A Common Design Problem Is Fitting Belt Cleaners In The Optimum Locations.
By R. Todd Swinderman
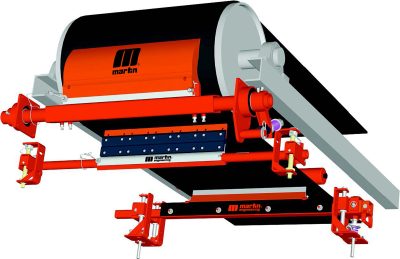
Knowing the location and number of belt cleaners required for a belt conveyor system is critical to improving safety, increasing component life and reducing clean-up costs. A common design problem is fitting belt cleaners in the optimum locations.
There are structural, spatial and safe access considerations that can offer limitations. Discharge chute configuration and installation of a dribble chute to capture extra discharge may also need to be factored into the design. This article will discuss design calculations for the location of secondary cleaners.
Placement and Positioning
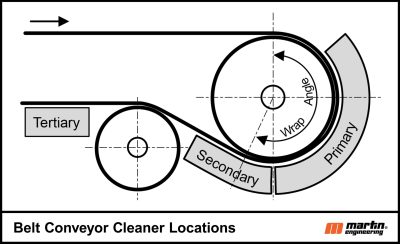
The Conveyor Equipment Manufacturers Association (CEMA) defines the secondary position as the space between the head and snub pulley on the return run of the belt. [Fig.1] Unfortunately, structural designs often result in a very short section of belt surface between the head pulley and the snub pulley which is the ideal location for many secondary cleaner designs.
This short distance allows little room for belt cleaners in the secondary position which is further complicated by the space needed for a dribble chute. In addition, designers often locate work platforms based on major components, overlooking access for belt cleaner inspection or maintenance.
Belt cleaners typically require more attention than major components to ensure system efficiency because the blades are wear components that must be maintained at optimal cleaning pressures.
Design and Installation Considerations
There are many simple options designers should consider:
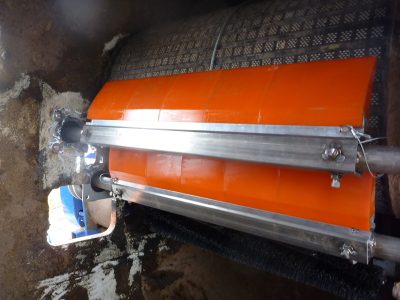
- Is the drive pulley wrap angle really needed or are you just applying it from habit? A common default wrap is 210 degrees created by the position of the snub pulley. The gap between the head pulley and snub is an ideal location for a secondary cleaner but the combination of pulley diameters and wrap angle may make mounting a secondary difficult and maintenance nearly impossible. We recommend utilizing an updated engineering design program that uses either the DIN or CEMA methods for the calculation of accurate tension values and the required wrap angle, ϴ.
- Consider using a larger diameter head pulley. Choosing a head pulley based on the minimum diameter may seem like it saves money, however, a larger head pulley can allow the installation of two cleaners in the primary position with enough snub pulley space for one or two cleaners in the secondary position, significantly reducing the amount of fugitive material. A larger head pulley can allow the installation of two cleaners in the primary position and enough snub pulley space for one or two cleaners in the secondary position, significantly reducing the amount of fugitive material.
- Place a priority on ergonomic access to the belt cleaners. Maintenance personnel can spend up to a third of their time merely gaining access to the equipment. Designing access to seldom-inspected or -maintained components based on minimum walkway codes raises costs. Consider structure and work platforms that allow belt cleaner inspection and maintenance.
- Consider using motorized drive pulleys. Motorized pulleys offer energy advantages and weight savings and open up space for belt cleaner installation and maintenance. Since all rotating components (including the main bearings) are located inside the pulley, the external stub shafts need minimal space to be mounted to the structure.
- Consider professionally trained installation. Belt cleaners must be mounted properly, often within ± a few millimeters, to perform optimally and limit the possibility of damaging the belt. Contracting with the belt cleaner supplier ensures proper installation with minimal adjustment and that the new chute will retain a clean professional look.
