To Accommodate Expansion Movement Within Anchoring Systems, Vital Allowances Must Be Incorporated.
Edited by Mark S. Kuhar
Research shows that more than 40% of monolithic refractory failures are the result of improper anchor design and installation. Failures commonly attributed to the refractory component are instead often caused by shortcomings in the actual anchoring system.
Like any material, refractories will expand and contract due to changes in temperatures. Expansion in refractories can be broken down into two different types: Permanent Linear Change (PLC) and reversible expansion.
PLC is a type of expansion stress that occurs during the initial heat-up when moisture is released from the refractory. Reversible expansion happens when the refractories go through thermal cycling, or in more detail, from an extremely high temperature to room temperature, and then back again to high temperatures.
Both types of expansion, PLC and reversible, are accounted for in mathematical terms as the rate of expansion, per inch, for every degree that the temperature increases. Engineers and refractory installers can find expansion rate numbers listed on technical data sheets.
Ceramic anchors, as an integrated part of the overall refractory lining, will move with the monolithic refractories as it experiences these thermal cycling and initial heat-up PLC stresses.
So, a critical consideration when designing an anchoring layout for a suspended refractory application is factoring in the movement of the anchor. If not accommodated, this movement can cause the ceramic anchor to fail, leading to a section of refractory dislodging. In the extreme, refractory sections could fall out and leave a major gap or hole in the lining.
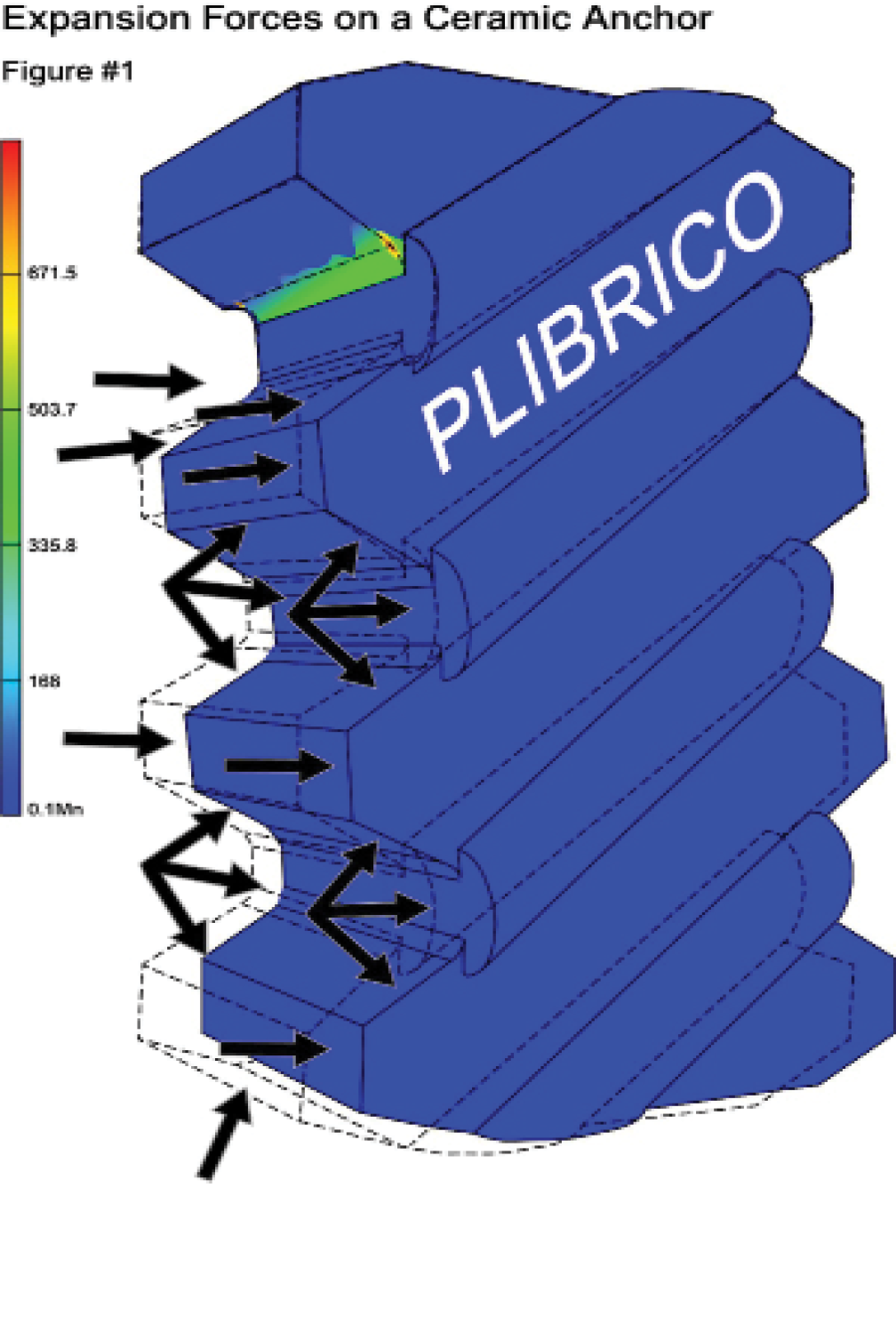
Three-Dimensional World
Thermal expansion happens in all three dimensions: length, width and height. For anchor designing purposes, the “height” aspect refers to the thickness of the installation material and is a minor consideration when designing for expansion allowance.
