Justifying Safety Investments Is Greatly Enhanced By Quantifying What Most Financial Managers Refer To As ‘Intangible Costs.’
By Dennis Blauser
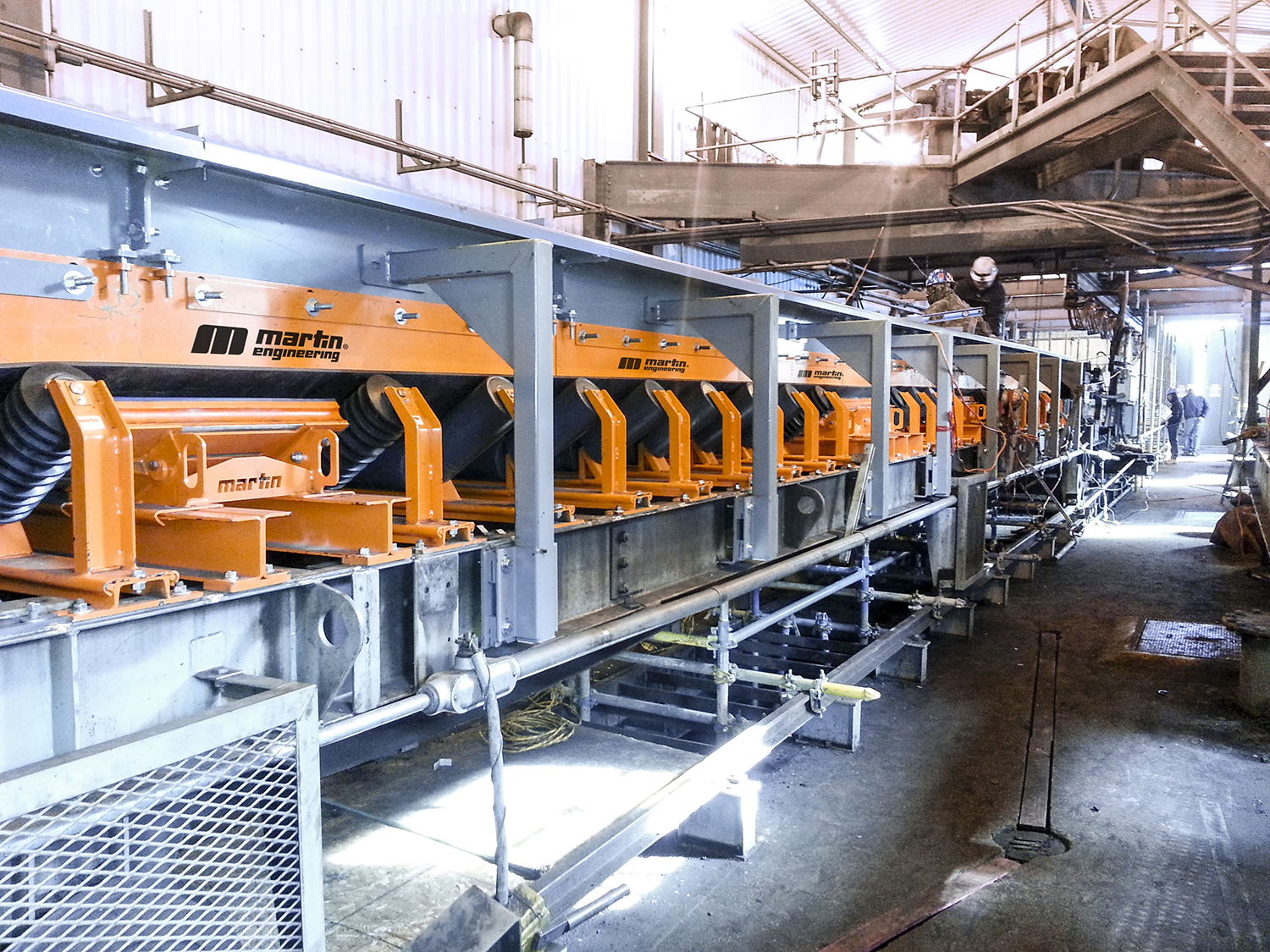
Conveyor safety is not a modern trend bred by government regulation; it’s a common-sense idea as old as the first conveyor design. In the modern age, safety is a key factor in worker protection, reduced insurance rates and a lower total cost of operation. There are several hurdles to the installation of safety equipment, the biggest of which is the near-universal use of the Low Bid process.
