Nestled In Limestone-Rich Indiana, A New Flagship Plant Leaves No Doubt That Heidelberg Materials North America Is All In On Negating Carbon Dioxide Emissions.
By Don Marsh
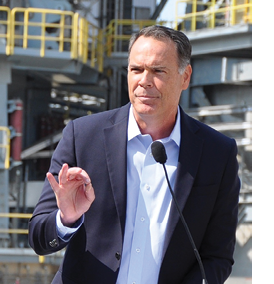
On a scale of new clinker capacity – and environmental metrics tuned to carbon-minded market and regulator sentiments – no North American and few cement plants globally will match Heidelberg Materials’ rebuilt Mitchell, Ind., operation any time soon. With a single kiln equal to output of 7,000 metric tons daily or up to 2.4 million mt annually, it triples the tonnage potential of its successor – a three-kiln line evolved from a 1902 mill whose builders knew how to prove and exploit a premium limestone deposit.
The Heidelberg Materials Mitchell team dubs its new workhorse K4. The 80-meter kiln anchors the continent’s second highest output operation of its kind, trailing only the 3.6-million-mtpy capacity Holcim US Ste. Genevieve plant (2010) along the Mississippi River. In addition to three pre-1980 kilns, K4 can shoulder clinker production volumes from a Speed, Ind.operation that Heidelberg Materials is converting for grinding and cement distribution.
At or near full capacity, the new Mitchell plant will effectively double Indiana legacy lines’ volume. To accommodate markedly higher throughput, Heidelberg Materials incorporated a 154,000-mt clinker storage dome in the new production footprint and expanded the adjacent distribution terminal with 32,000 mt of storage plus infrastructure for 1,000 additional railcars. Rail alternatives to bulk tanker deliveries for more Mitchell customers will translate to fuel savings and lower carbon dioxide emissions associated with finished concrete slabs and structures.
“We will be able to supply our customers more efficiently, consistently, and sustainably than ever before,” said Heidelberg Materials North America CEO and President Chris Ward. “We have brought the best knowledge available globally and collaborated with federal, state, regional and local officials to make the Mitchell plant the model it is.”
The final phase of the central-south Indiana operation’s $650 million upgrade entails build-out of a highly automated, 3,600-bag/hour blended cement and masonry cement packaging line.
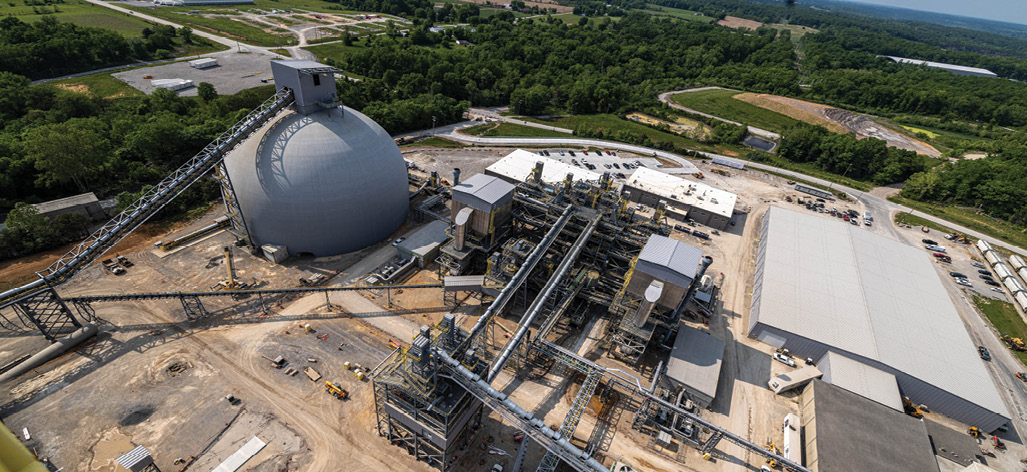
PHOTO: Heidelberg Materials North America
Center Stage
As a successor to the 2-million-mtpy Union Bridge, Md., mill, the new Heidelberg Materials North America cement flagship represents far more than a capacity exercise. Indeed, Mitchell is poised to become a global market leader’s case study in CO2 emissions reduction. That thorny challenge has invited unprecedented interest in cement production intricacies from customers and their contractor, engineer, design and owner clients across construction; government agencies or officials at all levels; plus climate technology developers or investors.
