A Lack Of Regular Cleanings Can Lead To Reduced Storage Capacity, Lost Material, Blockages And Even Structural Damage.
By Dennis Blauser
Silo cleaning is a critical part of any facility’s maintenance schedule. Without regular cleanings, stored material can become compacted, leading to reduced storage capacity, lost material, blockages and even structural damage.
This can have a serious impact on a facility’s bottom line. In this article, we’ll cover the importance of silo cleaning, the warning signs that a silo needs to be cleaned, the common cleaning methods used, the steps operators can take to avoid cleaning emergencies, and the importance of regular silo cleaning for safety and efficiency.
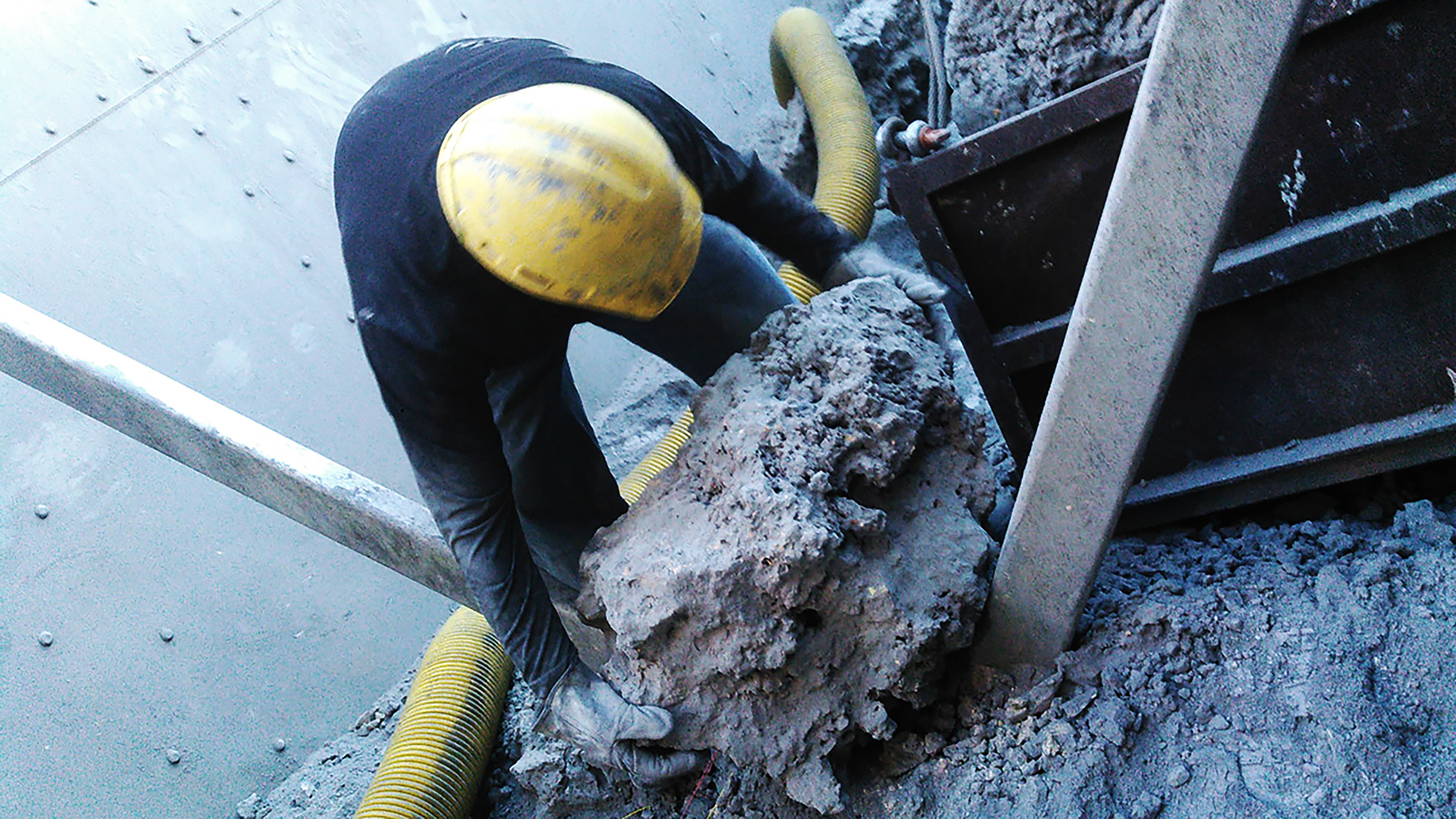
Why is Silo Cleaning Important?
When silo cleaning is not part of a facility’s schedule, there is a risk of reduced storage capacity, lost stored material, blockages and potential structural damage. All of these issues cut into a producer’s bottom line.
Over weeks, months, or even years, stored material can become compacted or buildup on interior walls, regardless of whether a concrete or steel silo is used to store cement, slag, lime, or another aggregate. As product builds up inside a silo year after year, the lost product write-offs add up. This buildup also means there is less room in the silo to store material. While this damage to profits is evident over time, potential damage to the silo structure remains hidden.