When companies buy on price (Low Bid) the benefits are short-lived and costs typically increase over time. In contrast, when purchases are made based on lowest long-term cost (Life Cycle Cost), benefits usually continue to accrue and costs go down, resulting in a net savings over time [Figure 1]. Safer and more reliable equipment is easier to service, has a longer life and is less expensive to maintain.
Organizations that embrace safety show significant performance advantages over the competition. The proof is reflected in reduced injuries and greater productivity, along with above industry average financial returns and higher share prices.
Justifying safety investments is greatly enhanced by quantifying what most financial managers refer to as “intangible costs,” i.e., injuries, lost labor, insurance, morale, legal settlements, etc. However, managers and accountants have been trained to think about saving direct costs to justify investments.
When conveyors don’t operate efficiently, they have unplanned stoppages, release large quantities of fugitive materials and require more maintenance. Emergency breakdowns, cleaning of excessive spillage and reactive maintenance all contribute to an unsafe workplace.
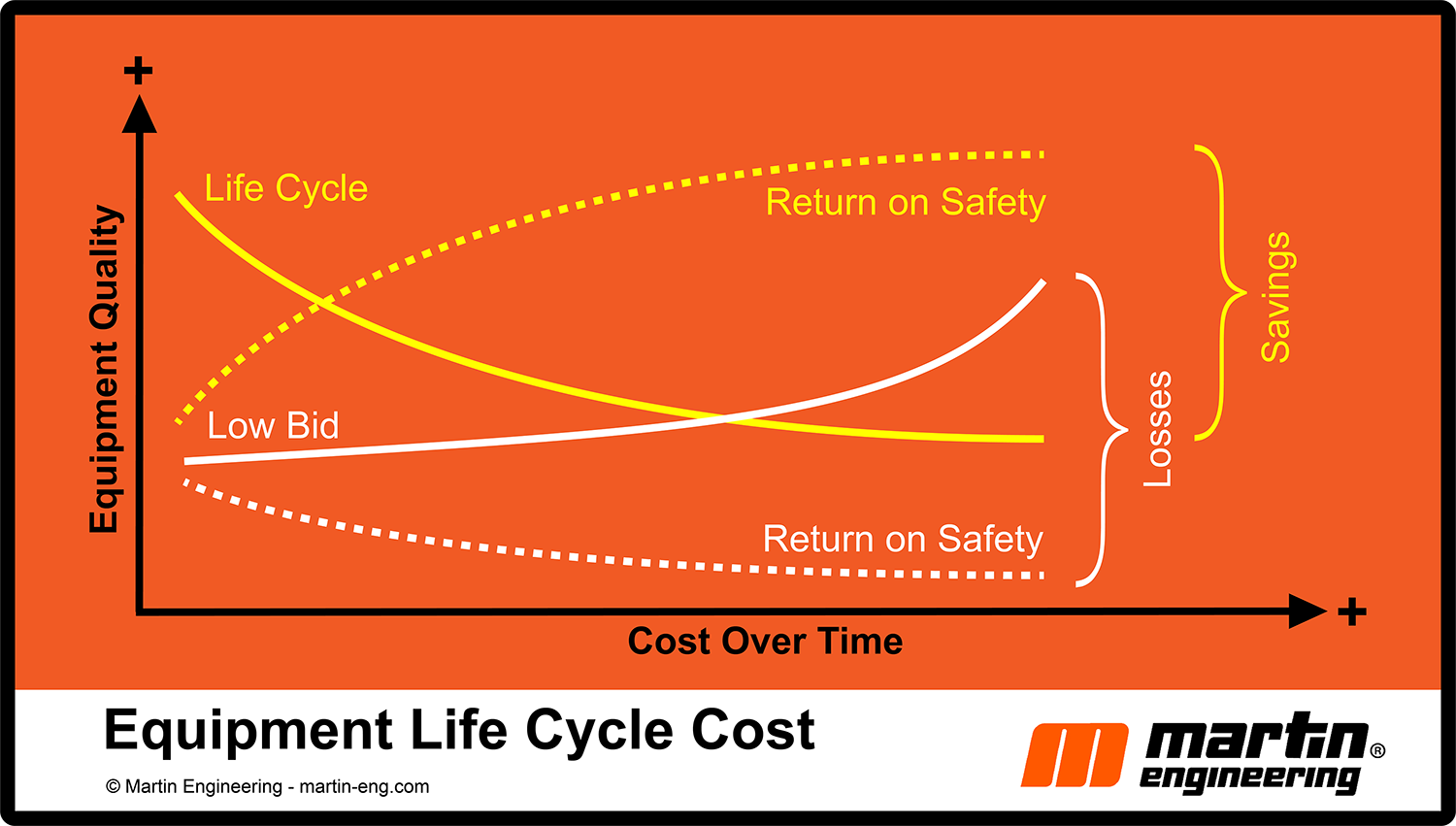
