By Mauro Nogarin
At the end of May, the Chilean company Cemento Melón inaugurated its fourth national cement production plant in the city of Punta Arenas, which is located 2,200 km south of the capital Santiago.
It is a cement plant that was carried out with an investment of $34 million and has automated facilities that incorporate the most recent technological and environmental developments in cement grinding plants.
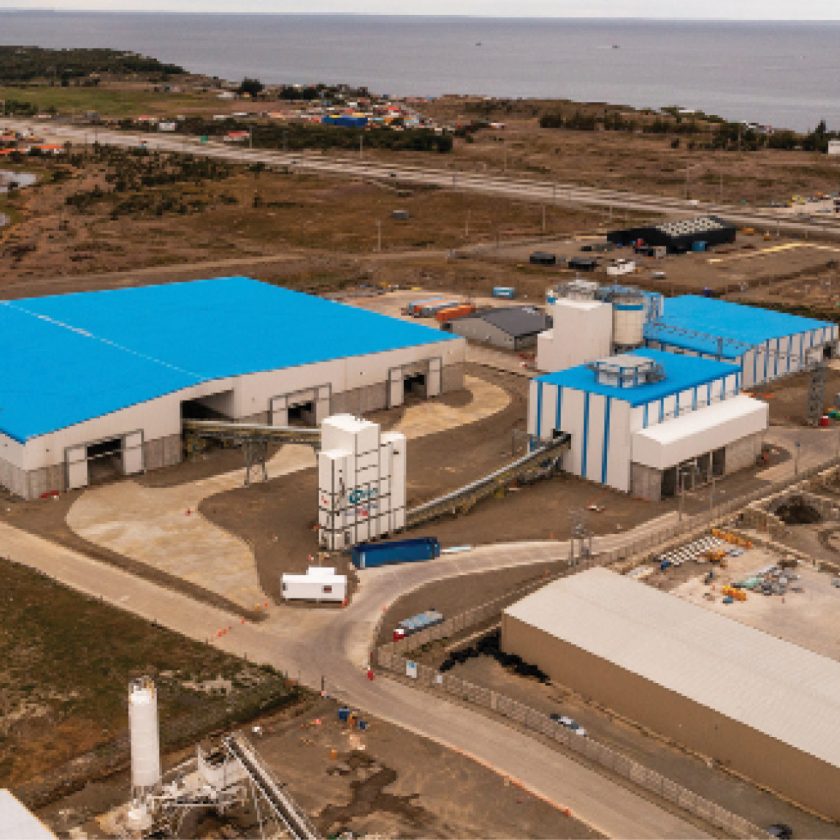
The plant has an initial production capacity of 110,000 tpy and the possibility of doubling its capacity. However, it had several months of production before being inaugurated, due to the increased demand for high-quality cement for the development of works of local infrastructure such as the expansion of the Carlos Ibáñez Airport and Puerto Mardones.
One of the main objectives that forced the company to build this new cement plant is to strengthen its position in the national market to face the expected boom of wind plants in the southernmost region of Chile, which will serve to generate green hydrogen, considered one of the main clean fuels in the world.
In fact, to date, Melón has already carried out the construction of 15 wind farms in other areas of the country, which so far include more than 630 built foundations, each of which involves between 500 and 1,200 cu. meters of concrete.
In recent years, Melón has expanded through the construction of different milling plants such as the one in Puerto Montt stage I in 2007 (ball mill), Ventanas in 2011 (vertical mill), Puerto Montt stage II in 2018 (ball mill), and Punta Arenas in 2021 (ball mill).
At the end of 2018, the company began using a new Plug&Grind Xtreme-type cement modular grinding unit from Cemengal at its Puerto Montt plant, constituting the first mill of its kind to be installed in Chile.
After that, it was decided to install a similar mill, but this time in the industrial zone of the city of Punta Arenas in Chile.
Melón, together with Cemengal, carried out the project for this grinding station throughout 2019. Its construction was slowed down by the pandemic and the plant could only be started up in September 2021, the date on which its first tons of cement were produced.
The Punta Arenas Plug&Grind Xtreme unit was chosen in a modular format, to speed up all the logistics and assembly tasks of the structure. It has low energy consumption in production and incorporates modern filtration and capture systems for dust emissions into the atmosphere in compliance with the strictest international environmental standards.
