Heidelberg Materials’ Edmonton, Canada, Plant Works To Implement CCUS Technology.
By Kristin Dispenza
The concept of carbon capture has been around for decades. While it has been implemented more widely in other sectors, such as coal-fired power generation, carbon capture, utilization and storage (CCUS) has not historically been applied to a cement kiln.
There are significant differences and complexities between the applications, including flue gas makeup, process characteristics and other factors. That said, it remains critical for the cement industry, as a significant source of CO2 emissions, to decarbonize.
A CCUS project currently underway at the Heidelberg Materials North America plant in Edmonton, Canada, exemplifies the complexity of implementing the technology in this sector – the carbon capture facility is so sizeable it had to be located on a neighboring site. Among the structures it will accommodate are an absorber tower that is as tall as a 20-story building and a mile-long, 12-ft.-diameter flue gas pipe that will connect the main plant to the CCUS operation.
Important Step
Reducing actual net CO2 emissions for cement production is an important step toward achieving net zero carbon concrete. Currently, carbon neutral concrete calculations rely on the purchase of offset credits, while capturing and storing CO2 allows for the direct greenhouse gas (GHG) benefit to be realized on the product and hence avoid the use of offsets.
Therefore, CCUS for cement plants is one of the technologies Heidelberg Materials is studying not only across its North American sites, but around the world. Once fully realized, the CCUS project planned for the Edmonton, Canada, facility could be North America’s first full-scale implementation at a cement plant.
“When operational, cement produced at the Edmonton facility will be net-zero carbon,” said J. Ignacio Cariaga, commercial sustainability director, Northwest Region, Heidelberg Materials North America. “This is important to concrete producers, because those within the shipping area of the plant could potentially use the cement to achieve net zero concrete. As more and more people pursue net-zero building, the availability of this kind of cement is critical.”
Edmonton’s CCUS front-end engineering design (FEED) study was approved in summer 2022 and by the end of 2026, based on finalization of sufficient government funding, carbon capture is expected to begin. The operation will significantly contribute to Heidelberg Materials’ goal of achieving net zero by 2050.
The project remains on target to be the first new CCUS project in Alberta this decade, although it is the first of many that are being planned.
”The first generation of post-combustion CCUS technology was deployed 10 years ago on coal-fired power plants, including both Boundary Dam in Saskatchewan and Petra-Nova in Texas. The Edmonton project has leveraged the lessons learned from these first projects, which have similar flue gas to cement kilns, in order to develop what we consider to be the second-generation application of this technology, which promises more favorable performance in all areas,” said Corwyn Bruce, project director, Edmonton CCUS, Heidelberg Materials.
The cost of the project is estimated at nearly $1.4 billion Canadian dollars.
Process of Carbon Capture
The carbon capture process at Edmonton involves installing a motorized damper at the base of the exhaust stack that can route the kiln’s flue gas to the new facility. The diverted flue gas is first cooled to 30-40 degrees Celsius as required for the proper functioning of amine (a chemical compound derivative of ammonia) which, in solution with water, is used to bind with and absorb the CO2 from the gas.
Liquid amine accumulates in the bottom of the absorber and is subsequently sent to a desorber, where steam heat is used to separate out the CO2. CO2 that is captured at the plant will be compressed for transportation and permanent, safe storage in deep wells outside the city (Alberta being a geologically ideal location for this type of well). Storage will follow strict Measuring Monitoring Verification (MMV) protocols to ensure it is permanently stored. Treated flue gas with less than 1% CO2 remaining will then be released into the atmosphere.
Seventy-five thousand liters of water per hour are extracted as part of the CCUS process. Whereas in traditional cement production, such water would have been exhausted through the stack as vapor, the Edmonton facility will use 90%of the wastewater to provide cooling for the capture process. The remaining 10% will be used in residual applications such as in grinding mills and in the gas conditioning tower. Since fresh municipal water is currently used for this type of residual application, the use of wastewater represents both an economic and environmentally beneficial option.
Additional Carbon Reduction
The use of alternative fuels in cement production can further reduce the carbon footprint. The Edmonton facility is expected to operate using 50% alternative fuels by 2024. Alternative fuels contain biogenic carbon, which is derived from living (plant or animal) organisms that have absorbed CO2 from the atmosphere relatively recently. When biogenic carbon is combusted, the CO2 that results is considered carbon neutral because it is being returned to the atmosphere after having been absorbed.
