The Availability Of High-Quality Alternative Fuels Is A Key Barrier To The Widespread Adoption Of Alternative Fuels In The Cement Industry. However, There Are Now A Number Of Solutions On The Market That Allow The Use Of Coarse And Low-Quality Materials, Without The Traditional Preparation Requirements.
by Jonathan Rowland
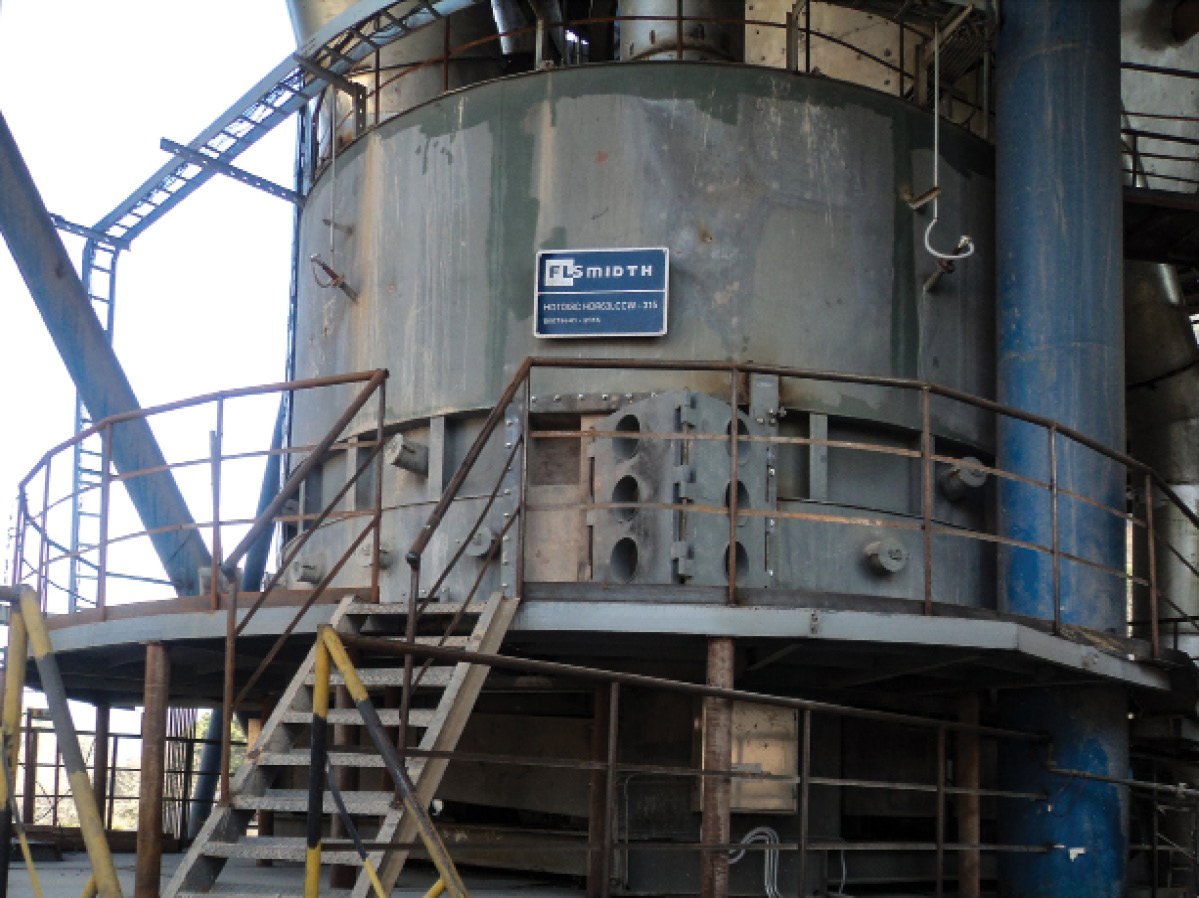
The use of alternative fuels (AF) is widely promoted within the cement industry as key to reducing the carbon intensity of cement production. But as we have discussed in recent issues of Cement Products, their use also raises challenges (e.g., check out the article on handling and storing AF in the October 2022 issue, or the article on the impact of AF on process and equipment in Mar/Apr 2023). There may also be issues around permitting and public acceptance of AF, with sensitivities around the incineration of waste products.