The advantages related to the compact and modular format of Cemengal’s Plug&Grind-type modular plants have been key to meeting the deadlines and quality criteria that Melón produces.
The process begins with the reception of the different raw materials, of which two of them arrive by sea to the area, which involved the construction of an ecological hopper, ensuring the discharge of clinker and plaster.
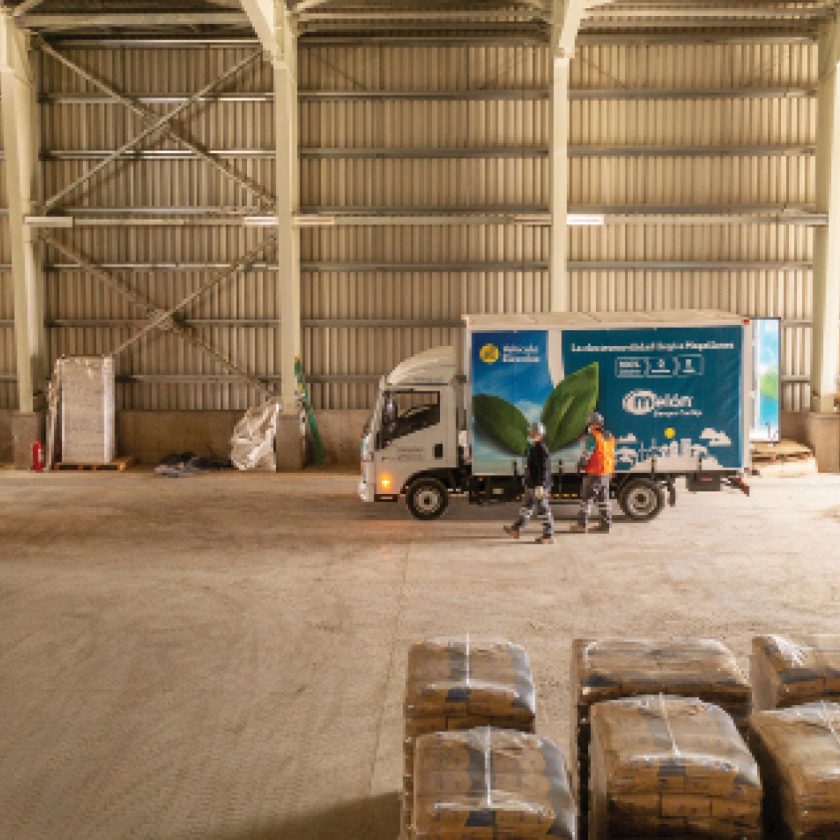
The material is unloaded from the ship by means of shovels to this hopper, and from there the trucks that transport the material to the plant are loaded, where it is stored.
The construction of three warehouses with a total capacity of 60,000 tons allow raw materials such as clinker, pozzolan and plaster to be stored and protected from the weather. These three materials are transported to hoppers and weighing belts; they are dosed and weighed with precision to control the quality of the product.
Once the material is dosed, it enters a two-chamber ball mill with a production capacity of 250,000 tpy. A separator performs the final classification of the product based on its fineness. The cement is transported by a pneumatic system to the final storage silos, that is, two silos of 500 and 1,000 tons, for each of the two types of cement produced.
The packaging in bags is carried out by using Ventomatic equipment with an in-line stretch wrapper, which allows the pallet to be plasticized and protects the packaged cement from inclement weather. The plant also has a system for bulk truck loading and for the preparation of 1,500-kilo bags.
Today, the plant produces in three formats – bulk, bags and maxi-bags – and produces two types of cement: Melón Extra and Melón Magallánico, the latter which is specially designed for cold areas, where temperatures can reach up to 15 degrees below zero.
The Magellanic cement is a special mixture of raw materials and the result of which is that it achieves high resistance with less setting time, even in low temperature conditions. In this way, it achieves its “early resistance” quality, which allows it to be demolded in shorter periods of time, thus generating shorter construction times, with the consequent cost savings.
Mauro Nogarin is Cement Products’ Latin American correspondent.