What Are Some Of The Problems Experienced In The Cement Industry And How Can They Be Overcome?
By Alan Highton
Spiraling energy costs, pressures on extractive resources and the drive to reduce carbon emissions are prompting more and more heavy industry sectors to switch to waste-derived fuels and raw materials.
Operators already using such alternatives know that handling them can be tricky. Here we explore some of the problems experienced in the cement industry and how they can be overcome.
The cement industry was among the first sectors to investigate the use of cost-effective alternatives to the likes of coal and pet coke. As far back as the 1970s, plants in Europe and the United States were blending fossil fuels with shredded tires and offcuts from timber production.
Since then, with fuel typically accounting for more than a quarter of cement clinker production costs, an increasing number of producers have been sourcing alternatives. Recent years have seen things accelerate as producers seek to secure suitable waste streams to optimize the use of available materials and deliver on their net-zero carbon commitments.
Today, a handful of cement plants around the globe are able to boast 100% alternative fuels, raising the bar for the sector and challenging fossil fuel-reliant plants to look to locally available wastes as fuel sources – from non-recyclable plastics, commercial mixed wastes and shredded upholstery to biomass like rice husks, sugar cane bagasse, and pelletized animal meal.
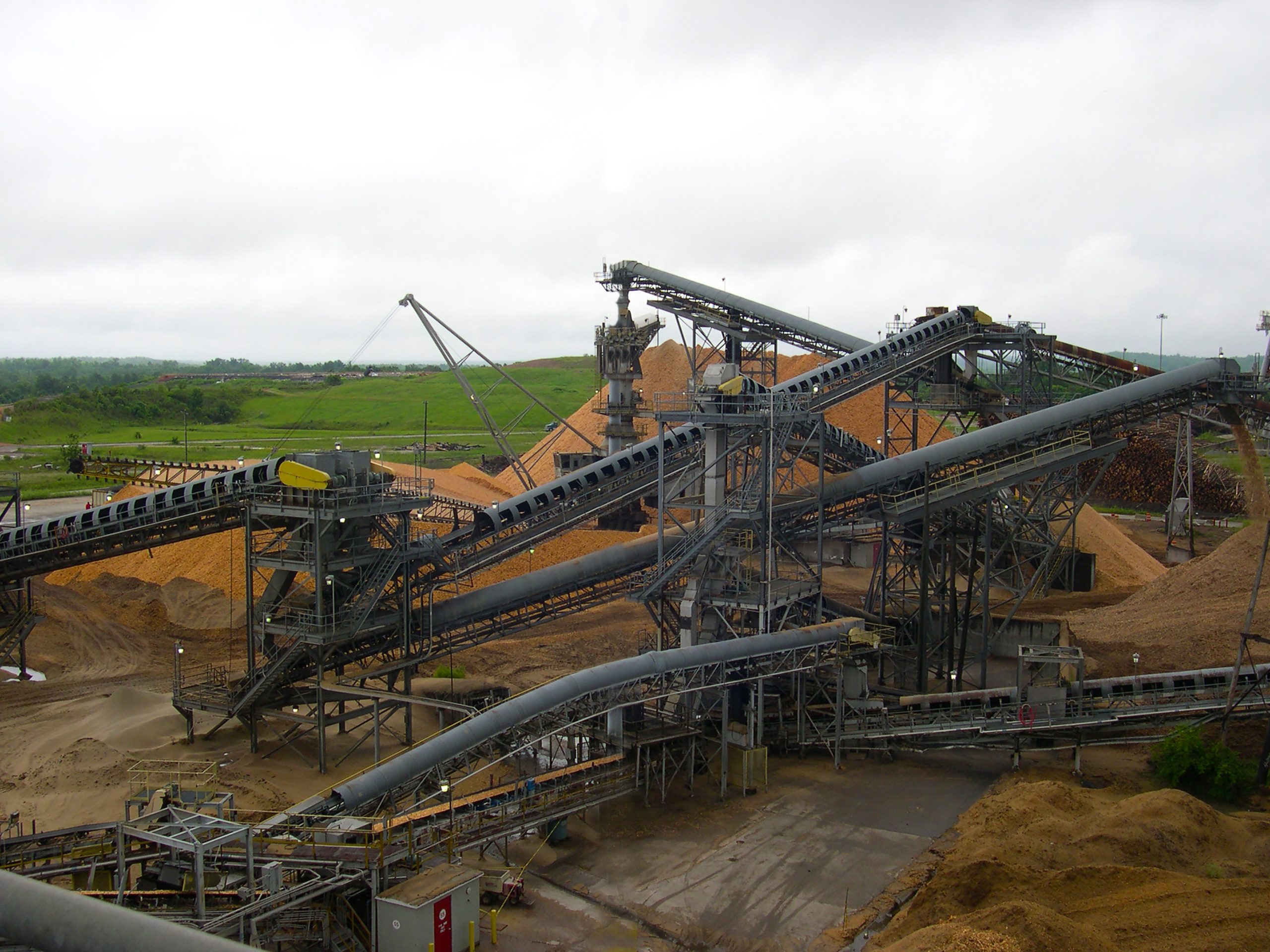
Buildups, Blockages and Breakdowns
The choice of alternative fuels requires careful consideration as the implications for productivity and process design can be significant. One of the key differences between solid fossil fuels and waste-derived alternatives is their flow characteristics, largely determined by their physical makeup and moisture content.