An additional major challenge is the availability of AF suitable for the cement process. Although cement making is among the hottest of industrial processes, you cannot in fact just toss any old trash into the calciner or kiln. At least, not without impacting the stability of the process and quality of the clinker. More often than not, potential fuels will require processing before they can be used as a viable substitute for fossil fuels. The degree of processing varies depending on where they will be used (e.g., the calciner is generally able to accept coarser fuels than the main kiln burner): but processed they will have to be.
This requires either an adequate local waste management and processing sector (or investment by cement companies in processing facilities – and sometimes even waste collection. Unfortunately, this adds a level of complexity and cost to the adoption of AF that many cement plants are either unwilling or unable to take on. As Steven Miller, global product manager, pyroprocessing technology at FLSmidth recently told Cement Products: “The barrier to increasing substitution of AF for many plants is a reliable supply of fuels.”
“When you consider the use of AF to replace traditional fossil fuels, we have to accept that these materials were never intended to be used as a fuel,” added Matthias Mersmann, chief technical officer at KHD.
“This means that their chemical, physical and particulate properties are far from ideal for a fuel. Although some attempts at standardization have occurred, they have not been generally adopted. The only thing we can say for sure is that AF are always more challenging to burn, with some individual fuel particles taking up to several minutes to combust. Most conventional alternative fuel systems can therefore only utilize AF that has been heavily processed to improve their quality and consistency.”
Fortunately, equipment manufacturers have woken up to this challenge with a number of solutions on the market that allow cement plants to utilize AF with minimum (if any) expensive shredding or drying of these materials. These concepts rely instead on an additional thermal processing step occurring before the calciner in a separate combustion device or reactor.1
The use of such a device “allows much higher flexibility in the type of AF used, as well as a quick changes between fuels, as the cement plant is not committed to one specific AF preparation step,” explained Uwe Maas, director of technical sales – fuel substitution at thyssenkrupp Industrial Solutions. Pre-combustion is also “ideal for fuel mixes that contain both high-calorific and low-calorific fractions, because it facilitates a more even flow of energy into the calciner.”
“The flexibility of these systems thus helps to overcome the barriers to increased thermal substitution rates,” concluded Miller, “making the transition to AF much easier and cost-effective, especially in regions that lack a developed waste processing industry.”
This not only supports efforts to decarbonize the cement industry, “it offers much more than that,” added Mersmann. “It means cement plants can source fuels locally, and so protect themselves against fuel price shocks caused by disruptions to global fuel supply chains. It also has the potential to lower fuel costs – and thus cement production costs.”

FLSmidth HOTDISC Reactor
First introduced in 2002, the conventional HOTDISC reactor is integrated into the pyroprocess below the calciner bottom and features a slowly-rotating disc onto which the AF are fed and combust. Hot tertiary air is directed into the HOTDISC to provide an oxidizing atmosphere in which the AF is combusted.
“As the AF travels about 270 degrees on the rotating disc, almost all of it fully combusts,” explained Miller. “Depending on the nature of the AF – size, heat content, moisture, etc. – the rotational speed can be adjusted to optimize residency time and combustion rate. Temperature is controlled by directing a portion of the preheated raw meal into the HOTDISC.”
The HOTDISC generates a “controlled mix of hot gases, combustion residue (ash), and calcined raw meal,” continued the FLSmidth expert. “The combustion gases and finer materials are carried with the hot gases into the bottom of the calciner, while a scraper at the end of the 270-degree turn directs the coarser residues into the riser duct. This material then falls into the kiln and is incorporated into the clinker.”
AF fired in the HOTDISC replaces a high percentage of the total fuel burned in the calciner; however, “some fuel firing in the calciner is still needed to control the bottom stage exit temperature and hence the raw mix calcination percentage,” concluded Miller.
The HOTDISC is available for both new kilns and retrofits onto existing kiln systems with a recent design change making retrofits easier. “In 2021, we introduced the HOTDISC-HMT, which offers the same functionality and benefits as the traditional system, but is quicker and easier to install at existing plants,” explained Miller. Instead of directly integrating the exit of the reactor into the calciner and riser duct, the new layout allows the reactor to be mounted 2 to 5 meters away and then connected via a hot material transport chute for gas flows and combustion ashes.”