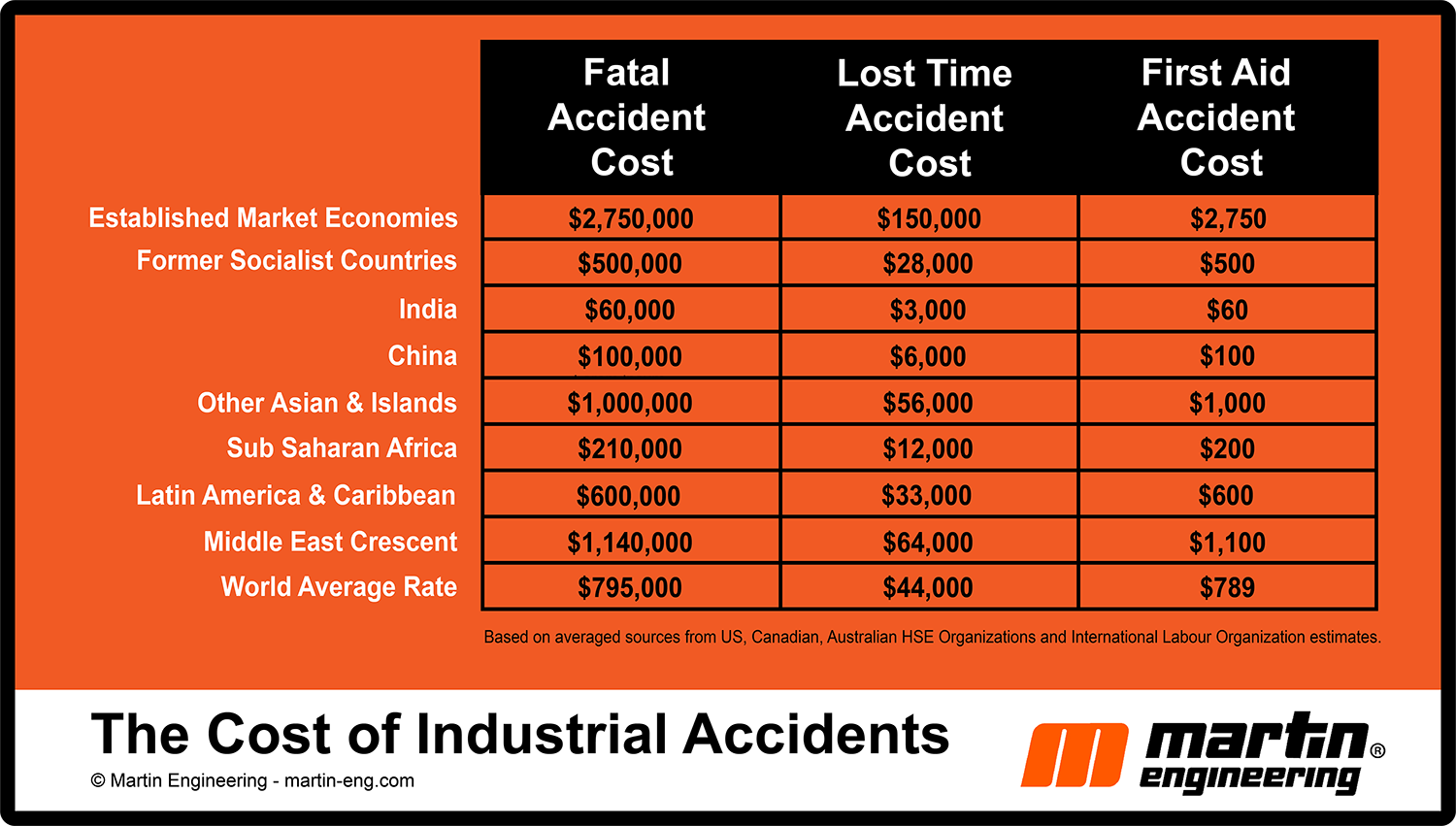
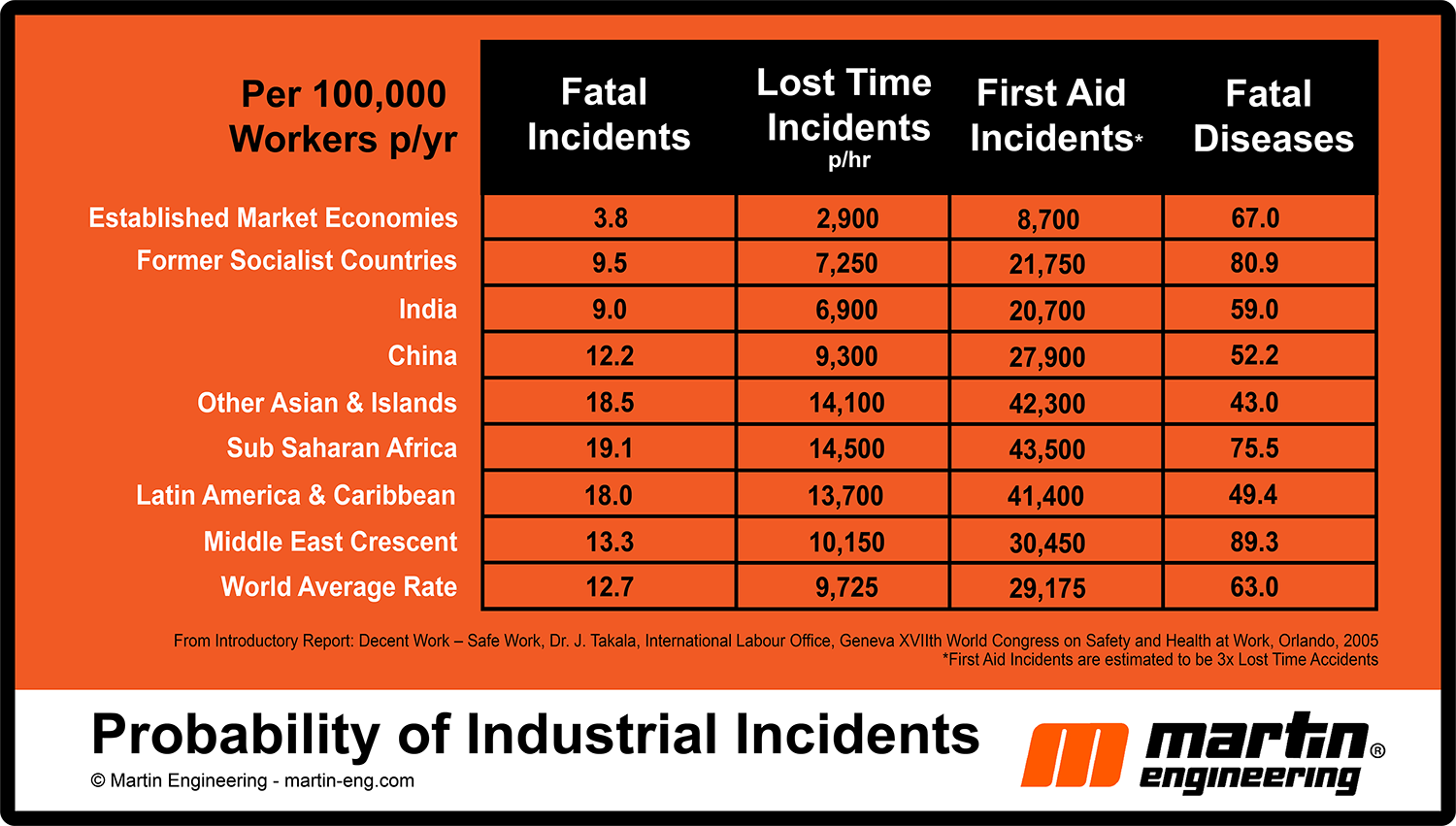
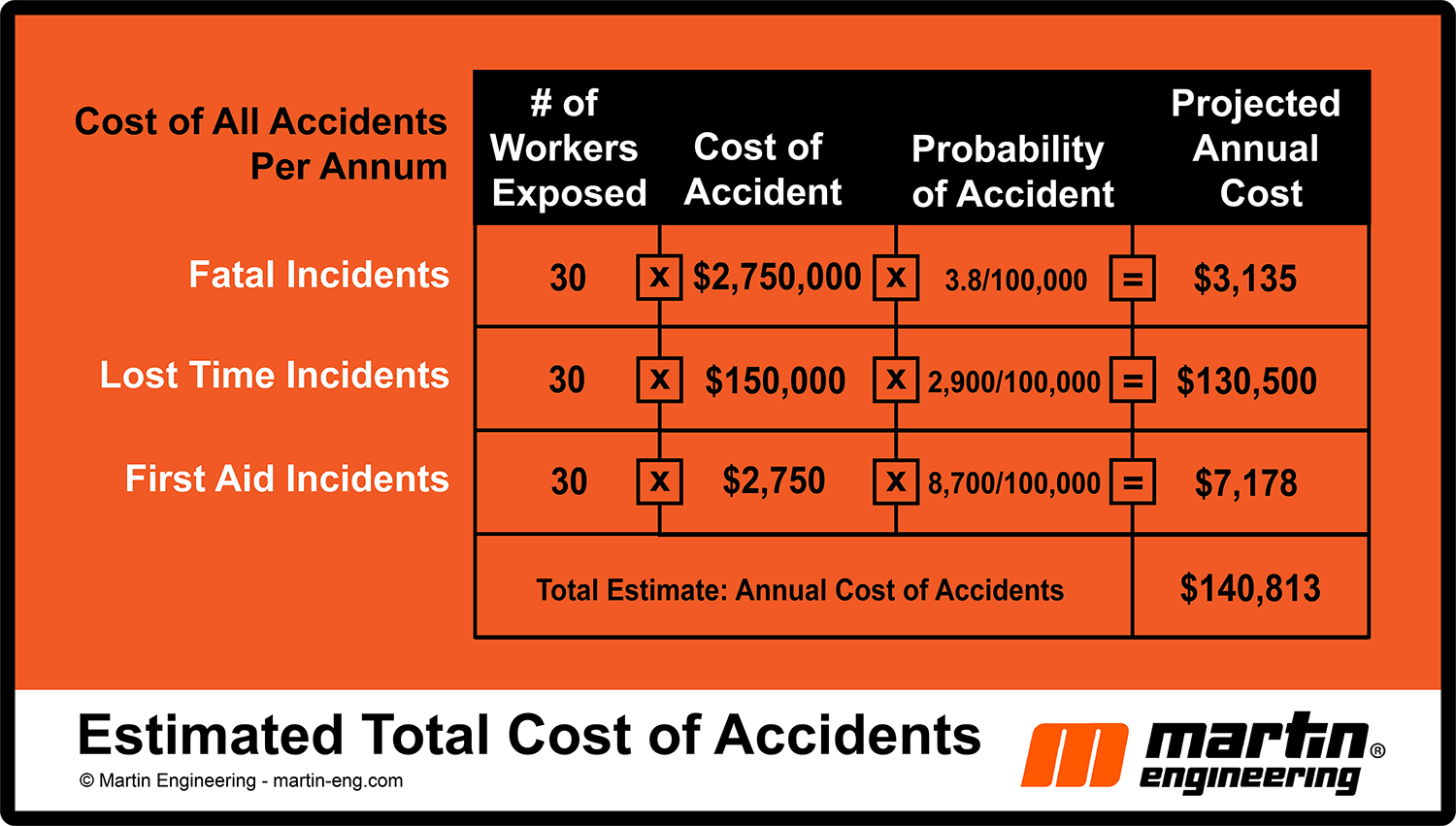
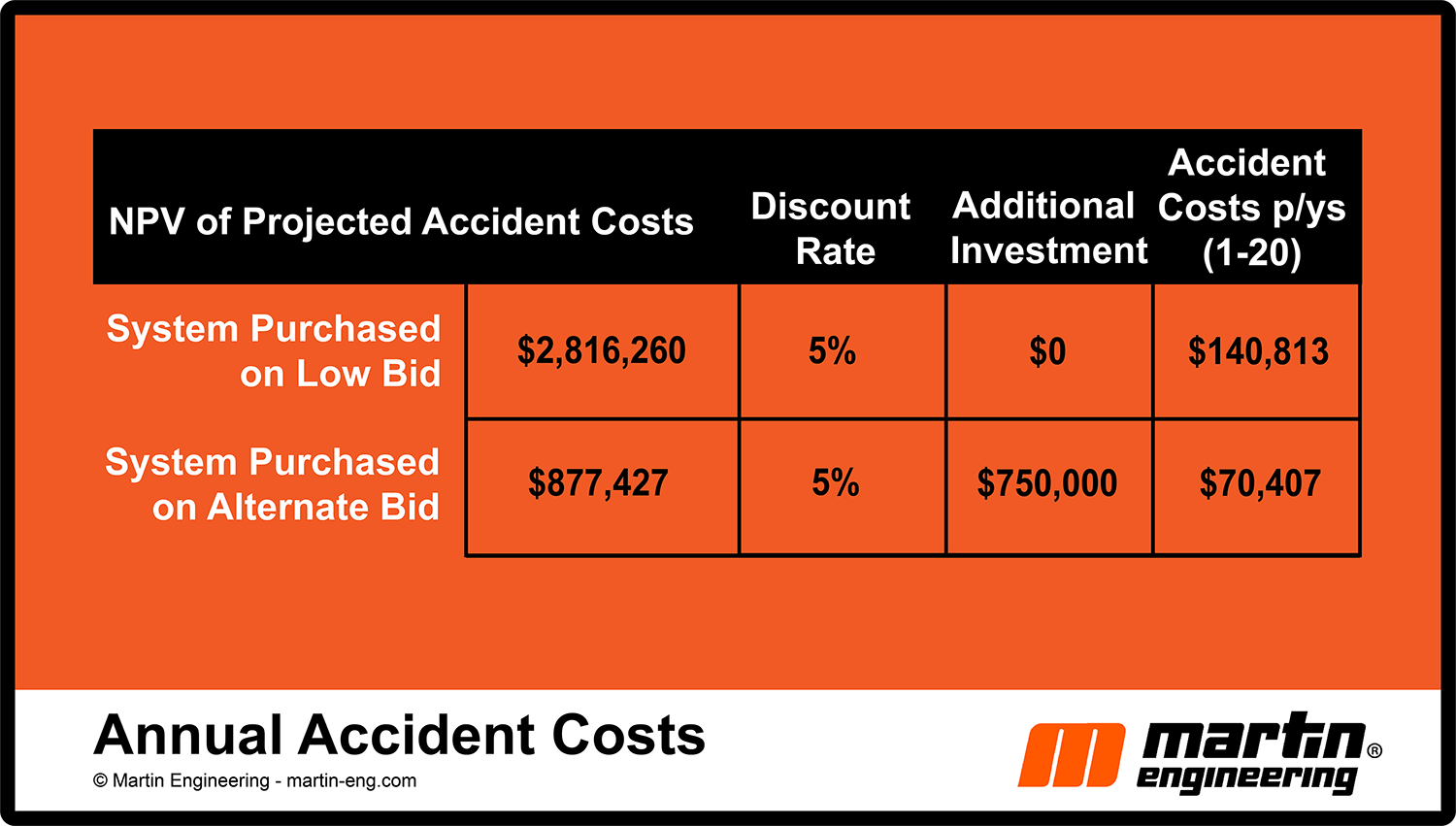
Safety Pays
Numerous case studies revealing the positive relationships between safety and productivity are backed up by organizations that gather global statistics on accidents and incidents. The simple formula for return on investment (dividing savings by cost) does not capture the potential savings from safety investments. Several organizations provide detailed and regional statistics on the cost of accidents [Figure 2].
Lacking specific historical data, managers can turn to numerous reliable sources that provide the probability of incidents that can be used to estimate tangible and intangible future costs [Figure 3].
The financial technique used to compare options is called a “net present value” (NPV) analysis. NPV compares different investment options with varying costs and savings (cash flows) over time, discounting them by the company’s cost of money. For example, an internal risk analysis shows a facility has 30 workers exposed to conveyor hazards. The estimated probability of the different classes of accidents (fatal, lost time and first aid) is multiplied by the cost of these accidents to reveal what could be invested to reduce the incident rate by half [Figure 4].
Assuming the life of the conveyor is 20 years and the cost of money (discount rate) is 5%, the available additional investment would be about $750,000 more in design time to accomplish the 50% improvement in safety. By choosing the lowest-priced bid to meet the minimum safety requirements, the short-term expenditure ends up costing considerably more over the 20-year lifecycle [Figure 5].
By spending $750,000 more to exceed the minimum safety and design requirements and reduce the accident rates by 50%, the annual projected cost of accidents drops from $140,813 to $70,407.