Efficient and continuous material flow is a critical element of dry-process cement manufacture, and any accumulation or blockages can choke a plant’s profitability. Hang-ups in storage systems and buildups in chutes and process vessels can cause serious blockages that impede equipment performance and reduce efficiency.
Material buildup can occur in many places, and in several forms. Accumulation often occurs in riser ducts, feed pipes, cyclones, transfer chutes and storage bins, as well as kilns and coolers. In extreme cases, massive buildups can suddenly break loose and suffocate the process, potentially causing significant damage to equipment and almost invariably prompting the need for unscheduled downtime.
It’s worth stating that buildups of alternative fuel materials can happen even in well-designed systems. Changes in process conditions, the raw materials themselves, or even the weather can have an effect on material flow, and a small amount of accumulation can quickly grow into a serious blockage, with obstructions often leading to other problems.
Accumulations of some alternative fuels are even susceptible to spontaneous combustion, while others may accelerate wear, tear and corrosion of structures, and deterioration of conveyor components. A preventive approach to controlling buildups and blockages is the only way to address these issues and prevent unscheduled downtime.
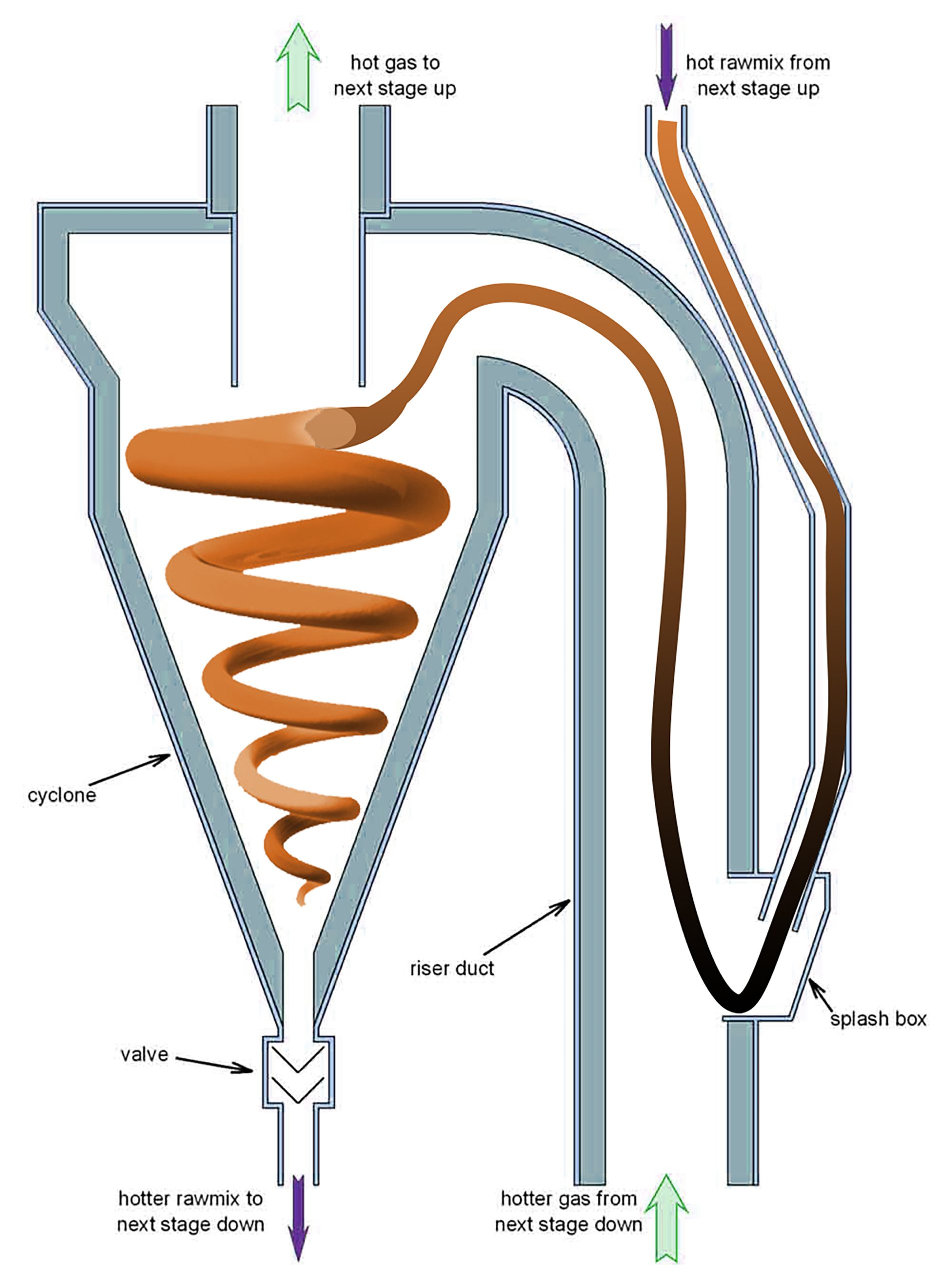
Flow Problems and Safety Risks
Lost production is usually the primary cost of flow problems, but the expense can become apparent in a variety of secondary ways. Shutdowns to clear blockages and buildup also cost valuable process time and maintenance hours. That increases maintenance costs and diverts service teams away from core activities, potentially introducing needless safety risks.
Refractory walls can become worn or damaged by tools or cleaning techniques. When access is difficult, removing material blockages may also introduce serious risks for personnel. Working platforms are usually needed to reach access points, and there’s a risk of exposure to hot debris, dust or gases when chunks of material stuck to the sides of a silo, hopper or bin are suddenly released.