A further design option is the HOTDISC-S, which is positioned under the existing calciner – instead of above the kiln inlet as is the case at plants with in-line calciners – and allows application at plants with separate line calciners. In this layout, “most of the alternate fuel is fed first into the calciner, with any unburnt fuel falling into the HOTDISC-S, where it completes burnout,” said Miller. “Any drop-out from the HOTDISC-S is recovered via an ABC cooling unit for cooling, and can then be transported back into the system or discarded.” The first HOTDISC-S reactor was sold to Ssangyong Cement in South Korea and has successfully operated since 2020.
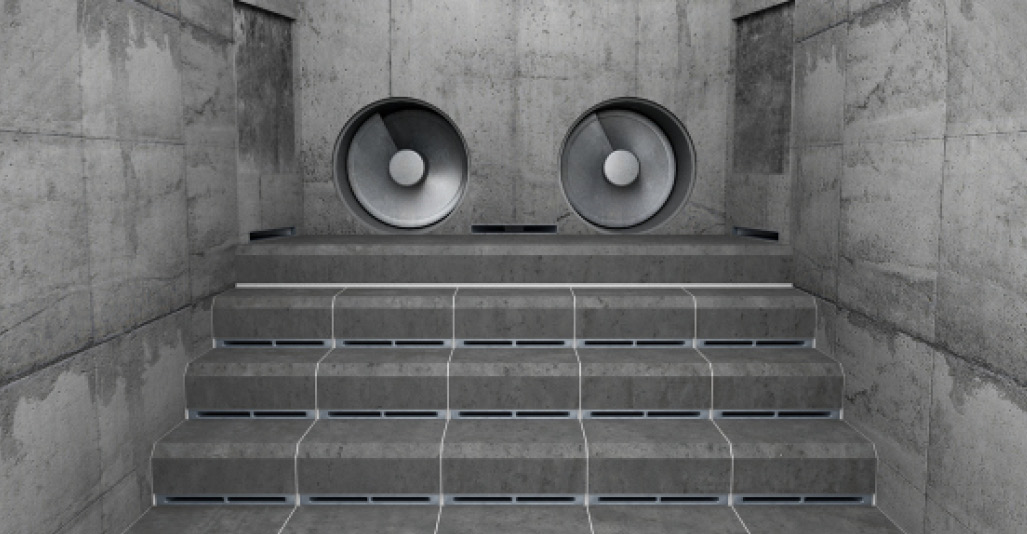
A Solution for Hazardous Waste
The LZ cement plant is a 5,000-tpd facility in ZiBo, Shandong province, China. It was having issues with pyroprocess instability, as a result of feeding hazardous waste directly into the calciner. “The plant team got in touch with us to discuss the possibility of installing a HOTDISC as a solution to this problem,” said Miller. “After much discussion, we recognized that high chlorine content in the waste would require special measures and designed a four-feed point that enables the LZ plant to burn solid waste, semi-solid waste, liquid waste, and waste packaging. In addition, we added a 10% bypass system to the design.”
Start-up and commissioning commenced in October 2018. According to Miller, “within a week the plant was able to double the previous waste feed rate. The pyroprocess is also far more stable than it was previously. Since then, we have supplied a number of HOTDISC reactors for safe disposal of hazardous waste at cement plants. And CY company, one of China’s largest hazardous waste operations, has purchased three HOTDISC since 2019 to dispose of waste.”
