As The Use Of Alternative Fuels Grows, So Too The Challenges They Pose To Equipment And Process.
by Jonathan Rowland
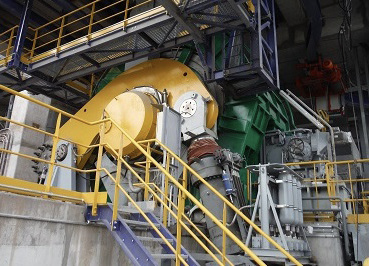
Fossil fuels are often maligned for their carbon emissions. Yet they are not the world’s most successful energy source without reason. Fossil fuels pack a punch when it comes to calorific value and offer consistent chemical composition, moisture content and particle size. Their impact on the pyroprocess is thus predictable and easy to manage. They are also supplied along well-established supply chains (although not immune to geopolitical shock).
For all of these benefits, it is the emission of carbon that now supersedes all others – and leaves the cement industry searching for alternatives as part of its commitment to the global net-zero transition. But the adoption of such alternative fuels (AF) is not a simple one: derived from waste – either municipal or of other industrial processes – AF often lack the consistency of fossil fuels. This in turn poses challenges for the equipment and process.
The Impact of Variability
“The variability can have a significant impact on the clinkerization process,” explained Jean-Michel Charmet, pyroprocess product manager at Fives FCB. “AF can have different chemical and physical properties that traditional fossil fuels, which can affect the burning process and the resulting clinker quality.”
For example, high-moisture fuels or fuels with lower calorific value can impact the stability of the calciner. “This will lead to variability in the calcination of the meal entering the kiln, which in turn may result in the kiln cycling between overburnt and under-burnt clinker,” explained Mark Mutter, managing director of JAMCEM Consulting.
“Chemical variability in the fuel – for example variable levels of ash – will also have an effect on the stability of the kiln and on clinker quality,” continued Mutter. “To achieve higher substitution rates, as seen in some kilns now – and as required under the various roadmaps to net-zero cement – it is necessary to fire the AF on the main burner. This is not so much a problem for liquids or finely ground solids (such as carbon black) but for materials such as refuse-derived fuels (RDF)/solid recovered fuels (SRF) it is critical to have a low moisture content and finely shredded material in order to ensure rapid combustion in the burning zone.”
“To control and manage the variability of AF, it is important to carefully monitor the fuel properties and adjust the burning process accordingly,” concluded Chamet. “This can include adjusting the temperature and airflow, or the chemistry of the raw meal. Online monitoring of the raw materials chemistry is also a must to make the necessary adjustments. Of course, regular testing and monitoring of the clinker quality is needed to ensure that it meets the desired specifications.”
Due to the wide range and heterogeneity of AF, standard laboratory analysis techniques, such as thermogravimetric and chemical analyses, are not always relevant. “Fives FCB has developed a set of tests in order to evaluate the main parameters governing AF combustion, such as specific surface area, energy and temperature of volatilization, as well as char combustion cinetic according to the atmosphere and temperature conditions,” explained Chamet.
“A broad range of fuels have been tested with our in-house experimental tools in order to build a database, which is then used for new projects and modeling purposes. Furthermore, such tests can be conducted in addition to the standard chemical analyses, to characterize fuel samples during the early stage of the design process of a new industrial plant.”
This ability to characterize fuel behavior early with a design process is important, as fuel variability also impacts the choice and operation of the burners. “AF are more inconsistent than fossil fuels when it comes to moisture content, calorific value, particle size, and chemical composition, and these factors affect how the fuel burns and the resulting heat distribution within the kiln,” explained Chamet.
“To accommodate the use of AF, burners may therefore need to be specially designed or modified to handle the unique properties of the fuel,” continued Chamet. “Fuel injection must insure that the larger AF particles are correctly lifted in order to have sufficient travel time within the flame. Air-fuel mixing must also be insured to avoid stratification and double flame phenomena. Additionally, the use of AF may require changes to the burner settings and combustion process: for example, adjusting the air-to-fuel ratio, the combustion temperature and the airflow may be necessary to ensure complete combustion.”