If the discharge door is in the open position, material can suddenly evacuate, causing unsecured workers to get caught in the flow. Cleaning vessels containing combustible dust – without proper testing, ventilation and safety measures – could even result in a deadly explosion with as little as a spark from a shovel.
Many of the most common problem areas for accumulation are also classified as confined spaces, requiring a special permit for workers to enter. The consequences for untrained or inexperienced staff can be serious, including physical injury, burial and asphyxiation.
Design the System Around the Fuel
The most effective way to manage the challenges of using alternative fuels is to design the material handling system around the physical properties of the intended fuel. That means each component is specified and engineered according to the flow characteristics of the material.
In reality, most cement producers will be using existing systems to feed in alternative fuels, which can require some modest retrofitting or a whole new facility. Martin Engineering has been perfecting material handling technologies in sectors like cement for more than 75 years and there are few challenges that Martin technicians haven’t already faced and overcome around the world.
One approach that brings significant benefits to operators seeking to retrofit material handling systems to accommodate alternative fuels is to use modular components. These can be specifically built to handle the cargo such as transfer chutes with specific flow angles or settling zones of appropriate height and length. Rather than replacing large sections of existing equipment, modular designs can be engineered to fit into the specific system that is already on hand.
However, Martin’s engineers are also experienced enough to know that designing a single system to handle every type of alternative fuel is virtually impossible. Materials with high moisture content can adhere to chute or vessel walls or even freeze during winter temperatures.
Continuous operation can compress the material, and physical properties often change due to natural and inevitable variations that are typical in waste-derived fuels. Just a small change can cause a system to become completely blocked in a short amount of time. Most of these issues can be overcome, and a whole-process approach is needed with a selection of flow aids installed to collectively work together to keep things moving.