While fossil fuels are also derived from once-living organisms, the carbon in those fuels has been long since out of circulation and CO2 that results from combustion of fossil fuels therefore increases the concentration of CO2 in the atmosphere. Importantly, storing CO2 from biogenic carbon underground using CCUS will permanently remove CO2 from the atmosphere.
Specific alternative fuels that will be used at the Edmonton facility include solid recovered fuel (SRF) comprised of paper, cardboard, wood, textiles and plastic. This blend is estimated to be 50% from municipally-sourced refuse materials from households and 50% from construction and demolition (such as pallets and other scrap wood).
Cement production lends itself well to the use of alternative fuels compared to other industries. One reason is the fate of ash that is produced when solid fuels are combusted. Many industries, such as power generation, must manage ash residue and the impurities it contains (such as dust, metal particulates, and sulfur compounds) as waste or byproduct.
In a cement plant, however, the recirculating lime-rich minerals in the preheater tower effectively scrub out the particulates, forcing them into the process to be fully incorporated as nonhazardous ingredients into the finished product.
“This makes cement production a very good match for the use of alternative fuels,” explained Jasper van de Wetering, AFR/CO2 manager, Northwest Region, Heidelberg Materials. “Since plastics placed in landfills can produce microplastics, which pose a hazard to ocean and aquatic life, and biogenic materials such as wood emit methane as they decompose, the benefit for use in the cement making process is significant.”
According to the Environmental Protection Agency (EPA), methane is more than 25 times as potent as carbon dioxide at trapping heat in the atmosphere.
