The Cement Laboratory Is A Crucial Source Of Data. Collecting And Managing That Data Are Vital Tasks Supporting A Plant’s Industry 4.0 Journey, As Flsmidth Cement’s Jens Asbjørn Pedersen Explained To Cement Products.
By Jonathan Rowland
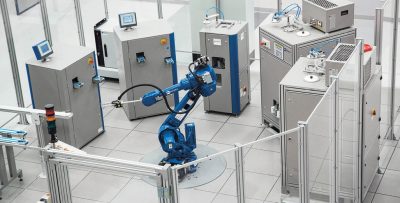
It was in 1969 that a small group of pioneers changed the course of history. No, not the astronauts of Apollo 11, but Henrik Bang-Pedersen and his colleagues in the electrical department at FLSmidth Cement, who would that year launch the company’s Quality control by Computer and X-ray system – or QCX as it would become known.
The system applied automated analyses and quality optimization to cement production. A small step in the scheme of what would later be achieved by today’s automation and digital solutions, it nonetheless represented a paradigm shift, allowing cement plants to optimize cement quality and production in an unprecedented way.
The first QCX system was implemented at a customer site in 1970 in Thailand. Its use spread steadily over the next few years. The technology also developed rapidly: fully automated laboratories followed in the 1970s, with the first robotic laboratories after that.
Fast-forward half a century, and the revolution it began has gone far beyond what those first pioneers could have imagined. In this world reshaped by the Industrial Internet of Things (IIoT), cloud computing, artificial intelligence, and machine learning, cement plants are again looking to their laboratories to support the revolution.
How can laboratories support the cement industry’s Industry 4.0 ambitions and beyond? It was a question Cement Products put to one of Bang-Pedersen’s successors, Jens Asbjørn Pedersen, global product manager, sampling, preparation and analysis, at FLSmidth Cement. The answer is found in the “fundamental building block of laboratory automation: the Production Laboratory Information Management Systems (Production LIMS),” Pedersen began. “And the reason for that is data.”
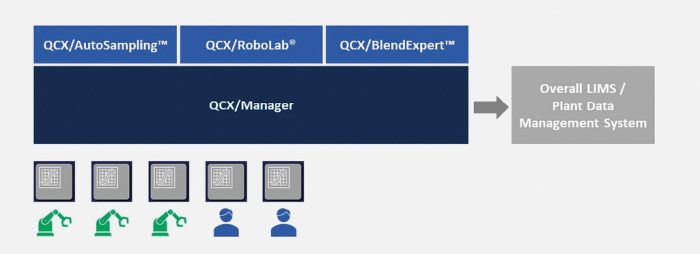
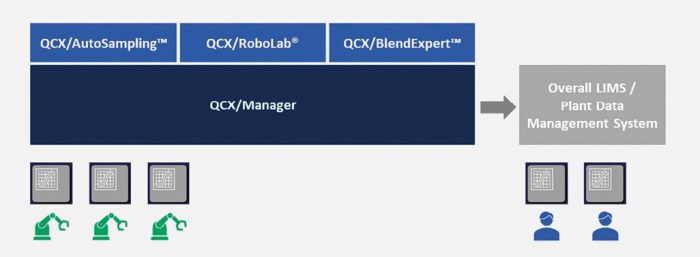
Data are the “fuel that drives Industry 4.0,” he continued. “All Industry 4.0 systems require data; the higher the data quality, the better the Industry 4.0 outcomes will be. Alongside the production process, the cement laboratory is one of the key data sources at a cement plant, providing critical data for controlling and improving cement quality and the whole cement production process.
“Because the Production LIMS collects and organizes these laboratory data and makes them accessible to other systems, including the latest Industry 4.0 technologies, selecting a Production LIMS is critical to a cement plant’s digital journey.”
Types of LIMS
The first issue to be aware of is the two different LIMS applicable to the cement context: Production LIMS and more general data management systems. According to Pedersen, Production LIMS, such as FLSmidth Cement’s QCX/Manager, are “the primary LIMS on which laboratory automation systems are based and to those systems send information. They specifically target the production laboratory environment, offering a set of LIMS features relevant to running many standardized routine samples daily. Production LIMS are typically used for recipe management, laboratory equipment control, and the acquisition of analysis results, and may be sufficient to cover all LIMS requirements at smaller plants.”
Larger plants, however, typically use Production LIMS “at the front end, exporting sample data to an Overall LIMS or Plant Data Management (PDM) system. Such overall systems may cover a single plant or span several plants,” said Pedersen. When this distinction between Production and Overall LIMS/PDM is present, there are “questions about system architecture. For example, when the laboratory contains manual equipment, should this connect to the Production LIMS (Figure 1) or feed results directly to the Overall LIMS/PDM (Figure 2)?”
However, the system architecture works, “it is essential to unambiguously identify every sample across both the Production LIMS and Overall LIMS/PDM,” concluded Pedersen. “Also crucial is ensuring data accessibility to more advanced optimization solutions via effective export functionality from either the Production LIMS or Overall LIMS/PDM. This is true regardless of whether the optimization solutions are based on AI or other technologies and whether they are standard products or more experimental and site-specific trial systems.”
Further Considerations
In addition to the system architecture, there are several additional considerations to keep in mind when selecting and implementing a Production LIMS:
- Metadata.
- Sample database.
- Sample data integrity.
- User interfaces, reporting and trending.
- Export features.
- Online analyzers.
- Equipment performance tracking.
- Initial and maintenance costs.