Instead, the larger focus should be on the other two anchoring dimensions since the installation is far more likely to move in the length and width directions. Therefore, it is critical that allowances be made in the anchoring system to accommodate this movement.
Illustrated in Figure 1 (below) are the forces that act on a ceramic anchor in one of the directions of expansion. Arrows signify the pressure distributed across the various faces of a ceramic anchor, while the top of the anchor is constrained in place.
Note that there is a concentration of stresses at approximately the point where an anchor clip would normally contact the anchor. If this clip or the beam that supports the clip does not allow the anchor to move to relieve this stress, the anchor will very likely fail.
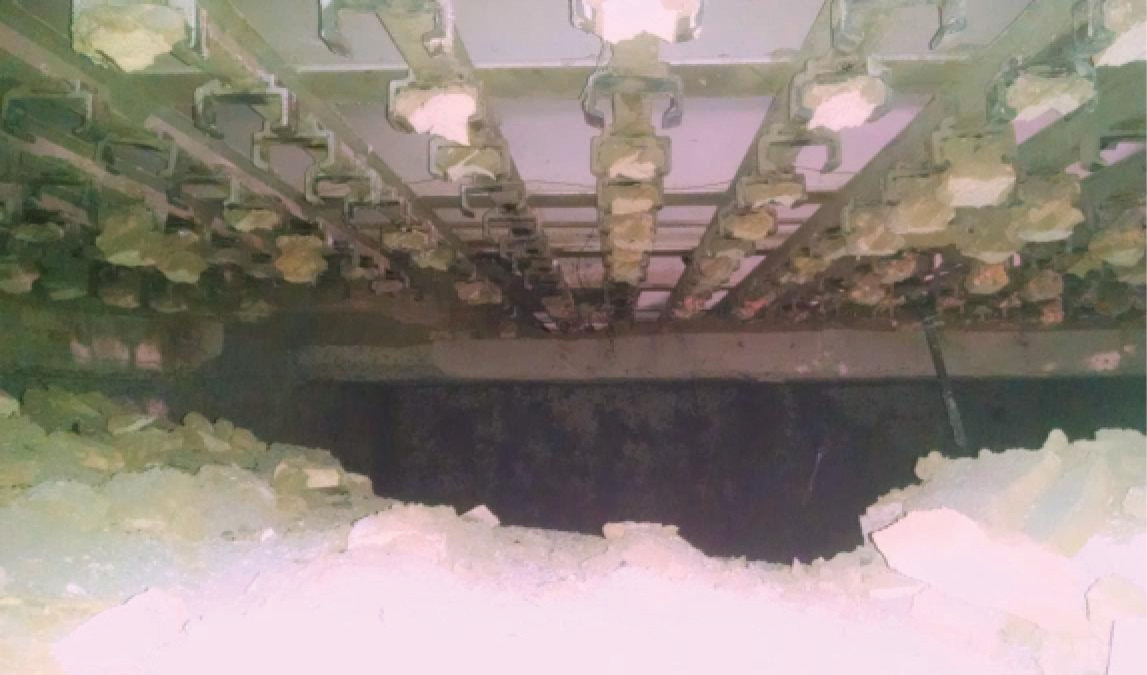
fall out and leave major gaps or holes in the lining.
Preventing Anchoring System Failures
To create a strong anchoring system that accommodates movement, here are three simple steps that should be followed in the design and planning of a ceramic anchoring system:
1. Determine how much expansion the installation requires, including reversible expansion due to cycling, and the PLC that happens only during the initial bake-out.
2. Choose an appropriate expansion scheme.
3. Select an anchoring system that will accommodate these expansion requirements, including number of anchors, anchor spacing, anchor shape, size and material.
A strong anchoring system is key to maintaining monolithic refractory lining integrity and preventing cracking, dislodging, or a total structural collapse. And essential to a strong anchoring system is movement accommodation.
By carefully determining expansion, and then designing the suspension system to accommodate for movement, you’ll greatly improve refractory life and prevent any possible catastrophic refractory lining failures due to a rigid and poorly designed anchoring system.
For additional information on optimal ceramic refractory anchoring design, including a short video, check out the Plibrico website: www.plibrico.com and YouTube Channel: https://plibri.co/Plibrico_YouTube . You can also contact Plibrico at 312-337-9000, or [email protected].
Plibrico Company
Plibrico Company LLC is a single-source supplier of aluminosilicate and high alumina monolithic refractories used in the processing of aluminum, steel, sugar, cement, waste, power generation and other demanding thermal environments.
For more than a century, organizations have trusted the company to develop innovative and reliable refractory solutions that consistently increase efficiency, improve production uptime and safely boost the performance of its customers’ thermal processing operations and equipment.
Committed to growth, and focused on providing value to customers, Plibrico has brought together one of the broadest product and technical service portfolios in the refractories industry. Its wide portfolio allows us to fully service our customers from concept to completion.
The Plibrico Company supplies its highly durable monolithic refractory materials to thermal processors in the United States under the Plibrico and Redline brands, and worldwide under the Plico brand.
Headquartered in Northbrook, Ill., Plibrico serves its customers through a centrally located manufacturing plant, and a network of refractory construction offices throughout the United States and Canada. Plibrico has built a business over more than a century, based on trust, knowledge and experience, qualities that create close lasting relationships to deliver superior heat control solutions.