained Morley. Alternative fuels can also increase build-up in certain areas, e.g., the lower riser and vessels in the lower portion of the preheater tower. This build-up “leaves plant operators struggling to maintain a smooth process. Air and material flow can be hindered, resulting in the need to remove buildups mechanically. This can lead to thermal shock and rapid wear of refractories at the hot face.”
Higher wear rates and build-up also require increased maintenance, including the risk of “unplanned shutdowns for repairs and higher bin costs due to increased fuel use for (non-productive) kiln preheating,” the HWI expert continued. “This not only causes interruptions in production; it also introduces a safety concern for those plant operators responsible for removing the built-up material.”
Combatting these challenges typically means using refractories that contain silicon carbide and/or zirconia/zircon. However, “these raw materials are expensive, so using them strategically is important to help control refractory spending,” noted Morley. “A thorough understanding of the wear mechanisms and their location in the pyroprocess line will help plant operators achieve plant reliability and performance KPIs.”
The higher cost of such refractories may be “offset by the consequent reduction in energy costs and CO2 emissions, as well as operational downtime,” added Refratechnik’s Klischat. It is also not solely about the refractory materials themselves. “The proper selection, engineering, design, and installation of refractories play a vital role. Close communication and interaction between the plant operation team and refractory partner are essential in creating the best solution to support any transition to alternative fuels.”
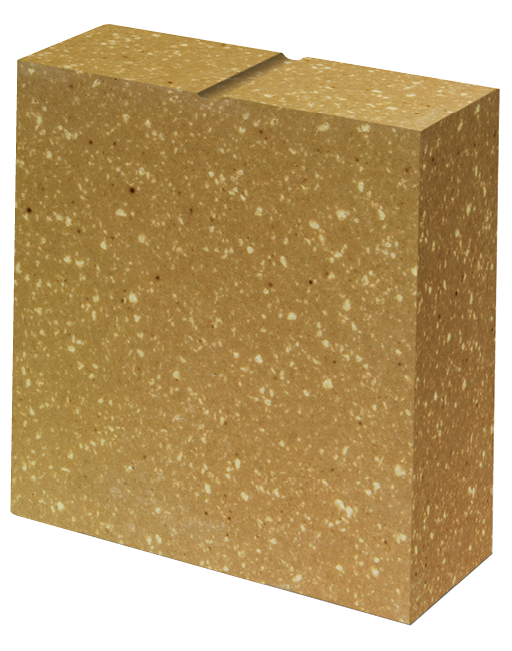
Case Study: Mitigating Alkali Attack in Cement Kilns With Refractory Solutions
While the shift in kiln operations to alternate fuels, such as tires and car fluff, presents significant cost savings and carbon emissions reduction benefits, “transitioning can introduce new wear mechanisms that impact existing refractory linings,” HWI’s Morley told Cement Products. “When a large North American customer sought to understand these wear mechanisms, our product and research teams provided critical insights. We enabled the customer to anticipate and address potential problems, select and optimize refractory linings, and maintain production efficiencies.”
As noted earlier, alkali attack is a primary concern with alternate fuels. Compounds such as sulfur oxides (SOX), alkali sulfates, and chlorides infiltrate refractories, particularly magnesia-spinel types. SOX reacts with magnesia and lime in the brick to form MgSO4 and CaSO4, which further react with other sulfates and chlorides, weakening the bond structure and making the lining prone to thermal shock and spalling.
“Understanding the current state of refractories is vital to mitigate these effects when transitioning to alternative fuels or new raw materials,” explained Morley. “Proactive approaches, including half-life sampling and zonal chemistry analysis, provide valuable insights into wear mechanisms. Techniques such as x-ray fluorescence spectrometry (XRF), x-ray diffractometry (XRD), and scanning electron microscopy (SEM) reveal chemical and mineralogical changes within the refractory, guiding better maintenance and replacement strategies.”
After extensive research and customer collaboration, HWI introduced the THORBIDE family of high-alumina bricks with silicon carbide in 2020 (Figure 4). The products provide superior alkali attack and abrasion resistance, low porosity, and exceptional thermal shock resistance. These features significantly reduce alkali attack and infiltration, resulting in a more stable operation and longer lining life.