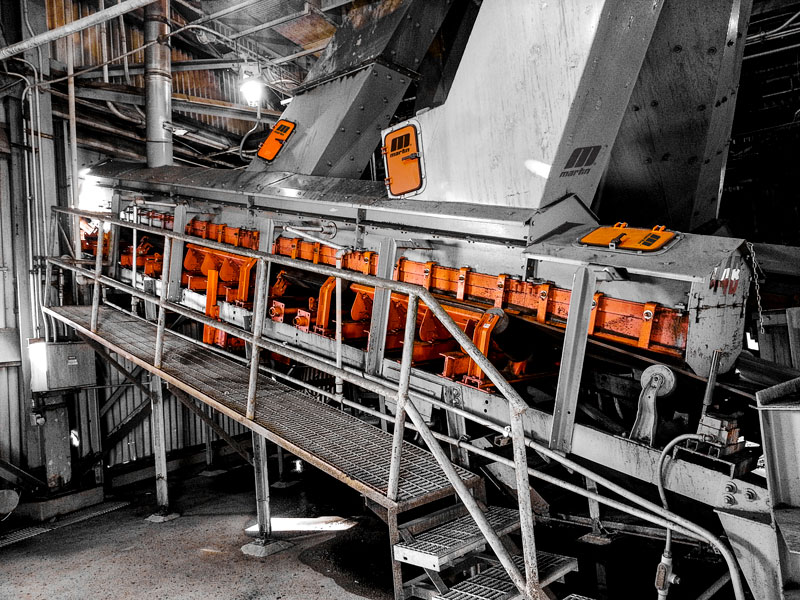
Dust Control at Transfer Points
One of the first challenges to be addressed when using dry alternative fuels is the potential for release of combustible dust, and containment is therefore critical. Successful dust management starts with minimizing air turbulence through appropriate transfer point geometry.
Air is very compressible and will find the path of least resistance. Typically, the design of transfer points means that air is most often speeding up to flow under or around a single exit dust curtain with narrow slits, resulting in re-entraining the dust particles in the exhaust. Therefore, it’s necessary to create recirculation regions inside a transfer point to improve dust settling and containment.
A transfer point is similar to a gravity settling chamber, which depends on relatively slow air speed without much turbulence. Conversely, the airflow through a conveyor transfer point is almost always turbulent.
So, the transfer point enclosure design needs to incorporate a series of curtains to slow and control airflow and promote settling. Used in tandem with adjustable dual skirting, these can create a sealed environment where dust settles back into the cargo flow or is sequestered into a dust bag without spillage or emissions.
Going With the Flow
To achieve contained and consistent flow on conveyors handling large volumes of alternative fuels, transfer chutes and vessels must be designed to accommodate and facilitate the flow of the materials they will be handling. Even if the operating conditions are expected to be ideal, many engineers include flow aid devices in new designs to ensure delivery of the optimum results but with the agility to deal with changes in alternative fuels and raw materials.
Flow aids is an umbrella term for a complementary set of components installed to promote the transport of materials through an entire system. Because they will affect a conveyor’s loading, flow aid devices can also reduce spillage and help control dust.
If not properly managed, buildups that break free – accidentally or intentionally – can produce surges, which result in overloading, spillage and belt mistracking. By designing active flow aids into a conveying system, the operation gains a level of control over the material that cannot be obtained with static approaches (such as low-friction liners) alone.
Flow aids come in a variety of forms, including rotary and linear vibrators, high- and low-pressure air cannons and aeration devices, as well as low-friction linings and special chute designs to promote the efficient flow of bulk materials. These systems can be combined in any number of ways to complement one another and are shown to improve performance.
They can be as simple as an impacting piston vibrator on a chute wall to dislodge material buildup, or as sophisticated as a multiple air cannon system discharging automatically on a timed cycle to prevent accumulation. The components can be used together to benefit processing of virtually any bulk alternative fuel or hazardous or complex materials.
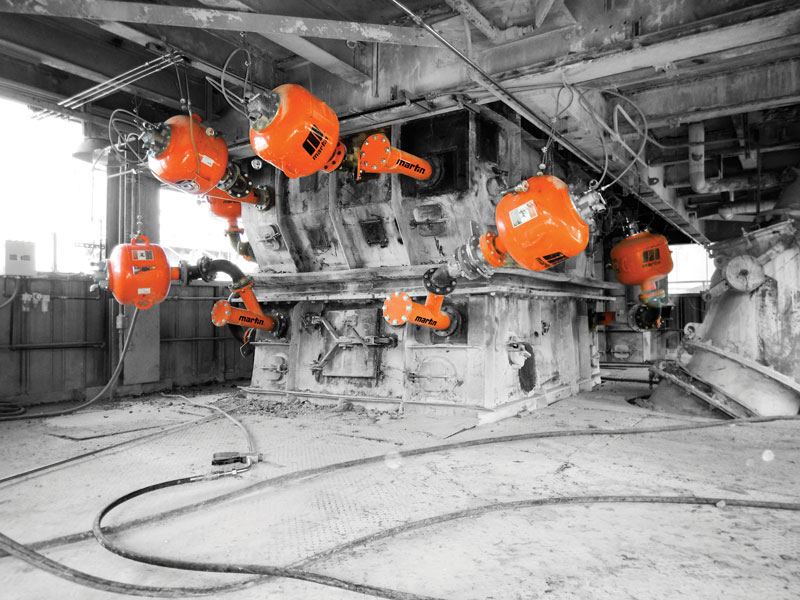
Productivity Starts With a Blast
One of the most successful devices for resolving material flow issues associated with bulk handling is the Martin Air Cannon, which has a number of applications in cement production, from unclogging cyclone collectors and kiln inlets to keeping super-heated material moving through the cooling process. Air cannons function by releasing a powerful shot of pressurized air from a tank through a short pipe assembly to a specialized nozzle, breaking away collected material from inner surfaces and directing it back into the process stream.
