This Routine Maintenance Can Be Done Quickly And Efficiently Without Creating Unsafe Conditions Or Contributing To Unplanned Downtime.
By Dennis Blauser
Concrete silos are used to store a variety of materials in aggregate, industrial, energy and agricultural industries. Concrete silo design offers numerous advantages over steel. Concrete silos provide better structural stability than steel or aluminum and better resistance to internal pressure that causes buckling, splitting, and other failures of steel silos, like abrasive inner wear from stored materials and corrosion.
Using concrete instead of steel to construct storage silos eliminates these risks when combined with proper cleaning and maintenance. When it comes to silo maintenance, concrete silos typically require less maintenance than steel versions.
When it comes to reducing overhead costs, how you handle your silos can make or break your bottom line. Following through with routine silo cleanings will increase the useful lifespan of a concrete storage silo. When completed by a professional silo cleaning company, this routine maintenance is done quickly and efficiently without creating unsafe conditions or contributing to unplanned downtime – it can also help you reap long-term cost savings.
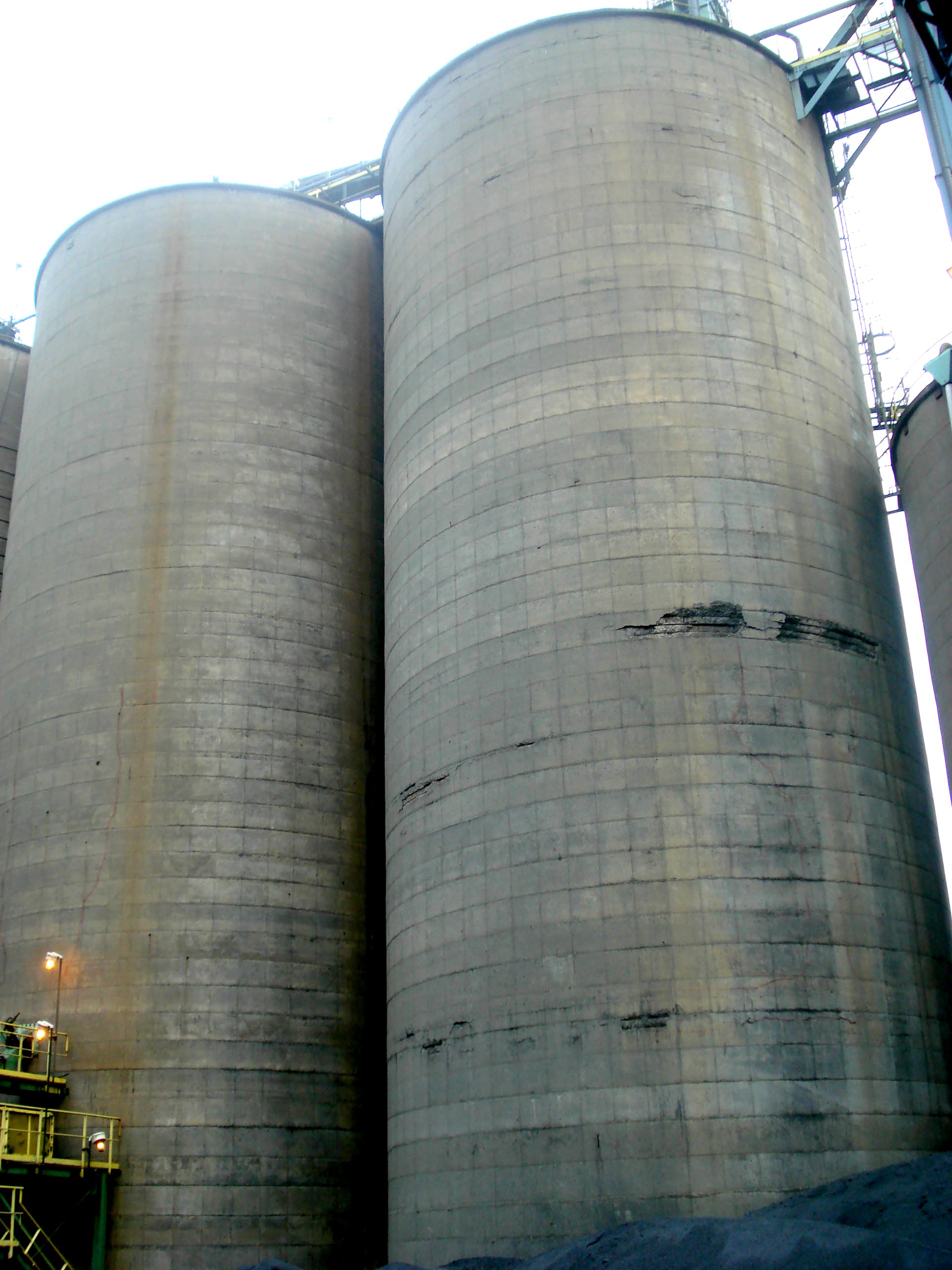
The Secret to Saving on Silo Maintenance
A silo in good working condition that is successfully meeting a plant or facility’s production goals is easy to forget about. However, if a silo becomes clogged or blocked, production slows down immediately and an array of problems and issues become clear.
Yet despite the problems that can arise from a poorly maintained silo, plants and facilities may postpone cleaning and often consider this required maintenance unnecessary. They may also find silo cleaning expensive and not worth the potential loss of production downtime.
However, the key to cost savings is to ensure silo maintenance is performed early on rather than waiting until emergency repairs are necessary. Maintenance and repairs that are part of preventive measures keep your silo safe. Preventive maintenance is a critical factor in total lifecycle costs for all storage silos.