Metadata are “data about data,” explained Pedersen, with significant sample data metadata including sample time, sample point, and material type. “All metadata are valuable for managing sample data; however, they may become more prominent when implementing Industry 4.0 systems. Deciding how they are handled is thus a crucial factor in planning and implementing a Production LIMS, which should be able to manage metadata gracefully and make them available alongside sample data through data export features.
Sample data are more complex than process data, which “triggers specific requirements for sample database,” said Pedersen. In my experience, a Production LIMS works best when it mimics the real world, with a hierarchical database comprising the main sample and its preparations (Figure 3). This provides an intuitive and direct relationship between the recipe, which controls how the main sample and subsamples propagate through the laboratory, and the sample database, which stores the results and metadata.”
A second question to consider when thinking about the sample database is how long the Production LIMS should store data. Again, this will depend on whether the plant operates only a Production LIMS or with an Overall LIMS/PDM. Data storage time requirements “may also evolve as the need for sample data as the basis for AI increases,” noted Pedersen.
Another important factor is how the cement plant ensures sample data integrity via audit trails and change logs. “Cement plants have traditionally not been as interested in this as other more-regulated industries such as pharmaceuticals,” continued Pedersen. “However, we expect this to change as documentation requirements develop. It also comes at a price. The days of the single operator station, with a generic lab user continuously logged in, are gone.”
User interfaces, reporting, and trending are “basic features but their implementation and quality are nevertheless integral to reliable and accurate system use,” the FLSmidth Cement expert said. “Cement plants should also consider export features, as sample data provide no value when left in the Production LIMS. What systems will the Production LIMS export to, and what are the required export formats? We must also consider future export requirements to futureproof the Production LIMS.”
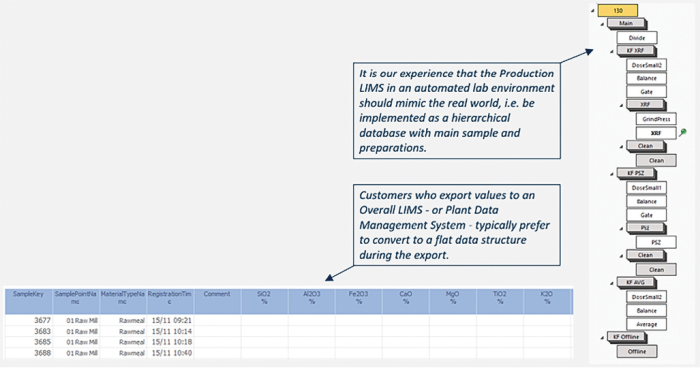
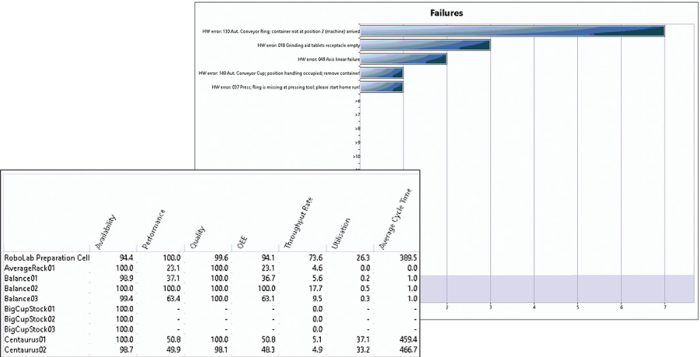
The use of online analyzers is gaining traction in the cement industry. These “provide faster and more frequent results than a central laboratory, but the trade-off is lower accuracy,” explained Pedersen. In the context of Production LIMS selection, however, the critical question is whether online analyzers should connect to the process control system or Production LIMS. “When used for chemical quality optimization, e.g., online XRF, PGNAA, or PFTNA analysis, I suggest that the online analyzer should connect to the Production LIMS as this allows for dynamic calibration based on the more accurate laboratory results; on the other hand, it makes more sense to connect online analyzers used for process optimization to the process control and optimization system,” Pedersen said.
According to Pedersen, tracking equipment status and performance provides “a valuable tool for securing uptime and ensuring efficient use of equipment, providing a life view of the operational status of all connected equipment, and then using that data over time to display more comprehensive performance metrics, usually as key performance indicators.”
There are two limitations to consider: the first is whether the Production LIMS includes status and performance tracking features; the second arises when not all equipment connected to the Production LIMS can report real-time status. “In my experience, equipment designed for automatic sample handling often provides relevant functionality, while equipment designed for manual sample handling often does not,” noted Pedersen. “However, I would always recommend investigating the remote capabilities of specific equipment with the relevant equipment vendors.”
The final consideration is cost, which “will be influenced by factors like initial implementation costs, system flexibility, expected future maintenance, and software licenses/subscriptions,” Pedersen concluded.
The Foundation for the Next Generation of Cement Optimization
The original version of QCX was mere kilobytes in size. Today’s systems are measured in gigabytes and handle terabytes of data. But, “in doing its job collecting and managing sample data, QCX remains as foundational to automation and digitalization in the cement industry today as it became in those early years,” said Pedersen. “As Industry 4.0 advances, careful planning of sample data infrastructure – considering all of the above – will be essential to support the next generation of cement plant optimization technologies and help the industry achieve its goals.”
Note: For a more detailed discussion of the topics raised in the article, see Jens Asbjørn Pedersen and Claus Østergaard’s “What to consider when selecting a Production LIMS,” which is available at https://bit.ly/ProductionLIMS.