Measured in today’s dollars – including the additional investment of $750,000 – the projected savings over the 20-year term at 5% are about $1.2 million by investing more upfront.
If, after further analysis, the savings are found to be less – perhaps only a 25% reduction in the cost of accidents – the upfront investment is still justified over the long term. Even though it takes a little more effort to collect data and do a financial analysis, in the end, NPV consistently proves that safety does indeed pay.
R. Todd Swinderman is CEO Emeritus, Martin Engineering. Martin Engineering has been a global innovator in the bulk material handling industry for more than 75 years, developing new solutions to common problems and participating in industry organizations to improve safety and productivity. The company’s series of Foundations books is an internationally recognized resource for safety, maintenance and operations training – with more than 22,000 print copies in circulation around the world. The more-than-500-page reference books are available in several languages and have been downloaded thousands of times as free PDFs from the Martin website. Martin Engineering products, sales, service and training are available from 17 factory-owned facilities worldwide, with wholly owned business units in Australia, Brazil, China, Colombia, France, Germany, India, Indonesia, Italy, Mexico, Peru, Spain, South Africa, Turkey, the USA and UK. The firm employs more than 1,000 people, approximately 400 of whom hold advanced degrees. For more information, contact [email protected], visit www.martin-eng.com or call 800-544-2947.
At CalPortland Co.’s Mojave plant, kiln production was being limited by the raw mill, which couldn’t cope with the increasing demand of a hot market. The company made the decision to invest in a new mill, and settled on an OK raw mill 48-4 from FLSmidth – the first OK raw mill to go into operation in North America.
CalPortland Co. (CPC) is a subsidiary of Japan’s Taiehiyo Cement and renowned for its commitment to energy efficiency. The Mojave K6 line was built in the early 1980s and has been upgraded a number of times since then, but it was still operating the original raw mill – a non-FLSmidth brand VRM rated for about 250 stph.
With cement demand running high in California, the plant was pushing the mill beyond its limits to meet the production capacity of the kiln, but still not achieving the desired throughput – and experiencing reliability issues as a result. CPC was ready to make a change.
Choosing the Right Supplier
When it came to choosing which raw mill would be the right fit for the plant, CPC went out to competitive bid for an EPC contract to supply and install a new grinding circuit.
“We gave a basic design,” explained Alan Simmons, director electrical and control engineering, CPC. “It included some slightly novel concepts, based on our preferences and experiences. We found that some suppliers were more willing to accommodate our requests than others and FLSmidth was one of those that was willing to work with us on the engineering. We narrowed it down to several suppliers, but in the end FLSmidth came out on top. It was a question of the technical ability, the financial offering, and the fact that we were already operating an OK mill, which was a real advantage. For one thing, it gave us the economic benefits of common spare parts, but it also meant we were familiar with the workings of the mill and its control system.”
“Commonality of spare parts is a major benefit for cement producers because it cuts their investment in half,” said Srinivasan Seshadri, project manager, FLSmidth. “In this case, we actually designed the new mill with an over-sized gearbox, just to ensure that commonality and give CPC those benefits.”
Commonality of Experience
The existing OK mill was put in about 20 years ago and upgraded in 2018 with a new separator and ECS/ProcessExpert.
“The fact we were familiar with OK mill operations was a huge factor,” said Simmons. “This knowledge doesn’t have a dollar value, but it is incredibly valuable – particularly as the two mills are on the same site. The OK mill has been updated in the last two decades and the raw mill operates a little differently to the cement mill, but having the existing expertise made the whole thing much easier. Our maintenance department is also very confident about what to look out for, what to expect, and how to manage it.
“The same goes for the control system,” Simmons added. “These systems can take a while to learn, so staying with the same technical solution was another advantage for the plant. We’ve seen a lot of benefits from implementing ECS/ProcessExpert. It’s an important part of how we maintain and increase our process efficiency.”
A More Sustainable Grinding Circuit
Increasing energy efficiency is one of CPC’s core goals, as they seek to reduce their environmental footprint. The OK mill uses 5% to 10% less power than other vertical roller mills, giving the plant an instant saving in energy consumption. Furthermore, the mill’s high run factor – typically 90% to 95% availability – means there are less starts and stops, therefore reducing the overall power demand. Greater stability in the mill benefits the rest of CPC’s process, enabling them to run the whole line at greater efficiency levels than previously. In addition to the reduction in energy use, the other major environmental benefit of the new raw mill is its ability to remove sulfur dioxide (SO2).