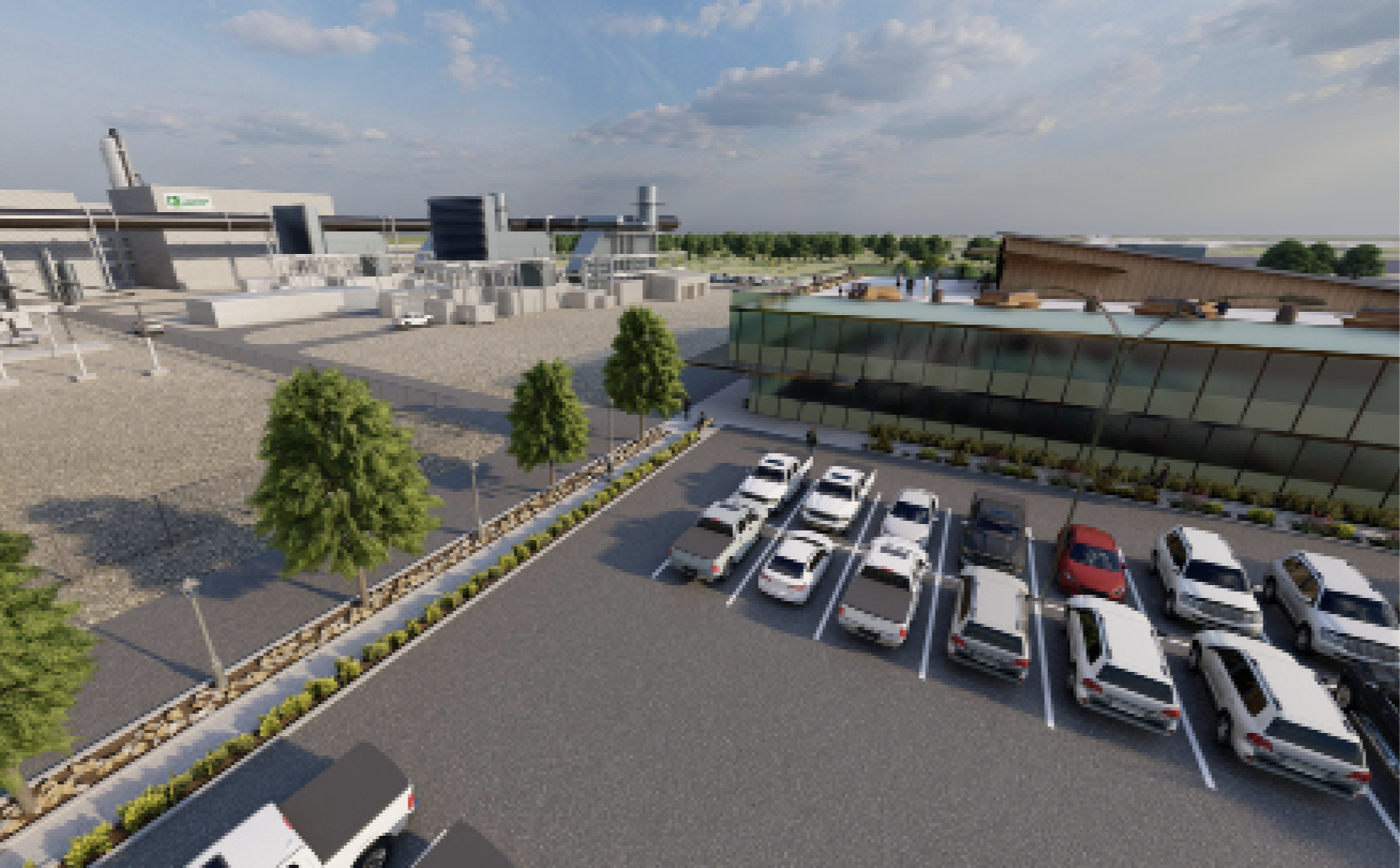
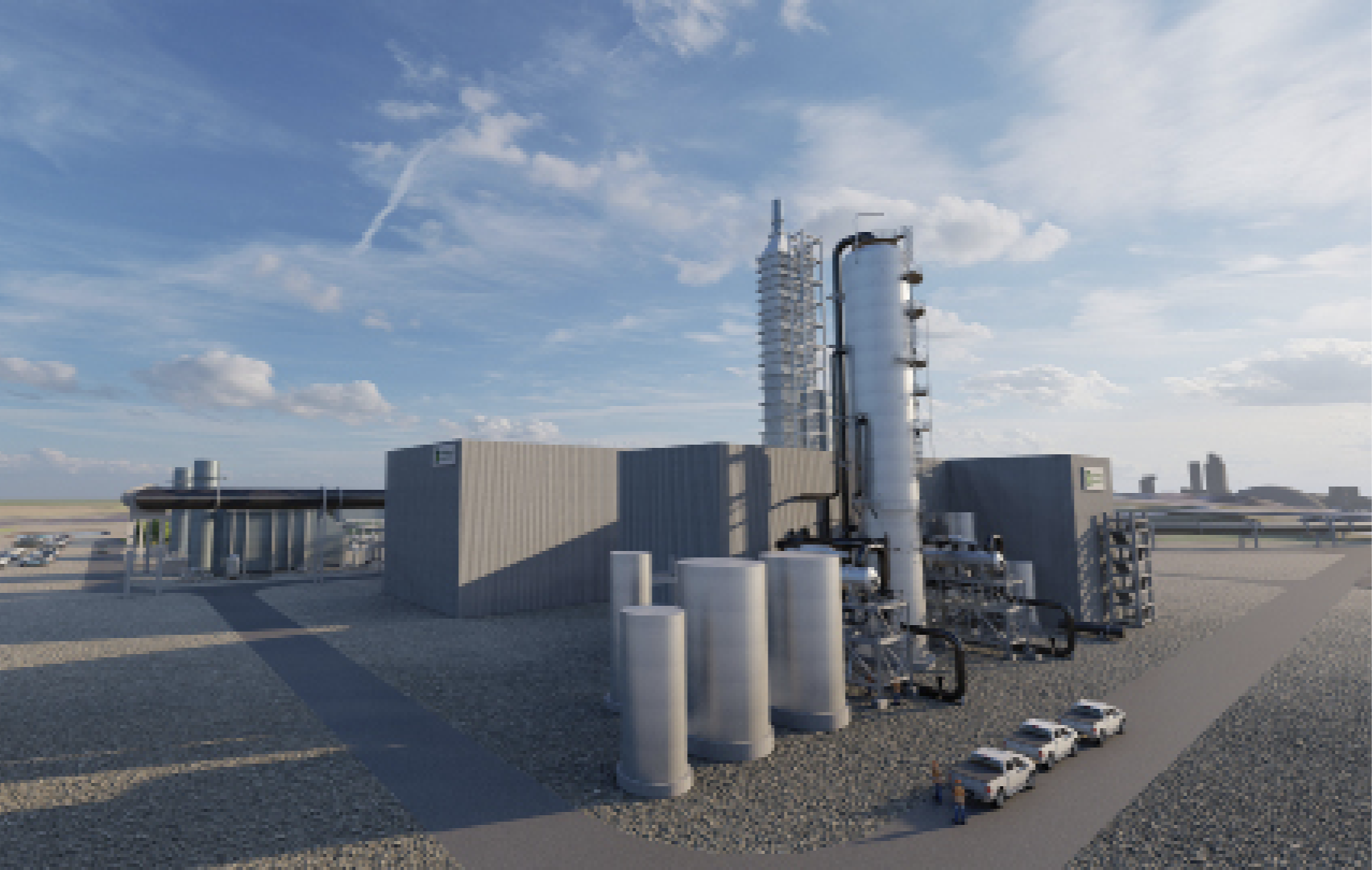
Combined Heat and Power
Another innovative feature of the Edmonton plant CCUS project is the employment of combined heat and power (CHP). In order to optimize the design of the CCUS system and meet the dual need of steam and electricity, it was determined that a CHP is not only the most efficient solution but is integral to the overall success of the project.
Importantly, the EPA points out that conventional, separate facilities for power and heat generation waste nearly two-thirds of the energy generated. Combined heat and power technology eliminates that inefficiency, taking advantage of on-site power production to route excess heat to applications within the facility such as producing steam or heating water, reducing facility demand on the grid.
At Edmonton, in addition to generating the electricity needed for the carbon capture process and for other power requirements across the facility, the CHP plant will generate the steam needed to drive the facility’s CO2 compressor and regenerate the amine in the absorber. Any surplus electricity will be exported to the Alberta grid.
Heidelberg Materials’ CHP plant in Edmonton is expected to yield significant advances in implementing the technology for the cement sector, since CHP is not yet common in the industry – despite the fact that recovering carbon dioxide from a flue gas stream is energy intensive.
In a cement plant, two-thirds of the CO2 emissions are a result of the fundamental chemical process of converting limestone to lime, while one-third are related to the fuel required to heat the kiln. CO2 from these sources is mixed together in the exhaust, and this CCUS process will capture 95% of the CO2 generated.