“By combining proactive approaches to understanding refractory wear mechanisms with advanced solutions like THORBIDE, we are helping cement manufacturers solve problems and manage their refractory needs effectively, ensuring production efficiency and reliability in transitioning to alternate fuels,” added Morley. Through HWI’s combination with Calderys, its expertise is now available globally to cement manufacturers, aiding them in their energy transition efforts.
New Operating Conditions
Efforts to reduce carbon emissions are taking the cement industry in new directions with new fuels (e.g., hydrogen) and operating concepts (e.g., oxyfuel, calcium looping, calcined clay, etc.). Implementing these will again require adaptation and innovation from refractory suppliers.
“The use of hydrogen as a main fuel is currently fairly limited,” said Klischat, “but test applications have been conducted, with more on the way. The impact of hydrogen on the shape and temperature of the flame, radiation, and convection ratio will have to be considered, as will the water/fluid condensation phenomena in critical areas.”
“Hydrogen and oxyfuel combustion will both increase the thermal load on refractories,” added Divyendu Tripathy, thermal marketing director at Calderys. “This is likely to lead to the need for higher grades of refractory in certain areas, compared to traditional fuels.”
“Experience of using hydrogen in other thermal processes and industries will help develop suitable refractory solutions for the cement industry,” noted Klischat, as will the participation of refractory suppliers in industrial-scale studies to evaluate the long-term impact on refractories, something both Refratechnik and Calderys are engaged in.
Refratechnik supplied the Leilac I project at Lixhe, Belgium, and is now supplying materials to Leilac II at Ennigerloh, Germany; the company is also involved in the CLEANKER calcium lopping project at Buzzi Unicem’s Vernasca plant in Italy; Cementos Argos’ Rio Claro calcined clay plant in Colombia; and the oxyfuel project at Devnya Cement, Bulgaria, part of the ANRAV project. Calderys, meanwhile, supplies materials to the C4C oxyfuel project at the Mergelstetten cement plant in Germany.
As plants transition to these new fuels and operating conditions, “conducting post-mortems on the refractories will help us fully understand their impacts and serve as a vehicle for improving refractory service life,” HWI’s Morley concluded.
Refractories go Digital
“Digital solutions are playing a vital role in all industries on the road to carbon neutrality and performance enhancement,” said Refratechnik’s Klischat. This is also true when designing refractories to support cement’s net-zero transition. “Customer operating and process data are essential to customizing refractory solutions, e.g., big data and remote data transfer to support simulation processes.”
“Discovering innovative ways to be proactive in refractory maintenance will involve digital solutions, such as laser scanning and imaging technology,” added Morley. “We currently use these methodologies in steel production, where the refractory turnover is much quicker. Translating these to clinker production will be the driving force for refractory services in the coming years.”
“Non-destructive remnant lining thickness and ovality measurement devices are currently being used to support our customers,” Morley continued. “Tying this information to 3D modeling and laser imaging while incorporating customer data, such as process, quality, and mechanical data, is the long-term goal.”
Ultimately, digital tools will only support the cement producer’s most powerful resource: their onsite plant personnel. “Knowledge sharing and best practice training will play a decisive role in providing the skills needed for today and tomorrow,” concluded Klischat. “From basic training as part of the onboarding process through continued learning throughout a career, investment in personnel will remain critical, even as digital solutions advance. For this, we founded the REFRA-Academy to serve both internal and external stakeholders on a global, regional, and local level.”
Refractories in the Circular Economy
Beyond the critical aims of improving energy efficiency and reducing carbon emissions, refractory providers are also aware of their position within another central sustainability ambition: the Circular Economy. “Refractories are engineered, high-performance ceramics produced from high-value minerals,” explained HWI’s Morley. “But historically, used refractory has ended up in landfill, wasting the remaining value of the residual material, not to mention the landfill expense. Creating a circular economy for waste refractory is thus a top priority.”