Alkali Attack
The use of AF can also alter the chemistry of the combustion environment. “If the fuels do not burn properly and release carbon monoxide, there is the risk of creating sulfate cycles in the system, which can lead to build-ups in the kiln riser and lower stage cyclones,” said Mutter. However, the bigger risk is often the introduction of chlorides into the system, which are “extremely volatile and cause much greater build-up issues that sulfates.”
“Ideally the sulfur/alkali ratio of all input materials should be kept close to one,” added Chamet. ”As AF usually contain less sulfur than traditional fuels, an excess of alkalis over sulfur could increase the likelihood of alkali-related buildups in the smokebox or kiln inlet, especially in the presence of chlorides. The clinker produced could have higher water demand and faster setting causing workability issues for the cement.”
“The level of chloride into the system is often the limiting factor on the substitution rate into the system,” explained Mutter. “In such instances, the solution is a volatiles bypass system of some sort – but that then raises an additional issue of what to do with the dust that comes out of the bypass.”
The higher concentration of alkali materials can also increase rates of chemical wear to equipment. “This results in increased maintenance costs and reduce the operating life of equipment,” said Chamet. “For example, alumino-silicate refractories are particularly sensitive to alkali attack and should be replaced by alkali-resistant materials containing silicon carbide and/or zirconium in most critical areas.”
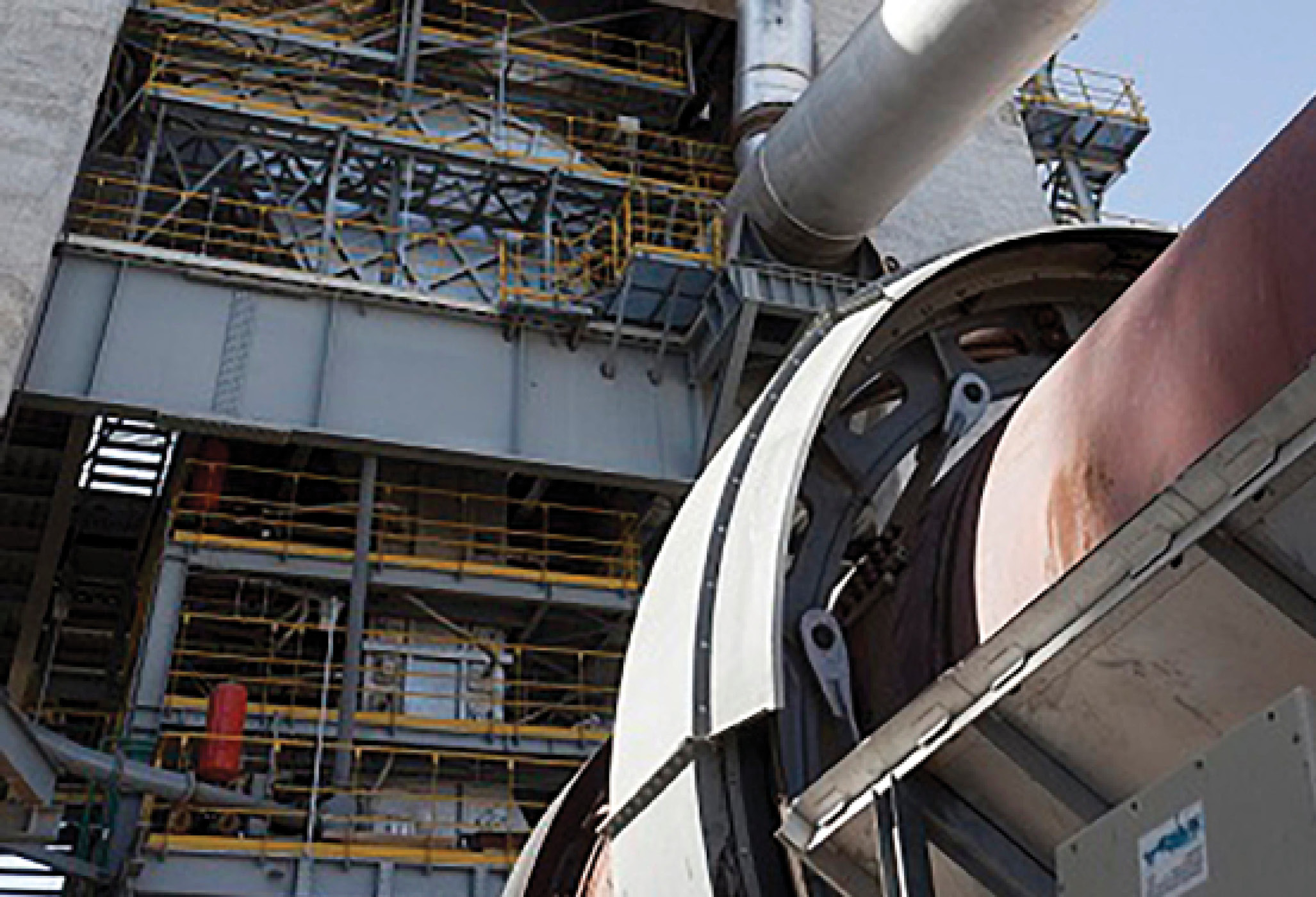
CFD Modeling
The challenging impact of AF on the cement-making process make it ripe candidate for modeling; however, this is easier said than done. “The modeling of the calcination process within the clinker pyroprocess is especially complex, as the combustion of the fuels, the chemical reactions of the raw meal, and fluid dynamics are intimately interacting with each other,” explained Chamet. “This is the main reasons why results of CFD predictions for cement plant are often perceived as inaccurate.”
In response to this, Fives FCB has built a new modeling concept, based on experiences and measurements from laboratory and industrial plants. The model is based on Ansys Fluent, a powerful CFD software, which has been enhanced by the use of User Defined Functions (UDF) in order to define more accurately the interactions within the calcination process. Those functions can be dynamically loaded with the Ansys Fluent solver to improve its standard functionality, e.g., to customize the boundary conditions, improve an existing model or integrate a new model, etc.