Between corporate and regional headquarters in Germany and Texas, Heidelberg Materials has equipped Mitchell to a) produce ASTM C150 Type I/II cement at sharply (> 45%) lower CO2 emissions levels against a 1990 baseline; and b) parlay the company’s branded EcoCem portland limestone cement, ASTM C595 Type IL, as a lower carbon alternative for concrete mix designs with traditionally prescriptive Type I/II specs.
CO2 emissions reduction and clinker optimization answer calls to action in parallel Roadmap to Carbon Neutrality by 2050 documents from the Portland Cement Association (PCA) and Global Cement and Concrete Association (GCCA), of which Heidelberg Materials North America and its parent company are members.
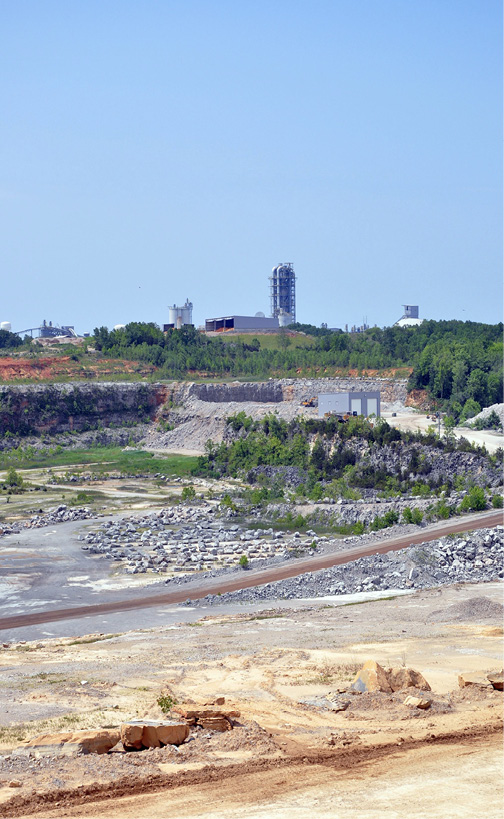
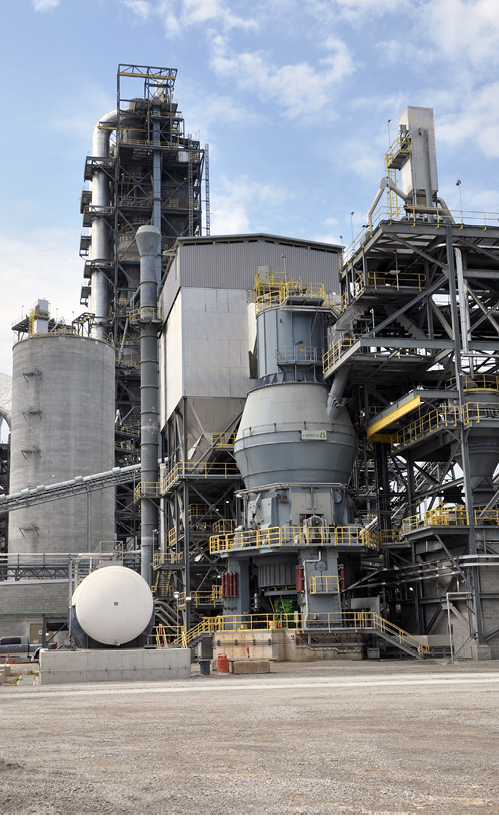
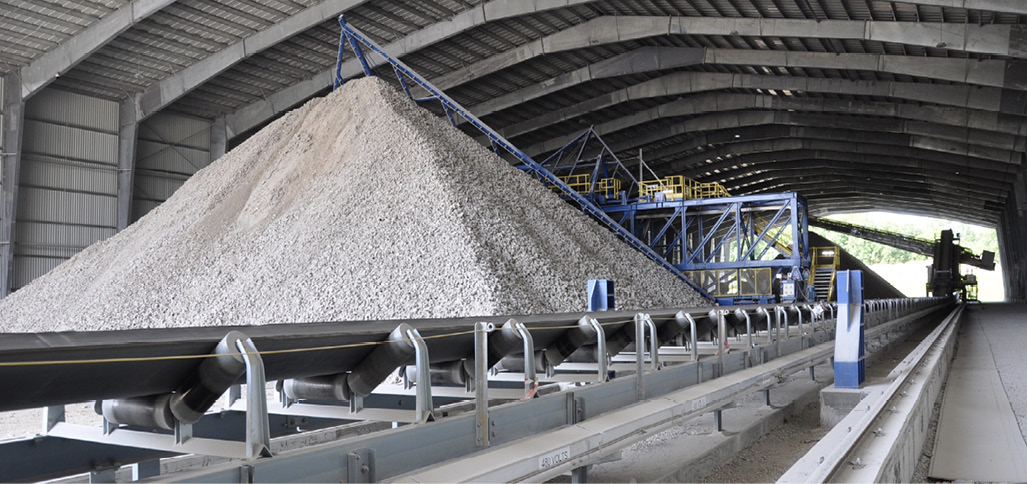
production and EcoCem Portland Limestone Cement. Key to the plant upgrade is a new enclosure for a limestone stacker/
reclaimer with 66,000 tons’ handling and storage capacity, plus Loesche vertical roller mills charging a 13,000-metric ton raw
feed silo (left, above) and EcoCem finishing lines (note cover image).