Energy consumption to power the CCUS process represents another emissions source; therefore, to achieve maximum emission reductions, the Edmonton plant’s CCUS equipment will also remove CO2 from the CHP exhaust, achieving the same 95% removal rate.
Dual Mode
The facility is dual mode and in the event of kiln outages, the CCUS will remain operational, treating only the exhaust gas from CHP. When the kiln is in operation, 3,900 tons of CO2 per day will be captured; when only the CHP is operating, that number is 1,400 tons per day, representing an increased capture percentage of 98%. Altogether, approximately 1 million tons of CO2 will be removed annually.
Further efforts being taken at the Edmonton facility for reducing CO2 emissions include replacing some of the clinker (the product made in the kiln that is responsible for high CO2 emissions) with supplementary cementitious materials (SCMs), such as coal fly ash or blast furnace slag. SCMs are byproducts of other industrial processes and incorporating them into cement does not entail any new CO2 emissions.
“Process emissions associated with the production of clinker – without application of CCUS – are considered ‘irreducible,’” said van de Wetering, “so a solution is to reduce the clinker content in cement. At Edmonton, we can reduce clinker content to as low as 67% when using fly ash and finely ground limestone as additives.”
The steps being taken at modern cement production facilities such as the Heidelberg Materials’ Edmonton plant are ones that will lead the industry toward cement that has an emission intensity of zero or less than zero.
This, in turn, will significantly contribute to the goal of net zero concrete and help the building and construction sector – a sector that currently stands as one of the major greenhouse gas emitters – reduce its carbon footprint.
Kristin Dispenza is a senior account manager for AOA Public Relations Practice Group.