Recent innovations in the design, engineering, assembly and installation of air cannons have been particularly effective in maintaining safe, efficient flow in cement operations. Today, air cannons are relatively compact and lightweight, with efficient and powerful performance.
New tank designs range from 35- to 150-liter capacity and deliver more force output with less air consumption at half the size of older designs. The way they’re built, installed, serviced and powered is all geared towards maximizing production and reducing both downtime and the overall cost of operation, while contributing to better safety. Air cannons often eliminate the need for confined space entry to remove buildup. Martin air cannons are designed to discharge only with a positive pressure pilot signal to reduce the chance of accidental compressed air release.
Bringing cement production equipment up to operating temperature takes a tremendous amount of energy. The cost of downtime for cooling the system, performing maintenance work and reheating the kiln can be prohibitive.
So modern air cannons are designed to be easily serviced from outside as individual units, for example Martin’s Y-pipe assembly can be maintained without shutting down production. And to avoid the need for tank removal and confined space entry, engineers have designed new cannons with outward-facing valves. This provides safe, easy access by a single maintenance worker from outside the vessel.
That innovation is one of a number of flow aid accessories that can be installed to achieve even better performance. For example, Martin’s SMART Series high-temperature nozzle enables hassle-free air cannon maintenance as it’s safe and easy to service and replace without damaging the surrounding refractory. Then there’s the Thermo Safety Shield which protects workers against exposure to extreme heat, allowing safe and timely servicing of air cannon systems.
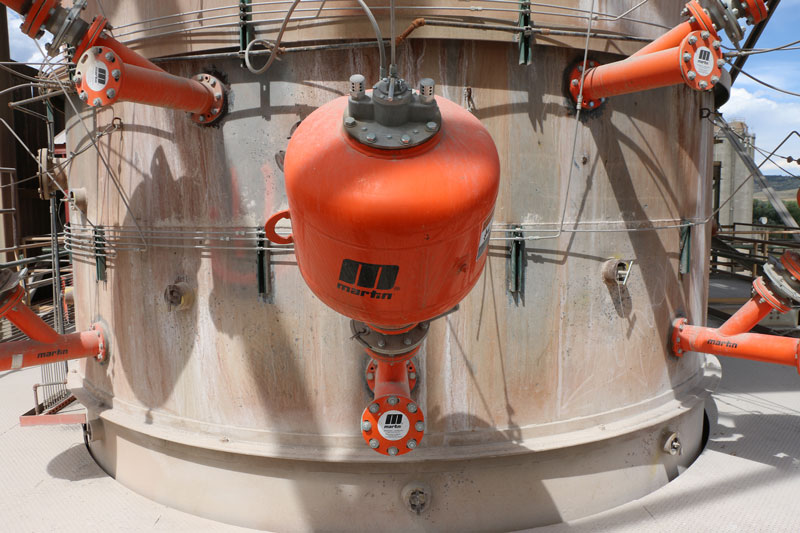
Full Installation Without a Shutdown
Not only does advanced engineering mean that servicing of air cannons can take place without the need to stop production, but Martin recently launched a patented technology that even enables them to be fully installed without a process shutdown. This system allows specially trained technicians to mount the units on furnaces, preheaters, coolers and other high-temperature locations while production continues uninterrupted.
Specialized core drill bits are engineered to create the exact diameter hole at the precise angle needed. Once a core is safely installed in the vessel wall, an isolation gate is inserted to protect from heat and blowback.
Trained technicians then attach the Y-pipe assembly with no downtime or process disruption. The technology dramatically reduces expensive downtime associated with traditional installation methods, which require that high-heat processes be halted to allow core drilling and mounting of the cannons.