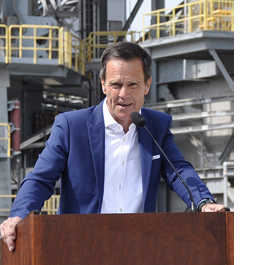
Carbon Negativity
At Mitchell, the most immediate and impactful measure abiding PCA and GCCA Roadmap goals is the use of natural gas to fuel K4 and its calciner, a departure from the retired kilns’ coal power. Quarry and finishing mill upgrades enable a nearly exclusive focus on producing EcoCem, with 5-15% limestone as Type I/II substitute.
Fuel choice and blended powder output at Mitchell will contribute to two metrics at the center of Heidelberg Materials’ enterprise-wide emissions commitments through 2030, both with 1990 baselines: A reduction of 750 kg to 400 kg of CO2 per metric ton of cementitious material output and a lowering from 82% to 68% of the clinker factor (i.e., Type I/II only) in subsidiaries’ ready mixed concrete deliveries.
“Mitchell capacity, operating efficiencies and finishing capabilities substantially contribute to our offering of low-carbon cement and concrete,” Heidelberg Materials Chairman Dr. Dominik von Achten told North American customers, colleagues and state or local allies at a June ribbon cutting. “The plant represents a commitment to further strengthening our North American footprint and increasing the sustainability of our products.”
Mitchell is on track to become the first decarbonized cement operation in the country, he added, owing to the proposed capturing and processing of 95% of the CO2 in calciner and kiln flue exhaust. Heidelberg Materials has launched a feasibility study for a carbon capture and storage (CCS) facility capable of injecting purified CO2 into an Illinois Basin reservoir below two impermeable, sub-water table geological layers.
Through its Office of Clean Energy Demonstrations, the U.S. Department of Energy is matching the producer’s $5 million commitment to the study, which continues work the agency supported through prior awards or grants. CCS infrastructure construction at Mitchell would follow a similar project under way at the Heidelberg Materials Edmonton, Alberta cement plant. Both North American facilities are to be modeled on a sister Norway operation whose scheduled 2026 deployment will position Heidelberg Materials with the first CCS-equipped cement plant the world over.
Don Marsh is the editor of Concrete Products magazine, sister publication to Cement Products.
Concrete mixes for main office and lab tilt-up wall front elevation, along with the clinker storage dome (right background) bear Heidelberg Materials EcoCem Portland Limestone Cement, the new plant’s principal offering. Along with administrative functions, the office houses a lab whose robotics expedite testing and quality control checks of raw material, clinker and finished cement samples delivered by pneumatic tube from across the operation.