Cement storage silos are susceptible to both product buildup and compaction or hydration. Cement hydration from leaks or ambient humidity causes the stored product to solidify in the silo. Particularly in the case of stored cement, silos must be watertight. Even a hairline crack can allow water intrusion, damaging stored material and leading to buildup and blockages.
Proper material flow through the silo is critical to the structure’s longevity. Poor material flow can create problems in loading/unloading efficiency and uneven internal loading. The silo’s internal concentric strength is based on evenly distributed pressure from the loaded material on the inside of the wall.
Poor internal flow can cause material to accumulate on one section of the silo wall interior, which is known as asymmetric flow. The resulting disruption to material flow can exceed the wall’s concentric pressure and potentially lead to bowing, cracking, or even wall failure. When silo flow is slowed and the capacity is compromised, it’s time to call a silo cleaning professional.
Choosing a Silo Cleaning Company
When hiring a professional for silo cleaning services, facility managers must ensure they look for a silo cleaning company with the proper experience. They should know safety protocols when working around hazardous materials and operate cautiously using specialized tools and techniques to quickly and efficiently remove buildup within a silo.
Silo cleaning professionals should be trained in the safest and most efficient methods of clearing buildups from concrete and steel silos so that operations can continue smoothly. By utilizing specialized equipment designed specifically for this purpose, they can quickly clear away any material buildup within a silo without causing damage to its structure.
Additionally, these professionals can work within tight timelines while providing thorough cleanings that will ensure maximum storage efficiency and reduce the chances of blockages or clogs occurring in the future. Full-service silo companies are those that service all aspects of silos, including cleaning, inspection, maintenance, as well as repair, restoration, construction, and design.
The benefit of using a full-service silo company for your cleaning is that you can bundle your silo inspection and cleaning together to reduce downtime and ensure all areas of the silo interior are visible during the inspection. A full-service company is also often equipped to make minor repairs in the same mobilization, saving you time and money.
Case Study
Marietta Silos is a full-service silo company that offers cleaning, inspection, and maintenance services through its sister company USA Silo Service. Together the companies service concrete and steel silos and storage tanks for a variety of industries. USA Silo Service was recently called out to complete a cleaning project for a repeat client with four 40- x 12-ft. slag silos at their cement facility in Wisconsin.
Challenge
Slag, or sand, used in certain cement mixes is stored in steel silos or tanks. Before being stored, slag is put through a dryer that makes the aggregate extremely hot. Slag storage silos are refilled every day. The extreme temperature difference between the newly dried slag and the storage container causes the interior walls of the steel tank or silo to sweat. This causes thin layers of slag to build up on the silo walls.
Solution
To remove this buildup and restore the tank to full storage capacity, slag silos must be cleaned every year. The slag silos for this facility are housed inside a metal building near the drying kiln, which results in a temperature difference of 20°F. The extreme heat makes cleaning a more intensive job for silo technicians.
To ensure the safety of technicians and complete the cleaning job as quickly as possible, USA Silo Service uses a specialized silo cleaning system known as The Boss. This cleaning method includes a proprietary, enhanced pneumatic system designed to remove large volumes of material buildup in a short amount of time. The proprietary system removes more material faster and more efficiently than other clean-out methods, accelerating the cleaning process by minimizing downtime and time on location, resulting in immediate cost savings.
Outcome
The client’s cement facility now has four clean slag silos with maximum storage capacity. USA Silo Service’s fast and efficient team completed the process in two days. The Boss remote silo cleaning system made the entire process easier and safer for the silo technicians.
Since the proprietary cleaning method used by USA Silo Service is able to remove more material buildup than conventional methods, it also ensures that the customer can often wait a full year before the next cleaning, rather than scheduling multiple cleanings per year. The client was also able to quickly put their silos back to full capacity with minimal mess and disruption.
Silo Cleaning Methods
Common silo cleaning methods include a basic whip method, which involves lowering a head equipped with rotors into the silo to cut away hardened material; the pneumatic whip system, which uses compressed air to “blast” the compacted material loose; or the enhanced pneumatic silo cleaning system. The enhanced pneumatic silo cleaning method used by USA Silo Service offers superior performance and safety features compared to conventional methods without sacrificing efficiency or effectiveness.
By utilizing The Boss silo cleaning system for regularly scheduled maintenance, operators can ensure their facility’s storage capacity remains optimal while minimizing any potential risks associated with manual cleaning.
Furthermore, using The Boss allows operators to save money by reducing operational costs while achieving excellent results in shorter periods than was previously possible with traditional techniques. The Boss silo cleaning system from USA Silo Service includes a specialized tool designed to quickly and effectively dislodge compacted material.
In addition to specialized silo cleaning methods, USA Silo Service uses a vacuum truck to remove the remaining material from the bottom of the silo. This recovered material is collected in the truck and either returned to the facility for sale or properly disposed of, depending on the quality of the recovered material. If returned to the facility for sale, it can help offset some of the costs associated with routine cleanings.