“Used refractories should not be considered waste but a precious resource for further use and applications,” agreed Klischat. “This is already standard in various industries and is the aim for refractory manufacturers in general.”
“Reusing the tear-out requires a robust circular economy with multiple players,” continued Morley. “Special expertise is needed at each step, including sorting the different refractory materials from the kiln and processing the waste by further separation, cleaning, crushing, and sizing. Because the reclaimed refractory is a matrix of minerals, it differs inherently from the virgin material from which it was produced. Differences in purity and changes in physical properties, such as porosity, define the reclaim quality. The reclaim is thus carefully tested at various substitution levels and approved for appropriate end uses. The top choice is always to use the reclaim within the original refractory formulation if this can be done without negatively impacting product performance. Reclaim can also be used in a different refractory product with a different performance profile.”
According to Tripathy, the Calderys Innovation and Technology group is developing options for drop-in substitution, formulation redesigns, and products designed specifically for recycled/reclaimed materials. Once a material is approved for use, the reclaim is transported to one of the company’s plants, where it is incorporated into a finished product.
It is also true that reuse and recycling come after prevention in the waste hierarchy – a point Klischat noted. “Developing products that consume less raw material avoids waste from the start. It is also important to protect stored refractories to avoid the loss of goods before they are used. For example, 6% of basic refractory bricks are disposed of in subtropical environments due to hydration of the main component (MgO or MG(OH)2). But even when goods are degraded, it is again possible to collect them and incorporate them into the manufacturing process.”
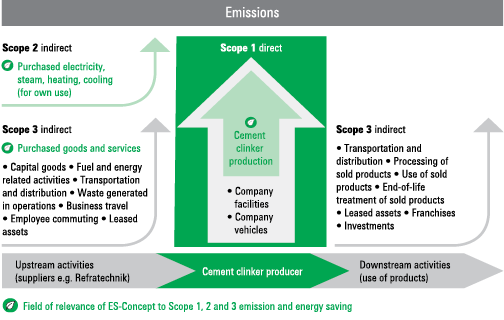
help reduce the cement industry’s Scope 1, 2 and 3 emissions.
Source: Refratechnik
Sustainable Refractories
The reclamation and reuse of refractory materials not only reduces waste. It also reduces the environmental impact of refractory production. “Refractories start life as minerals extracted by mining,” noted HWI’s Morley. “Mining impacts the surrounding water, plants, animals, land quality, and people. Many raw minerals also receive high-energy thermal processing to develop the properties that enable them to be used in refractory products. The best way to reduce these impacts is to reduce the consumption of virgin minerals.”
“When it is time to install a new refractory lining, about half of the old lining has been consumed in use, and the other half remains,” Morley continued. “By recovering and reusing that material, we reduce the amount of virgin materials needed and the high energy thermal processing of the virgin raw material. We cannot eliminate mining because the refractory is partly consumed, but the industry is working toward full recycling, aided by technological advancements and regulatory drivers in some regions. In addition, we seek relevant industrial wastes near our manufacturing plants, which can be substituted for our virgin raw materials.”
This last point not only reduces the need for virgin raw materials; it also reduces transport-related emissions, as does the use of fewer refractories over the lifetime of a kiln due to longer-lasting refractories.
When it comes to refractories and sustainability, however, Klischat reminded us that the use of high-quality, lighter-weight refractories avoids significantly more emissions than are generated in their production. “We can reduce a cement plant’s Scope 1 direct emissions by more than ten times the total Scope 3 upstream emissions generated during refractory manufacturing while also reducing a plant’s Scope 2 indirect emissions by cutting the amount of purchased electricity, as cooling fans can work less, while the kiln drive must turn 50 to 80 t less refractory lining (Figure 5).”
“Refractories are an essential part of the sustainability journey, not just for cement, but in many industries,” the Refratechnik expert concluded. “The job of the refractory manufacturer is to adapt to the KPIs of these industries, whether that’s energy efficiency, emissions reduction, or more sustainable operating practices. It is something we, and others, as refractory producers, are ready for, not tomorrow, but right now.”