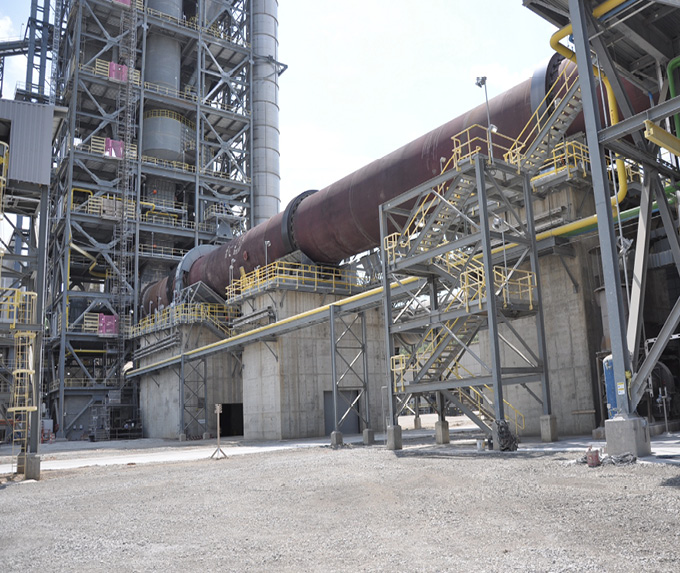
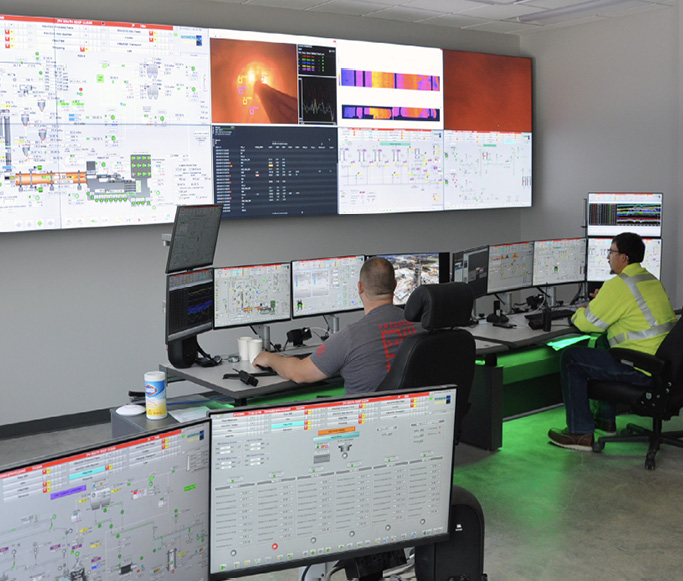
Georgia-based Humboldt Wedag Inc. oversaw Mitchell project design and engineering, including the principal components or features shown here: Threepier 80-meter long, 5.4-m diameter kiln, outfitted with fixed shell cooling fans; 164-ft. high, 219-ft. clinker storage structure, built by Dome Technology; and control room programmed around the Siemens Cemat platform. Between German parent KHD and domestic operations, Humboldt Wedag delivered the kiln; double-string five-stage preheater; Pyroclon LowNOX AF calciner; plus Pyrotop mixing chamber and high-efficiency cyclones. Other principal suppliers include Loesche America Inc. (vertical roller mills); Bedeschi America Inc. (stacker, reclaimer, clay equipment and pipe cement conveyors); IKN GmbH (clinker cooler); Redecam Group (air pollution controls); and, Howden Group (fans).
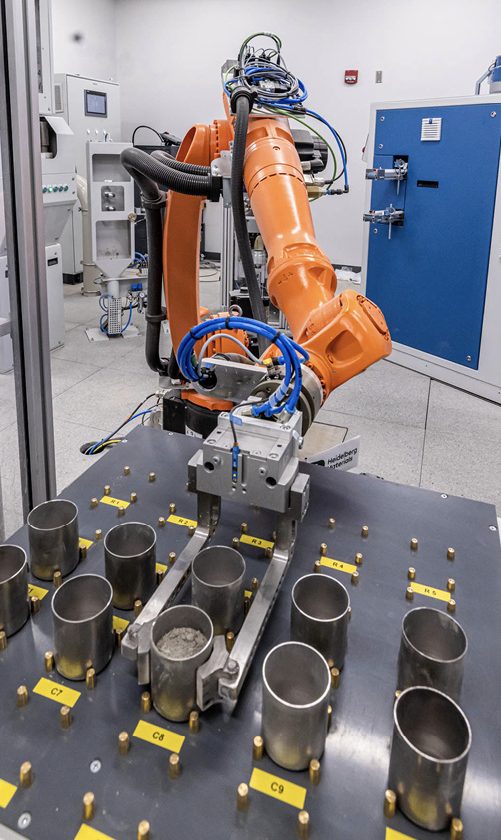
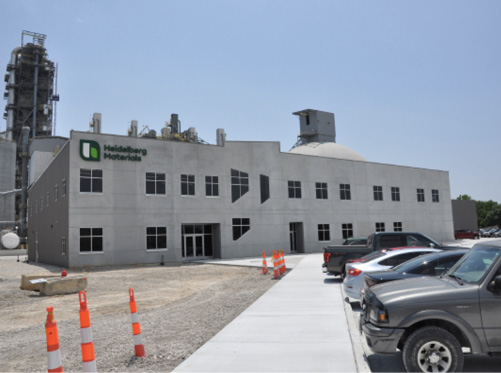
Concrete mixes for main office and lab tilt-up wall front elevation, along with the clinker storage dome (right background) bear Heidelberg Materials EcoCem Portland Limestone Cement, the new plant’s principal offering. Along with administrative functions, the office houses a lab whose robotics expedite testing and quality control checks of raw material, clinker and finished cement samples delivered by pneumatic tube from across the operation.