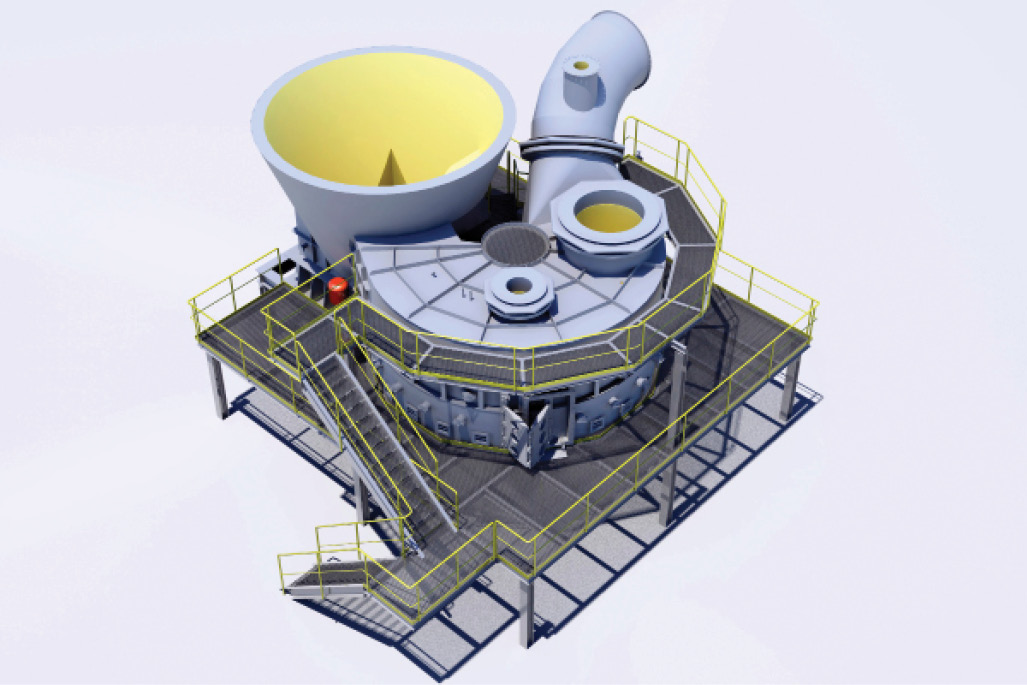
KHD Pyrorotor Rotating Combustion Chamber
Available as a modular retrofit to the calciner at both new and existing plants, KHD’s Pyrorotor is a rotary combustion reactor based on the same operating principles as rotary kiln, explained the company’s Mersmann. “We firstly leverage a plant’s existing tertiary air stream to achieve temperatures of up to 1,200°C in the combustion chamber. Rotation of the chamber then ensures thorough mixing of the AF with the hot tertiary air.”
The Pyrorotor has been “engineered with flexibility in mind,” continued Mersmann. “The installed drives offer a large reserve in terms of available torque to cater for a wide range of loads and rotation requirements, while rotational speed can be set at 0.3 to 3 rpm for residency times of up to 10 minutes. Residency time can therefore be optimized to the fuel characteristics to ensure complete burn-out.”
Ash generated in the Pyrorotor falls directly into the kiln riser, while combustion gases and entrained smaller particles exit the reactor and create a second combustion stage in the calciner. This “staged combustion” improves energy efficiency and environmental performance as “heat is transferred to the raw meal over an extended distance, without temperature peaks, and NOX formation is controlled,” explained Mersmann. “For even more advanced NOX reduction, tertiary air can be introduced downstream of the Pyrorotor to create a highly-efficient reduction zone in the lower riser duct, reducing kiln-generated NOX.”
The Pyrorotor has proved particularly popular in South Korea, where 10 installations are currently in operation or being implemented. There are also plants in Austria, China and Turkey, as well as a recently announced contract to deliver one to Cimpor Alhandra in Portugal.
At Asia Cement’s Jecheon plant in South Korea, for example, the Pyrorotor has been in operation since spring of 2022, increasing fuel substitution rates in the calciner from 23% to 86%. CO2 emissions savings are estimated to be 20 tph – or about 20% – as a result. NOX emissions have also fallen from 242 ppm to 166 ppm.
“The KHD Pyrorotor is very intuitive and flexible,” said Ju Ik Baek, research engineer at Asia Cement. “There are several options to fine tune combustion to ensure various types of fuel can be effectively burned, without additional processing. Due to its high reliability, we were easily able to achieve our fuel replacement goal. We also had no problems when connecting the Pyrorotor to our existing equipment.”