Project Planning vs. Covid-19
The contract for the new grinding circuit was signed in May 2020. “The world was in a state of uncertainty,” said Seshadri. “But we were still thinking in terms of months of disruption, not years. We certainly didn’t expect Covid-19 to still be a problem when it came time to start work onsite.”
Nevertheless, FLSmidth and CPC took the decision to get ahead on ordering project supplies – and it was a good thing they did. By the time it came to shipping parts, the supply chain crisis had truly kicked in.
“There were logistical challenges from day one,” explained Seshadri. “Contract negotiations were done on Teams. We had to share huge files so that we could look over the 3D models together. It was a whole new way to collaborate, and it took a while for everyone to adjust, but we made it work. When it came to practical logistics – getting parts in from China, for example – we were faced with unprecedented demand, an almost total lack of shipping containers, port congestion, trucker shortages…The logistics side of things was like a project all on its own.”
“On site, things were different too,” added Simmons. “The contractor had people working in bubbles. We worked to limit contact between the construction team and the CPC operations team. And then we also had to manage people’s time so that everyone was getting enough rest, and so that we aligned people’s rest days so that the right people were on site at the right time. It was tough, but it was worth it.”
Everyone also had to adjust to the “new normal” of extended lead times. Supplies that could previously be obtained within 24 hours were suddenly taking days or weeks to arrive.
“It was a mindset shift,” says Simmons. “We did have a few long journeys to pick up supplies that the sub-contractor hadn’t ordered in time, but for the most part we made it work.”
Fitting Right In
Fitting an oversized gearbox underneath the new OK mill was a challenge. The mill rests on concrete piers, which had to be redesigned to accommodate the size of the gear box – with a notch, instead of the usual straight sides. Knowing that the gearbox would need to slide out for maintenance, FLSmidth decided that the gearbox should be slid into position to ensure it could be done.
“We’re talking about more than 100 metric tonnes of gearbox and a very tight fit, with just half an inch either side,” said Seshadri. “It would have been easier to drop the reducer in with a crane, but we needed to know it could be done. We didn’t want to hear in a few years’ time that the gearbox was stuck in place.”
Successful Commissioning
Commissioning during Covid-19 could have been a catastrophe, but both FLSmidth and CPC teams are proud to say that the commissioning process ran extremely smoothly.
“For CPC, commissioning is a learning opportunity,” said Simmons. “We set up a commissioning team to participate in the process, add value and learn from FLSmidth to ensure the mill not only got off to a great start, but would continue that way. It was a highly structured team, made up of a commissioning manager, discipline leads and people under them. FLSmidth had the same structure and we collaborated very closely throughout.”
“We allocated more manpower for commissioning this mill because we were falling behind on electrical wiring and we saw efficient commissioning as a way to make up for lost time,” said Seshadri. “We literally had our commissioning people and electricians following behind the contractor, pushing them forward and checking everything as soon as we could. This gave us the edge when it came to commissioning.”
In fact, both teams began their commissioning checks before the outage. CPC’s commissioning team was assigned to go out and touch every single piece of equipment, ensuring not only that they knew where to find everything, but also that they would spot anything that might cause a delay.
“Because we had a large team on both sides, a number of the little issues that you often come up with – such as sensors not working – were addressed immediately,” said Simmons. “By the time we got to wet commissioning, we knew everything was working, so the mill came up very smoothly.”
Within 7 or 8 days, the mill was running close to its guaranteed capacity of 400 stph. Having expected to wait several weeks before being able to increase kiln capacity, CPC soon found themselves with a full raw meal silo and were able to raise the kiln feed rate to optimize plant throughput.
“This was one of the least painful start-ups I’ve been involved with,” said Simmons. “It went exactly as I’d hoped it would, which is a testament to how well our commissioning teams performed.”
Ready to Face the Future
CPC is very happy with the performance of the new mill, which started up in May 2022.
“The mill is doing what it was promised to do, and we anticipate it will continue to serve us well into the future. We’ll be leaning on FLSmidth to help us get the most from the mill, I’m sure. They already give us a lot of support, and we value that partnership,” said Simmons.
“CPC is at the cutting edge of cement production,” said Seshadri. “They’re really pushing the boundaries of what is possible in terms of energy efficiency. We’re happy to support them in their quest for optimization, which so closely aligns with FLSmidth’s Mission Zero targets.”
Information for this article courtesy of FLSmidth. For more information, go to www.flsmidth.com.