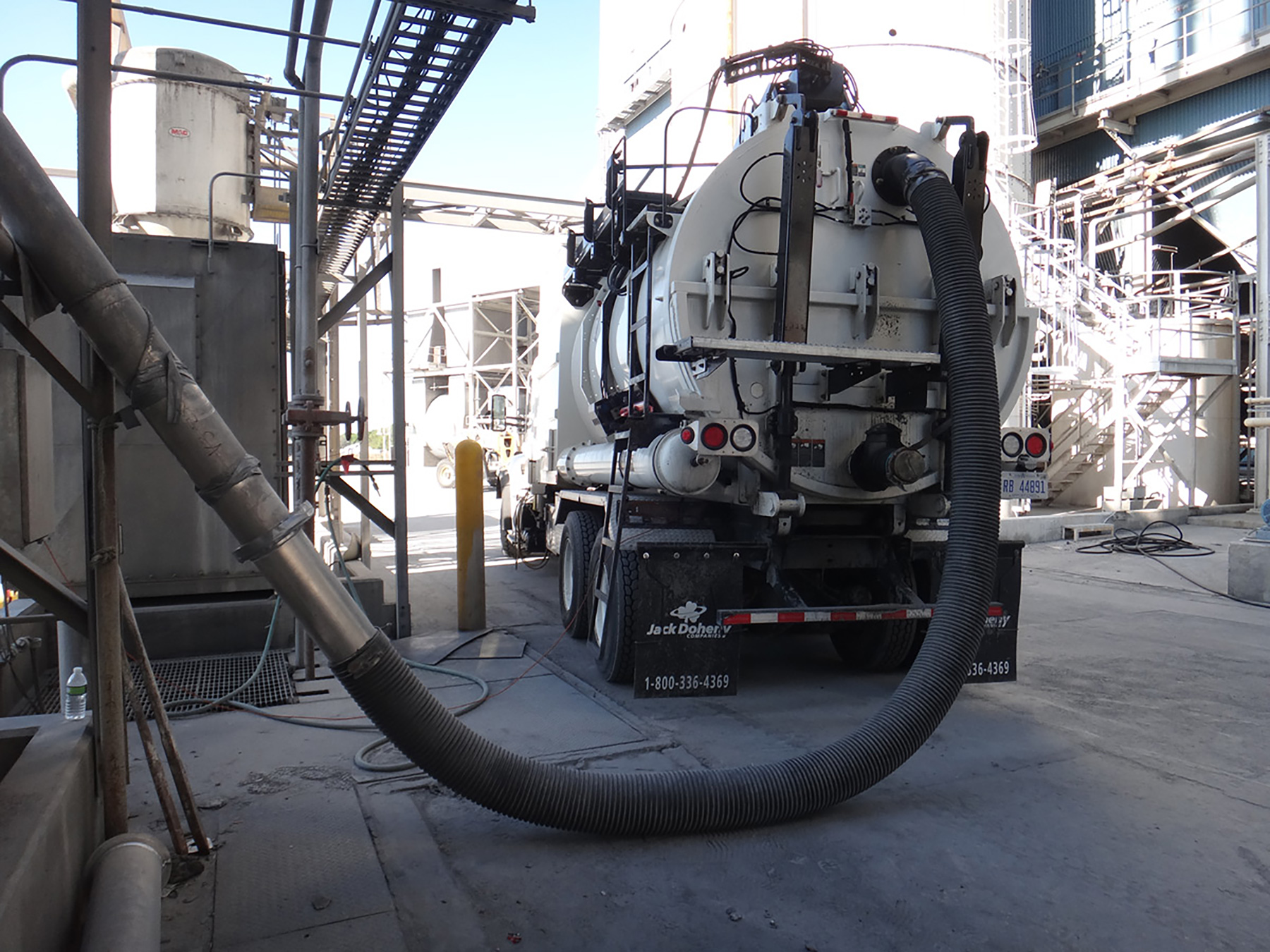
Conclusion
Regular silo cleaning keeps the job site safe. Material buildup within the silo increases the potential for structural failure or collapse, risking productivity and workers’ safety. Silos that are not properly maintained are dangerous to everyone around them.
In addition to regular silo cleanings, there are some steps that silo operators can take to avoid cleaning emergencies. Operators should control material compaction by frequently emptying material from the silo, as material that sits over an extended period is more likely to become compacted.
It is also important to avoid hydration of the stored material. Utilizing well-maintained fluidizing equipment can help. Regular silo inspections completed on an empty silo can also help ensure the silo roof and other areas are in good repair and free of leaks. While these measures can help, it is still important to schedule routine cleanings.
A significantly lower storage capacity, clumps or chunks of material coming out of the silo, or the observation of a diminished flow are warning signs that a silo is experiencing one of these conditions. These are also signs that it is time to call in cleaning professionals.
In conclusion, facility owners need to stay vigilant when it comes to maintaining their storage systems. Regular inspections and scheduled cleanings help keep operations running smoothly and ensure proper storage capacity for stored materials.
Dennis Blauser is the CEO of Marietta Group, which includes Marietta Silos Inc., Marietta Inspection Services and USA Silo Service.