A regular silo inspection program with proper preventive maintenance is the only way to correct hidden or visible silo wear and damage. Without regular necessary maintenance, small problems only grow into ones that can compromise structural integrity, lead to unsafe working conditions, and a reduced silo storage capacity.
When Your Silo Slows
No matter the design or the material stored, silos are susceptible to material flow issues caused by blockages. There are numerous blockage types possible in storage silos, including bridging, caking, doming, funneling, plugging, rat holing, and wall buildup or scaling. Silo blockage types may also be a combination of these or an unknown nature. Material flow that is free from blockages is essential to fully utilizing the silo’s capacity and its continued functionality. Blockages reduce storage capacity and promote bad flow characteristics. When material flow is off, delamination, exterior concrete cracking, and structural failure can result.
Silo wall buildup is especially common in adverse weather conditions, such as hot summers and cold winters. Moisture penetration from the silo walls or roof leaks, or from moist air injected into the silo through a fluidizing system increases the likelihood of material buildup.
Hung-up, clogged, or slow-running silos are a problem that will interfere with efficiency and profitability. The silo must be cleaned professionally if material buildup or other issues are visible.
The Dangers of Cutting Corners
Cleaning a silo should never be attempted by someone who is not a professional. While removing material buildup in-house may initially seem like a quick way to cut costs, there are numerous reasons why this can cost you more in the short and long term. Silo cleaning is extremely dangerous for unskilled workers.
It’s also dangerous for the facility as someone without the proper silo cleaning training is likely to damage the silo structure. Numerous news reports of serious injuries and fatalities were a direct result of in-house silo cleanings. In some cases, workers tried to dislodge buildup from below, only to be trapped by the resulting flow of materials. In other cases, workers were lowered directly into the silo, in violation of OSHA confined space entry guidelines.
Not only does this cause unnecessary loss of life, it also creates liability issues for facilities. A Nebraska company recently incurred more than $500,000 in OSHA penalties following the death of a grain handler who suffocated after attempting to clean a grain silo without the necessary safety precautions.
Failure to contract with a professional silo cleaning company also makes it easy for necessary maintenance to be missed. In addition to missing potential problems, improper silo cleaning can also create or exacerbate material flow issues, resulting in silo wall failure. The fact is, professional silo cleaning is a cost-saving measure.
Picking a Professional
Finding the right silo-cleaning professional partner is vital for a plant’s future production and profits. It is essential to work with an experienced company that has the plant’s best interests in mind and understands industry needs. To determine the best course of action, a silo cleaning company needs to consider all aspects of the situation, including the type of materials stored, the condition of the silo, and the difficulties the facility may be facing.
While the goal is to prevent emergency repairs in the first place through preventive maintenance, the right silo company should still be equipped to handle emergency silo cleaning or repairs.
A large enough company knows how to schedule silo cleaning efficiently no matter where you are located in the United States. Larger companies also allow you to bundle inspection and restoration or repair services into one mobilization. This lets you save money and can help ensure you stick to your production schedule.
When visiting your facility, the expert technicians should assess all aspects of the industrial silos, giving suggestions for further protection and preventative measures that can eliminate costly repairs in the future.
The focus of the silo cleaning professionals should be to find the most cost-efficient way to clean the silo(s). They should be transparent throughout and provide a turnkey service. The silo cleaning experience should be an easy one and result in a long-term partnership for the plant or facility to operate at its fullest potential.
Professional silo cleaning companies typically use a remote, dry-cleaning system to remove stubborn material buildup. One system that is available in the United States is a unique clean-out head, called The Boss, which is designed to remove large volumes of material buildup in a short amount of time, making it an efficient and cost-effective system. The Boss is 65% more powerful than other pneumatic systems.
By removing more material faster and with more efficiency than other clean-out methods, including the whip system, The Boss accelerates the cleaning process. This minimizes downtime and out-time on site, providing immediate cost savings.
A silo interior showing material buildup along the walls (left) before cleaning and the same silo interior following a professional cleaning.
When to Schedule Silo Cleaning
As soon as a plant manager notices a slowdown in production or a reduction in storage capacity, it is necessary to schedule a cleaning as these issues can indicate a partial blockage. Scheduling a professional cleaning as soon as possible allows more time to work the cleaning into the plant or facility’s operating calendar, as well as the professional cleaning contractor’s schedule.
One recommended cleaning schedule is during an “off-season,” when the industry and production naturally slow down, for example, during the winter months.
A routine cleaning schedule will also reduce the cost of mobilization charges and emergency plant outages. Plant and facility owners must pay more for emergency silo cleaning (where the attitude is often to hurry up and do the cleaning because the plant is shut down) than for routine cleaning during a scheduled outage.
The Takeaway
Prevention and proper maintenance are key elements to increase silo life and ensure personnel safety. Identifying issues that can later become safety concerns or cause structural damage will help avoid costly repairs and potential hazards.
Proactively checking loading and unloading procedures, observing and mitigating environmental damage to silo structures, and inspecting points of wear and potential roof, wall, and cone deterioration will improve safety and maximize silo life.
A clean silo is a safe silo. Silo cleaning services not only exist for the efficiency of the plant or facility but also for the safety of the compound and personnel. The buildup of any load within a silo creates the potential for a sudden collapse. This unexpected collapse could damage the silo or hurt workers.
Cleaning is essential for the facility’s safety, as well as for the performance of the silo. Silo cleaning using an untrained labor force is highly dangerous and can lead to silo damage, as well as accidental injury or death. It is essential to have qualified and trained silo cleaning professionals.
Dennis Blauser is the CEO of Marietta Group, which includes Marietta Silos Inc., Marietta Inspection Services and USA Silo Service.