“The UDFs are defined based on our experimental results of laboratory calcination tests realized on various types of limestone and AF,” explained Chamet. “They allow to describe accurately the heat and mass transfer related to the particles and the calcination reaction. This model has now been used to simulate various types of calciners (hot-spot or inline) with any type of fuels (coal/petcoke, natural gas and AF). Onsite measurements in several industrial plants allowed to validate its accuracy.”
Any Other Business?
In addition to these challenges, there are “several other issues related to the process, plant, and equipment that cement plants should be aware of when considering the use of AF at high substitution rates,” said the Fives FCB expert:
- Fuel storage and handling: The variable characteristics of AF can also affect the storage and handling requirements and may require the use of specialized equipment or modification of existing equipment. For example, due to the low density and mass calorific value, very large storage areas may be required; odor and VOCs may also have to be addressed from storage and handling areas. (ed. – for a more detailed discussion on the handling and storage of AF, check out the article “Sticky, Inconsistent, Potentially Hazardous: Handling and Storing Alternative Fuels” in the October 2022 issue of Cement Products.)
- Maintenance: The use of AF can result in increased wear and tear on the equipment and machinery in the plant. This can lead to increased maintenance costs and the need for more frequent equipment repairs.
- Process optimization: The use of AF can require adjustments to the burning process, the air-to-fuel ratio, the combustion temperature, and the airflow. This can be challenging to optimize and requires a good understanding of the fuel properties, as well as the ability to monitor and control the burning process.
- Safety: AF can present additional safety hazards. For example, some AF are more flammable or explosive. It is important to have proper safety measures in place and to provide training to the employees on how to handle and transport the alternative fuels safely.
Advanced crushing and grinding mill equipment from Fives FCB.