Improving Sustainability, Increasing Efficiency And Dealing With Labor Shortages Are Just A Few Of The Challenges The Cement Industry Is Facing.
By John Dronette and Jonas Norinder
The topic of digitalization is very broad. As a result, knowing where to start can seem overwhelming, which makes it even more difficult to figure out how to get started.
In most cases, the digitalization journey should begin with identifying what the organization’s digitalization goals are, keeping in mind it is critical that these goals align with the company’s overall goals. Once this are clarified, the next step is to identify areas of the plant where improvements can be made to achieve these goals
Early Digitalization Projects
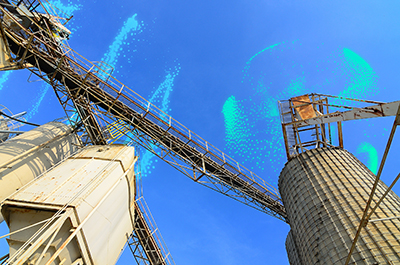
When thinking about a digital transformation, there is often an expectation that the plant will need major upgrades to begin. However, this usually is not the case; in most instances, the digitalization ourney can start with information that may already be available in a digital format from smart instruments. This data must be made accessible and then consolidated into a usable format that provides insights into identifying opportunities to improve the processes.
Early in the digitalization journey, some companies prefer to pilot a single digitalization technology in a specific area that may be experiencing challenges. If you choose to take this approach, selectdigitalization projects can be identified that are scalable and can be implemented across multiple areas of the plant – or even in multiple plants – to maximize the benefit. After the initial implementation, the effectiveness of the project can be monitored, and as efficiencies are gained, the project can be extended across other areas of the plant.
Another important consideration when starting on a digitalization journey is determining how the information will be stored. Will it be stored in a secure cloud or on a local network? If the data is stored in the cloud, there are several factors to consider when selecting a cloud provider:
- The provider should have the ability to seamlessly transfer the information to the cloud, either through the plant network or via a wireless link such as 4G/5G.
- The provider should adhere to the highest level of cybersecurity. Make sure the provider utilizes data protection standards that meet the plant’s IT/OT requirements to protect the stored information.
- Select a provider that can accept data from any type of measurement, regardless of the manufacturer. This will minimize the need to replace existing equipment.
- Consider a provider with digitalization consultants who can be contracted to help in the digitalization journey.
- To allow for remote monitoring, the provider should also have the ability to supply the information to as many users as possible while allowing plant management to control what information can be seen and by whom.
- The provider should be able to send information based on specific needs in various formats, including by phone, email and text, to ensure alerts are received by the proper people when a process upset occurs or if maintenance is required.
Remote Monitoring

Remote monitoring collects data from sensors and measurement instruments and displays it in an easy-to-read dashboard. This information can be process measurements to indicate where an upset has occurred or diagnostics related to the health of the equipment to indicate that preventive maintenance may be required.
The data can be accessed through any web-enabled device with proper credentials and alerts can be configured for distribution in various formats if the process strays outside of defined limits. These alerts can be sent internally to operations or maintenance personnel to ensure smooth plant operation or outside the organization for programs such as vendor-managed inventory of critical supplies.
In a cement plant, continuous feed to the kiln is critical to maintain production. To provide the kiln with this continuous feed, the material level in the homogenization silo must be maintained.
In most cement plants, the material level is already being measured but the reliability of that measurement may not be monitored. Many modern level measurement instruments can provide more information than just the level of the material. These instruments can also provide an indication of confidence in the measurement.
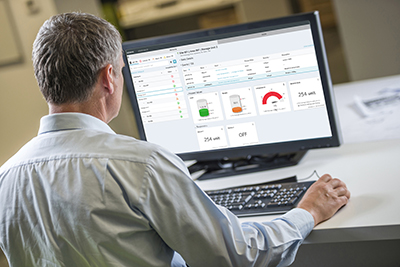
Using remote monitoring solutions allows both the measurement and the confidence to be monitored through a dashboard, and alerts to be sent if either the level or the confidence is not within an acceptable range.
Looking further into this process, similar measurements can be made with the raw material silos, providing additional insight into potential upsets in the supply of material to the homogenization silos.
Smart condition monitors can monitor the vibration and temperature of the kiln drive motor or the motors of conveyors transporting the material to the homogenization silo for early indications of maintenance requirements. This information can be made available to various plant stakeholders for review or monitoring – whether it is the plant manager who wants to get a status of the overall plant or the maintenance technician checking a specific measurement device configuration.
All of these measurements can be displayed on the dashboard so that the potential upsets can be easily identified using a web-enabled computer or mobile device and analyzed for predictive maintenance to provide additional efficiency gains. This analysis can include comparing the results of maintenance practices in different areas of the plant or across multiple plants.
Connected Worker
Efficiency gains through the use of digitalization technologies such as remote monitoring can help reduce demand on plant personnel. Other digitalization tools such as “connected worker” technologies allow plant personnel to work as efficiently as possible.