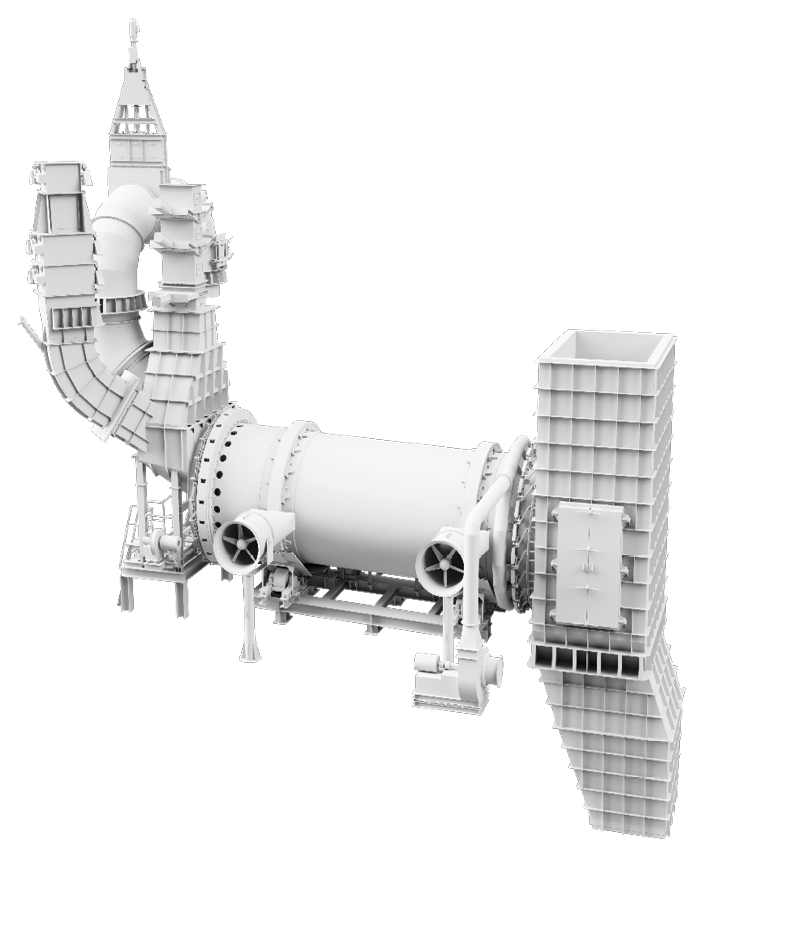
thyssenkrupp prepol SC Grate Reactor
The prepol SC is a grate-type combustion reactor that is “connected to the lower part of the calciner and allows a residency time of up to 1,000 seconds, before the particles finally enter the calciner,” explained thyssenkrupp’s Uwe Maas.
Continuous substitution rate of up to ~85% in the calciner are possible, continued Maas. “The machine itself is able to handle higher substitution rates but, although the prepol SC allows a very even combustion, it will never be as smooth as the combustion of traditional fuels. Therefore, highly reactive fuels – which can also be alternative fuels – have to be available to equilibrate fluctuations in thermal heat supply.”
A second consideration when utilizing AF a high capacities and of varying types and characteristics is the volatile and hazardous components in the fuel. “These components should not disturb kiln operations and need to be properly integrated into the clinker,” said Maas. “It is therefore quite common to install a chlorine bypass with a high-capacity prepol SC.”
Fuel is continuously fed into the combustion chamber via two water-cooled screw conveyors. Temperature for ignition and oxygen for combustion is provided by hot tertiary air. Movement of fuel over the grate is facilitated by an air blast conveying system installed inside the grate. This “regularly lifts particles into the hot tertiary air steam,” continued Maas, “whereby particles that are fine enough to be entrained in the tertiary air flow with the combustion gases into the calciner, while coarse particles fall back onto the grate. This allows efficient use of the available combustion area, since only particles that need further treatment remain on the grate.”
Temperature control is achieved by introducing meal from the upper cyclone stage into the prepol SC with the tertiary air. The meal serves as a “heat sink,” explained the thyssenkrupp expert. “If the temperature inside the combustion chamber increases, the amount of meal is also increased, whereas if the combustion chamber temperature is decreasing, the meal amount is decreased.”
The prepol SC is available for both greenfield and retrofit installations. “The only requirements are that tertiary air is available, and that meal from the upper stages can be directed to the combustion chamber,” said Maas. “Since 16 of the 19 units sold so far have been retrofits, these requirements can be met in almost all cases.”
Note
Available solutions discussed in this article are the HOTDISC from FLSmidth, the Pyrorotor from KHD, and the prepol SC from thyssenkrupp, but other systems are also available, e.g., FCB Preca-Max from Fives, who were unable to provide comment for this article. It should also be noted that no comparison of systems is intended here. Readers are encouraged to contact the companies involved for further information.