Calculating the Adequate Belt Tension
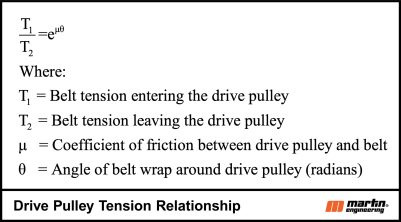
A critical design requirement is to determine the amount of wrap around the drive pulley required to provide the adequate conversion of torque from the drive into belt tension sufficient to move the belt without slipping.
It is interesting to note that the fundamental relationship describing this transfer does not depend upon the pulley diameter, only the coefficient of friction, µ, between the belt and pulley and the wrap angle, ϴ and the belt tensions required to prevent slip.
Secondary Belt Cleaner Location Geometry
Assumption: Top and bottom runs of the conveyor belt (X) are parallel entering head pulley and leaving snub pulley.
Variables:
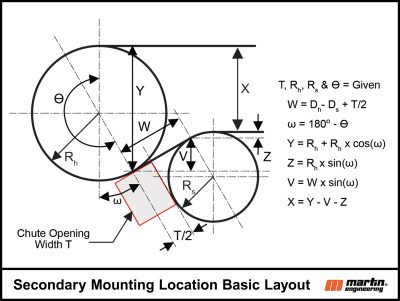
ϴ = Wrap angle of belt around head pulley.
ω = Wrap Angle, ϴ, – 180 degrees.
H = The height of the opening for the secondary belt cleaner blades and frame installation.
Rh = Radius of Head pulley plus lagging, plus belt thickness.
Rs = Radius of Snub pulley plus lagging, plus belt thickness. (Snub Pulley Diameter default value: 0.64 × head pulley diameter per DIN 22101).
T = The width off the opening for the Secondary belt cleaner blades and frame installation.
W = Length of belt segment tangent to both the head and snub pulleys.
X = Distance between top and bottom runs of the conveyor belt.
Y = The vertical distance between the top run of the conveyor belt on the head pulley and the tangent point where the belt leaves the Head pulley and starts the return run.
Some secondary cleaners must be mounted at least 50 mm from the point the belt leaves the head pulley so this offset also needs to be considered if required. In addition, the X dimension should be checked with the idler dimensions for adequate installation space.
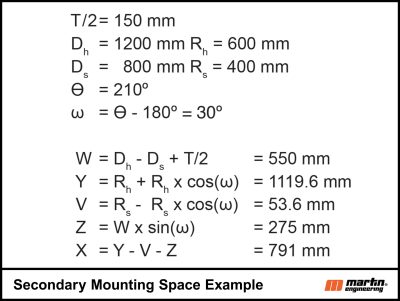
A similar analysis for the location of precleaners show that with a 1200-mm diameter head pulley, two primary cleaners can be installed in addition to a secondary cleaner. The addition of tertiary cleaners would be possible but may not be necessary if two precleaners and a secondary are mounted on the head pulley.
Conclusion
A belt cleaner system should be properly specified, designed and installed to gain the direct and indirect long-term cost benefits of reduced fugitive material, but compliance is an issue as well.
OSHA, 1926.1412(d)(1) and MSHA 75.362 state, “A competent person must begin a visual inspection prior to each shift the equipment will be used, which must be completed before or during that shift.”[1] Safe access with adequate space for installation, maintenance and inspection is critical to supporting longer system life and a lower cost of operation.
R. Todd Swinderman, P.E. is president emeritus of Martin Engineering and past president of CEMA. All photos copyright Martin Engineering 2025.
Reference
[1] Occupational Safety and Health Administration (OSHA), “§ 1926.1412 Inspections”, Dec, 2023. https://www.ecfr.gov/current/title-29/subtitle-B/chapter-XVII/part-1926/subpart-CC/section-1926.1412