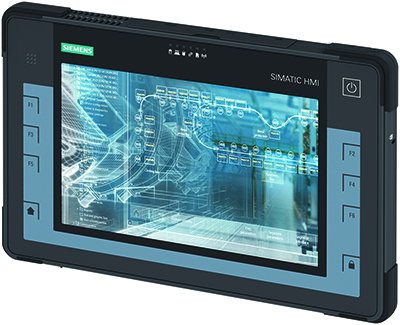
Connected worker tools provide the information needed to complete tasks from inside the plant using different types of well-known smart devices such as smart glasses, tablets, or smartphones.
Many cement plants use a central control room, where large monitors are set up to monitor the various processes needed to produce cement. If a process upset occurs, the operator may need to go into the plant to understand and resolve the cause of the upset.
The operator will typically take a radio so that they can call someone in the control room if a machine needs to be started – or the operator may have to return to the control room to start the machine.
In contrast, a connected worker would bring an electronic tablet rather than a radio when leaving the control room. The tablet provides access to the internal network so that, if needed, the machine can be started directly from the smart device while the operator is still in the plant – making troubleshooting easier.
This type of solution can also be implemented with maintenance personnel. In a typical cement plant, a maintenance technician is issued a work order and collects relevant information such as maintenance history, operations manuals and parts availability.
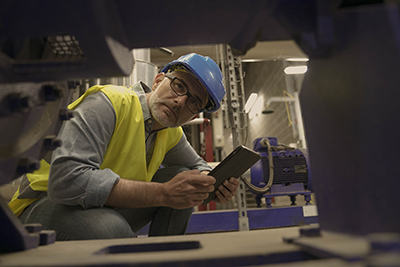
The technician will then go into the field to perform the maintenance. During this process, the technician may have to return to the maintenance shop to collect more information or contact an expert. In contrast, a connected worker is provided all the relevant information with the work order, on a mobile device that can be taken into the field.
Checklists can be provided to the technician to ensure all necessary steps in the process are followed and documented. If support from an expert becomes needed during maintenance, the mobile device can be used to contact support through email, text or phone.
This expert may be internal to the organization or technical support from the manufacturer. While connected to the expert, the technician can discuss the issue and share photographs as needed.
After completing the maintenance task, a technician with proper authorization can start the machine from the mobile device for testing. Once the testing is finished, the technician can log the maintenance using the mobile device and mark the work order complete. The system will then create a maintenance log that can be referenced while performing future maintenance.
Digitalization Consultants
Remote monitoring and connected worker tools are just two of many digitalization technologies currently available. These technologies advance quickly and the rate at which digitalization evolves is ever-increasing.
Given the number of tools on the market, keeping track of current solutions, where and how to use them, and different digitalization implementation strategies can be difficult. Some companies have chosen to use digitalization consultants to help in the digital transformation. A digitalization consultant will review the critical processes in the plant and discuss the digitalization tools available to optimize those critical processes. This type of consultant will also look for areas where existing measurements can be leveraged by a digitalization technology to improve the efficiency of the process.
Conclusion
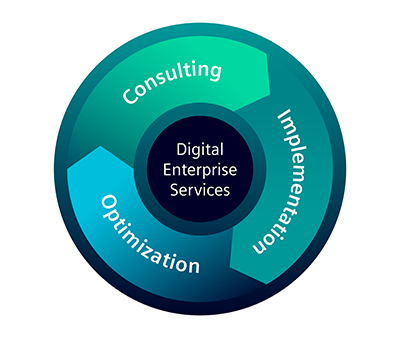
As with most industries, the cement industry faces unique challenges that it is working to overcome. In many cases, implementing digitalization technologies can be effective in reducing the impact of these challenges, but developing a strategy to implement these solutions can be difficult.
The digitalization journey should begin with identifying the organization’s digitalization goals and ensuring they are aligned with overall company goals. After determining these goals, identify areas where digitalization technologies can be implemented to address them.
Digitalization consultants can review the company’s goals and the measurements already being made to assist in determining the digitalization technologies that will best align with the digitalization goals of the plant and minimize how much equipment must be replaced for the implementation.
John Dronette is a product manager for Siemens Industry, Measurement Intelligence Business Segment. In this role he is responsible for sales support and marketing in the mining, aggregate and cement (MAC) industry. He has more than 30 years of experience in process instrumentation. During this time, he has held several roles in service and support, engineering, and product management. John has published numerous papers on the use of instrumentation in industrial applications. He has a BSEE from McNeese State University.
Jonas Norinder is a digital transformation consultant for Siemens Industry, where he identifies and promotes process optimization opportunities that help companies become more efficient, reliable and agile using technology, data, analytics tools and services. Since joining Siemens in 2006, he has held several roles within business development and sales, marketing, and communications. Jonas has presented on digital transformation topics at several industry conferences. He has a master’s degree from the Aarhus University in Denmark.