Core drilling is a careful and precise process to ensure there is no cracking in the refractory.
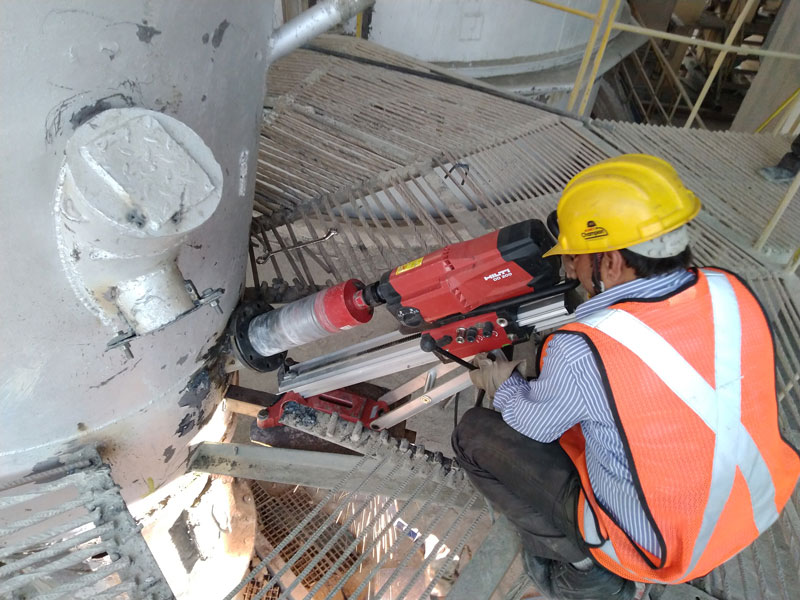
Conclusion
The use of alternative, waste-derived fuels and raw materials does present challenges due to their composition and characteristics. Yet those challenges can be overcome with the support of bulk material handling specialists who are able to identify existing and potential problems and their root causes, and design complete systems that prevent buildup and avert the knock-on effects for production.
Making good use of wastes either as fuel or as raw material is cost-effective and environmentally sound. Coupled with the expertise to develop effective handling solutions, operators can be sure to maintain the highest levels of safety, efficient and productivity.
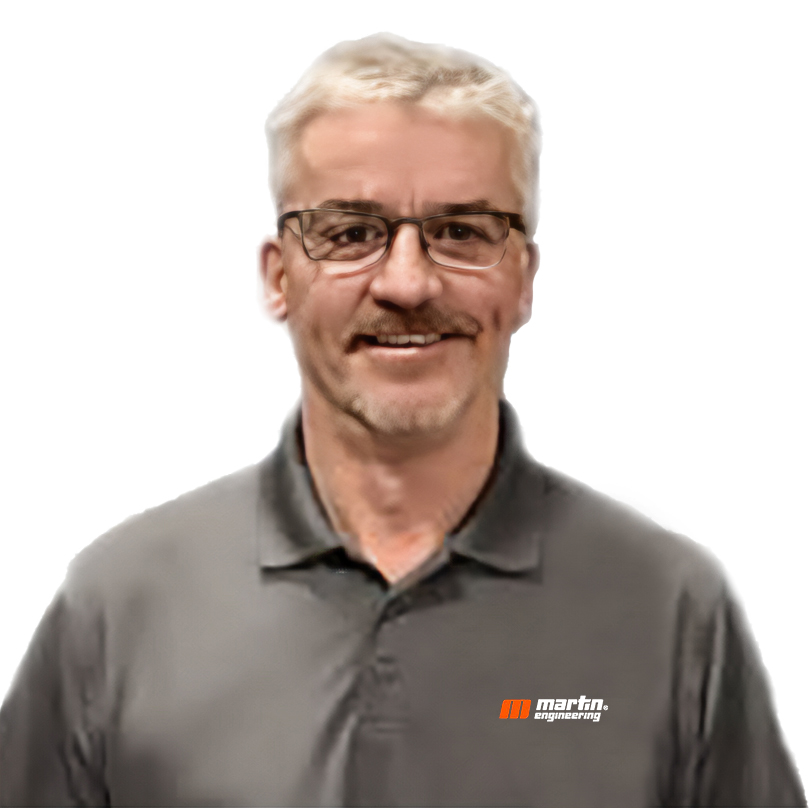
Alan Highton is national sales manager, Martin Engineering. All photos copyright 2023 Martin Engineering.